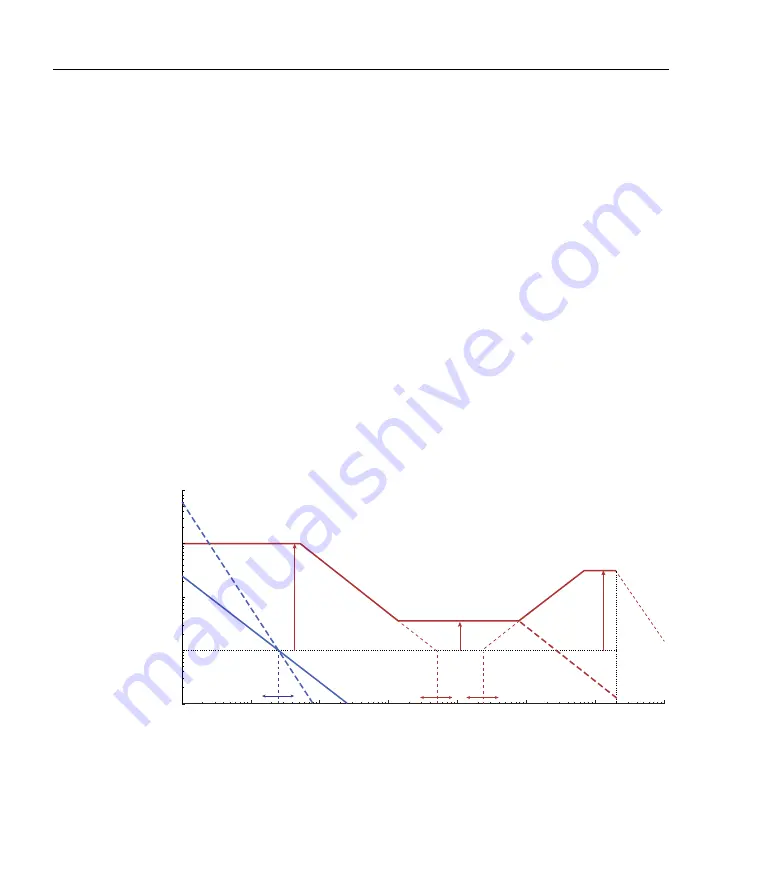
24
Chapter 3. Operation
Ideally the spectrum analyser would be used with an independent
frequency discriminator that is insensitive to laser power fluctua-
tions [11]. Good results can be achieved by monitoring the in-loop
error signal but an out-of-loop measurement is preferable, such as
measuring the cavity transmission in a PDH application. To ana-
lyse the error signal, connect the spectrum analyser to one of the
MONITOR
outputs set to “
FAST ERR
”.
High-bandwidth locking typically involves first achieving a stable
lock using only the fast servo, and then using the slow servo to
improve the long-term lock stability. The slow servo is required
to compensate for thermal drift and acoustic perturbations, which
would result in a mode-hop if compensated with current alone. In
contrast, simple locking techniques such as saturated absorption
spectroscopy are typically achieved using the slow servo, with the
fast servo compensating higher-frequency fluctuations only. It may
be beneficial to consult the Bode plot (figure 3.3) when interpreting
the error signal spectrum.
G
ain (dB)
20
0
40
60
–20
10
2
10
1
10
3
10
4
10
5
10
6
10
7
Fourier frequency [Hz]
Inte
grato
r
Double in
teg
rat
or
Proportional
High fr
eq
. cut
off
Diff
eren
tia
tor
Inte
grato
r
10
8
FAST LF GAIN (limit)
FAST
GAIN
DIFF GAIN (limit)
FAST INT
FAST DIFF
SL
OW INT
Filt
er
Figure 3.3:
Conceptual Bode plot showing action of the fast (red) and slow
(blue) controllers. The corner frequencies and gain limits are adjusted with
the front-panel knobs as labelled.
Summary of Contents for FSC100
Page 1: ...Fast servo controller FSC100 Version 0 1 2 Rev 2 4 hardware ...
Page 4: ...ii Contents ...
Page 14: ...10 Chapter 1 Introduction ...
Page 22: ...18 Chapter 2 Connections and controls ...
Page 36: ...32 Appendix B 115 230 V conversion ...
Page 39: ......