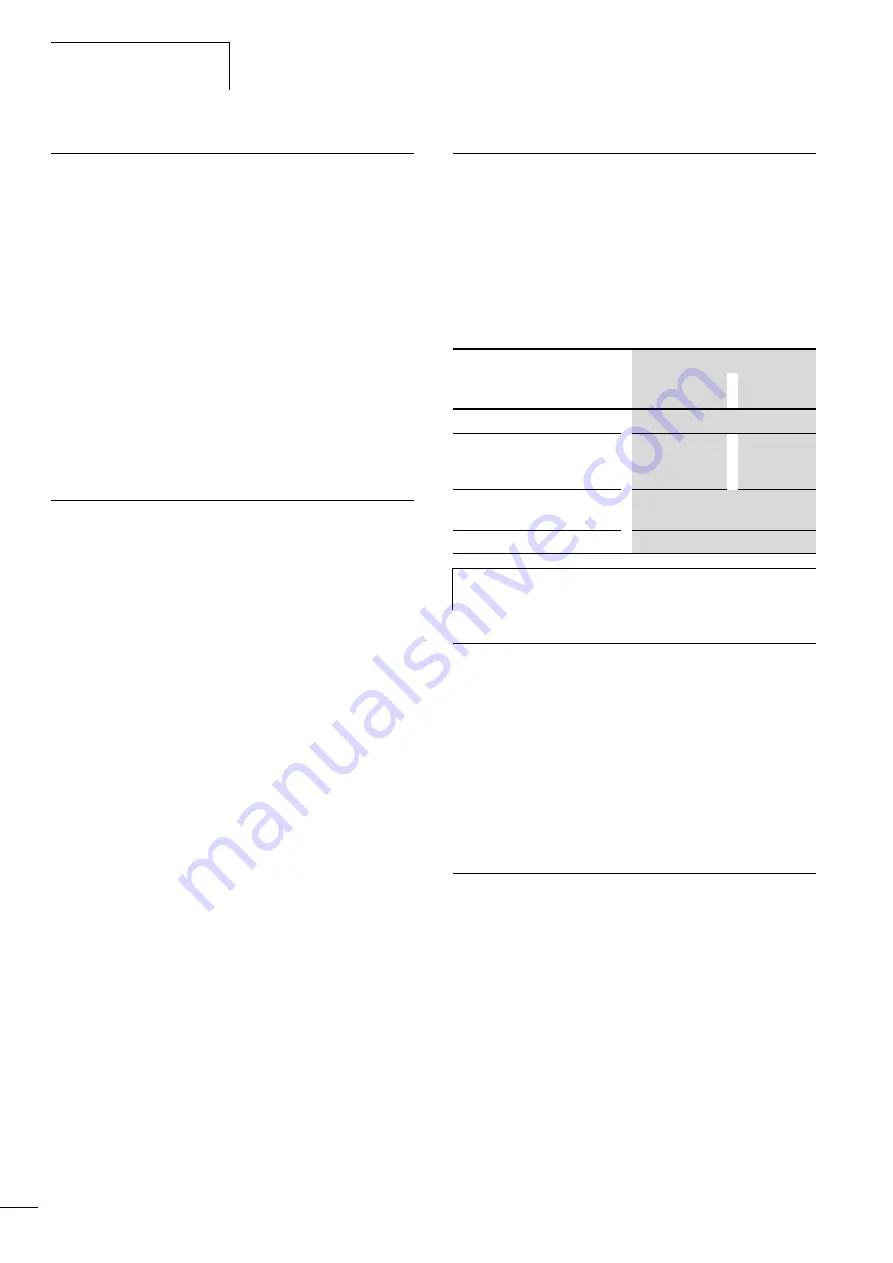
Using the XN-PLC
02/05 AWB2724-1566GB
18
Program start
When a program starts, the XN-PLC checks whether the
configured inputs and outputs match the physically present ones.
It also checks whether the actual module corresponds with the
parameterized module type. If the wrong module type is identified,
the CPU changes to NOT READY state. If no module is connected,
the start-up procedure continues.
Program start (STOP l RUN)
You can start the program in one of two ways:
• In online operation, issue the START command, for example
after loading a program. The CPU must be in STOP state and the
operating mode switch in the RUN position.
• Set the operating mode switch to its RUN position.
Behaviour after power off or power interruption
If you switch off or interrupt the CPU power while a program is
running, the program cycle or the task is interrupted immediately,
so that data integrity is no longer given. All outputs are set to 0 or
switched off.
table 6 on page 18 shows the behaviour of retentive variables.
The remaining program cycle will not be completed when power is
reconnected!
If inconsistent data is not acceptable in your application, you can,
for example, use an uninterruptible power supply (UPS).
The PLC restarts as defined by the settings in the
PLC
Configuration
window,
Program stop (RUN l STOP)
When you set the operating mode switch to STOP, the CPU
changes to STOP state, as soon as the program cycle is completed.
The outputs are set to 0.
You can stop the program in one of two ways:
• In online operation, issue the STOP command.
• Set the operating mode switch to its STOP position.
Table 6:
Behaviour of the variables at PLC start
Program processing and system time
The user program is processed cyclically. The states of the inputs
are read before the start of each program cycle, and the output
states are written to the outputs at the end of the cycle.
The run-time system’s software architecture can cause timing jitter
between individual processing cycles.
You can also program application routines that are started by the
occurrence of system events;
Monitoring cycle time
A hardware timer monitors the cycles of the user program and the
individual event tasks. If the cycle time exceeds a user-defined
value, the PLC goes into STOP state and the outputs are switched
off.
You can specify the timeout value on the
Other Parameters
tab
in the
PLC Configuration
window between 20 ms (default value)
and 1000 ms.
Start-up condition
Variable type
Non-retentive
Retentive
COLDSTART
Initial values are loaded
WARMSTART
Initial values are
loaded
Values
remain in
memory
Program loaded and started in
online operation
Initial values are loaded
Start/Stop/Start...
Values remain in memory
h
You can not declare physical operands, such as I, Q and
M, as retentive variables.
Summary of Contents for XION-PLC-CANopen
Page 4: ...2 ...
Page 8: ...02 05 AWB2724 1566D 4 ...
Page 10: ...02 05 AWB2724 1566GB 6 ...
Page 16: ...02 05 AWB2724 1566GB 12 ...
Page 18: ...02 05 AWB2724 1566GB 14 ...
Page 34: ...02 05 AWB2724 1566GB 30 ...
Page 38: ...02 05 AWB2724 1566GB 34 ...
Page 42: ...02 05 AWB2724 1566GB 38 ...
Page 48: ...02 05 AWB2724 1566GB 44 ...
Page 49: ...02 05 AWB2724 1566GB 45 Appendix Dimensions 113 25 114 75 50 6 74 4 ...