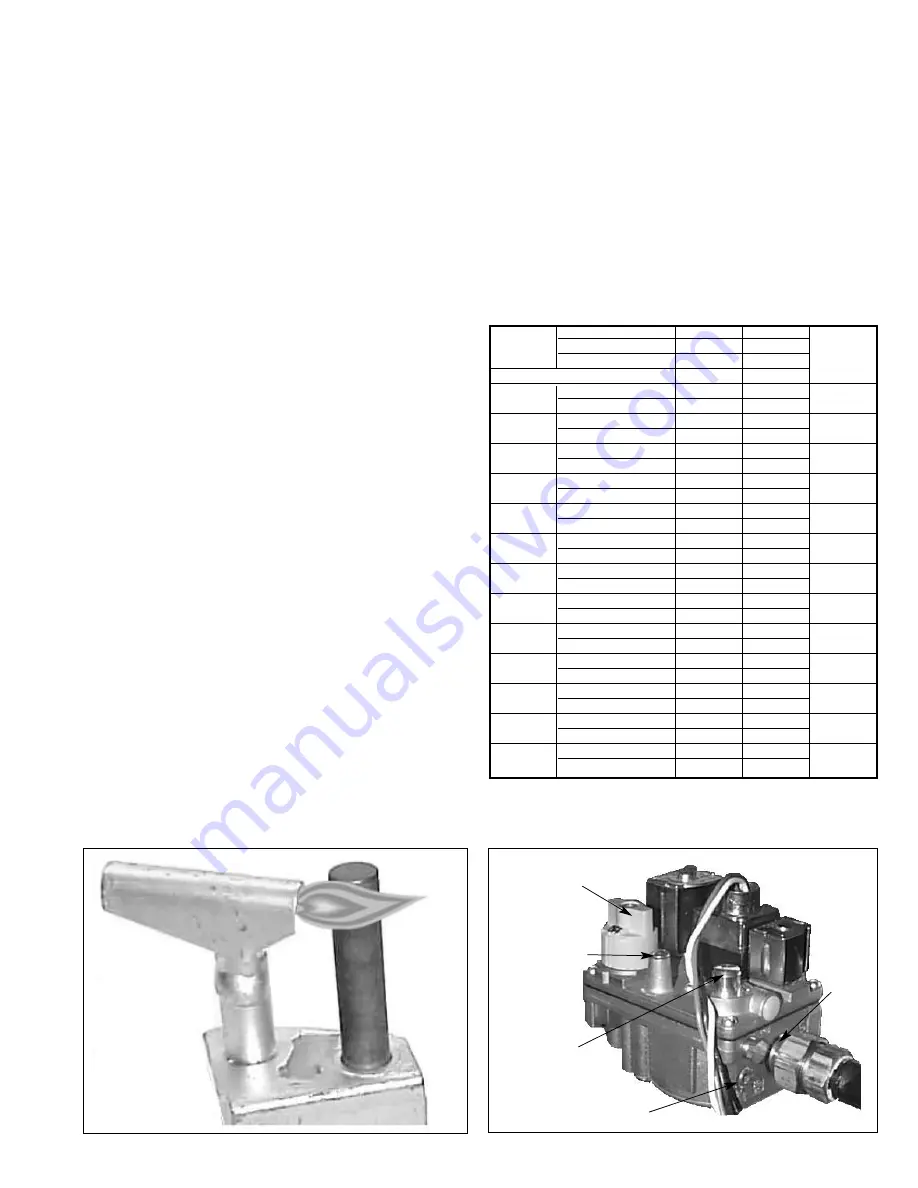
7
START-UP PROCEDURE
Pilot Flame Adjustment (Intermittent Pilot and
Millivolt Standing Pilot control systems – Control
Codes 04, 08, 27, and 67
The pilot burner is orificed to burn properly with an inlet
pressure of 7-14" W.C. on natural gas and 11-14" W.C. on
propane gas, but final adjustment must be made after
installation. If the pilot flame is too long or large, it is possible
that it may cause soot on the burner assembly. If the pilot flame
is shorter than shown, it may cause poor ignition and result in
the controls not opening the combination gas control. A dirty
pilot orifice may cause a short flame. Pilot flame condition
should be observed periodically to assure trouble-free
operation.
To adjust the pilot flame:
1. Create a call for heat from the thermostat.
2. Remove the cap from the pilot adjustment screw. For
location, see the combination gas control literature supplied
with unit.
3. Adjust the pilot flame length by turning the screw in or out
to achieve a soft steady flame 3/4" to 1" long and
encompassing 3/8"-1/2" of the tip of the flame sensing rod
or power-pile (See Figure 7.1).
4. Replace the cap from the pilot adjustment screw.
Main Burner Adjustment
The gas pressure regulator (integral to the combination gas
control) is adjusted at the factory for average gas conditions.
It is important that gas be supplied to the heater in accordance
with the input rating on the serial plate. Actual input should be
checked and necessary adjustments made after the heater is
installed. Over-firing, a result of too high an input, reduces the life
of the appliance and increases maintenance. Under no
circumstances should the input exceed that shown on the serial
plate.
Measuring the manifold pressure is done at the test port on the
main gas valve on the unit (See Figure 7.2).
To adjust the manifold pressure:
1. The correct manifold pressure is 6" W.C. for natural gas
and 10" W.C. for propane gas. Adjust the main gas
pressure regulator spring to achieve the proper manifold
pressure (see Figure 7.2).
2. Move the field installed manual shut-off valve to the “OFF”
position.
3. Remove the 1/8" pipe plug in the gas valve adjacent to the
manifold and attach a water manometer of “U” tube type
that is at least 12" high.
4. Move the field installed manual shut-off valve to the “ON”
position.
5. Create a call for heat from the thermostat.
6. After adjustment, move the field installed manual shut-off
valve to the “OFF” position and replace the 1/8" pipe plug.
7. After the plug is in place, move the field installed manual
shut-off valve to the “ON” position and recheck pipe plugs
for gas leaks with a soap solution.
Figure 7.1
Correct Pilot Flame (Millivolt Powerpile shown)
Figure 7.2
Gas Valve Features
Pilot Adjustment
Screw (Under Cap)
Regulator Adjustment
Screw (Under Cap)
Plugged Outlet
Pressure Tap
Pilot Line
Connectio
n
Control
Knob
Type of Gas
Natural
Propane
Model
Btu/Ft.
3
1040
2500
No. of
Size
Specific Gravity
0.60
1.53
Orifices
Manifold Pressure In. W.C.
6.0
10
MT-28
cfh
26.4
-
1
Orifice Drill Size
#43
-
MT-30
cfh
28.8
12.0
1
Orifice Drill Size
#42
#52
MT-33
cfh
32.2
-
1
Orifice Drill Size
#41
-
MT-56
cfh
52.9
-
2
Orifice Drill Size
#43
-
MT-60
cfh
57.7
24.0
2
Orifice Drill Size
#42
#52
MT-66
cfh
64.4
-
2
Orifice Drill Size
#41
-
MT-84
cfh
79.3
-
3
Orifice Drill Size
#43
-
MT-90
cfh
86.5
36.0
3
Orifice Drill Size
#42
#52
MT-99
cfh
96.6
-
3
Orifice Drill Size
#41
-
MT-112
cfh
105.8
-
4
Orifice Drill Size
#43
-
MT-120
cfh
115.4
48.0
4
Orifice Drill Size
#42
#52
MT-132
cfh
128.8
-
4
Orifice Drill Size
#41
-
MT-160
cfh
153.8
64.0
4
Orifice Drill Size
#38
#49
Table 7.1
Manifold Pressure and Gas Consumption