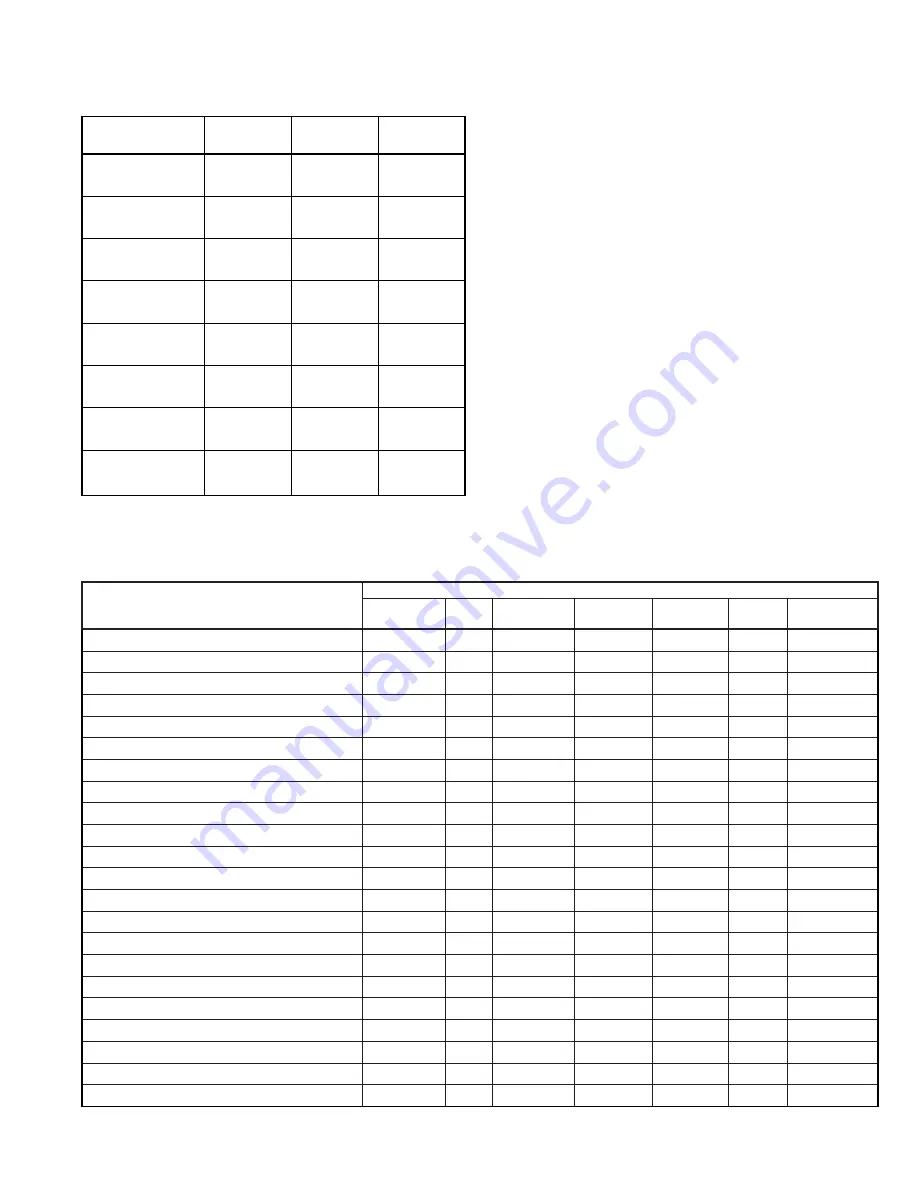
17
GEO16-501.4
START-UP PROCEDURE
Table 17.1 - Compressor Winding Resistance (Ohms)
Table 17.2 - Refrigerant Circuit Malfunctions and Probable Causes
➀
The following chart will assist in troubleshooting and diagnosing causes of a problematic unit. The chart provides general guidance
for system measurements relative to typical operating conditions.
Cause
Symptom
Head Press.
Suct.
Press.
Comp Amp
Draw
Superheat
Subcool
Air Temp
Diff.
Water (Source)
Temp Diff
Undercharged System
Low
Low
Low
High
Low
Low
Low
Overcharged System
High
High
High
Normal
High
Normal
Normal
Low Air Flow / Load Water Flow - Heating
High
High
High
High
Low
High
Low / Normal
Low Air Flow / Load Water Flow - Cooling
Low
Low
Low
Low / Normal
High
High
Low / Normal
Low Source Water Flow - Heating
Low
Low
Low
Low
High
Low
High
Low Source Water Flow - Cooling
High
High
High
High
Low
Low
High
High Air Flow / Load Water Flow - Heating
Low
Low
Low
Low
High
Low
Normal / High
High Air Flow / Load Water Flow - Cooling
Normal / High High Normal / High
High
Low
Low
Normal / High
High Source Water Flow - Heating
Normal / High High Normal / High
High
Low / Normal
High
Low
High Source Water Flow - Cooling
Low
Low
Low
Low
High
High
Low
Low Indoor Air / Load Water Temp - Heating
Low
Low
Low
Low / Normal
High
High
Normal / High
Low Indoor Air /Load Water Temp - Cooling
Low
Low
Low
Low / Normal
High
Low
Low
High Indoor Air / Load Water Temp - Heating
High
High
High
Normal / High Low / Normal
Low
Low
High Indoor Air / Load Water Temp - Cooling
High
High
High
High
Low
Low
High
Restricted TXV
High
Low
Low / Normal
High
High
Low
Low
TXV Bulb Failure (Loss of Charge)
Normal
Low
Normal
High
High
Low
Low
Restricted Filter/Drier
1
High
Low
Low / Normal
High
High
Low
Low
Inefficient Compressor
Low
High
Low
High
High
Low
Low
Scaled / Fouled Load Heat Exchanger - Heating
High
High
High
High
Low
Low
Low
Scaled / Fouled Load Heat Exchanger - Cooling
Low
Low
Low
Low / Normal
High
Low
Low
Scaled / Fouled Source Heat Exchanger - Heating
Low
Low
Low
Low / Normal
High
Low
Low
Scaled / Fouled Source Heat Exchanger - Cooling
High
High
High
High
Low
Low
Low
➀
Restricted filter / drier will have symptoms similar to restricted TXV. Check temperature drop across filter drier to verify a restriction.
Compressor
C to S
C to R
S to R
ZPS20K5E-PFV
1.64
1.30
2.94
ZPS26K5E -PFV
1.91
1.02
2.93
ZPS30K5E -PFV
1.52
0.89
2.40
ZPS35K5E -PFV
1.55
0.62
2.17
ZPS40K5E-PFV
1.87
0.52
2.38
ZPS49K5E-PFV
1.67
0.42
2.09
ZPS51K5E-PFV
1.67
0.42
2.09
ZPS60K5E-PFV
1.91
0.36
2.27