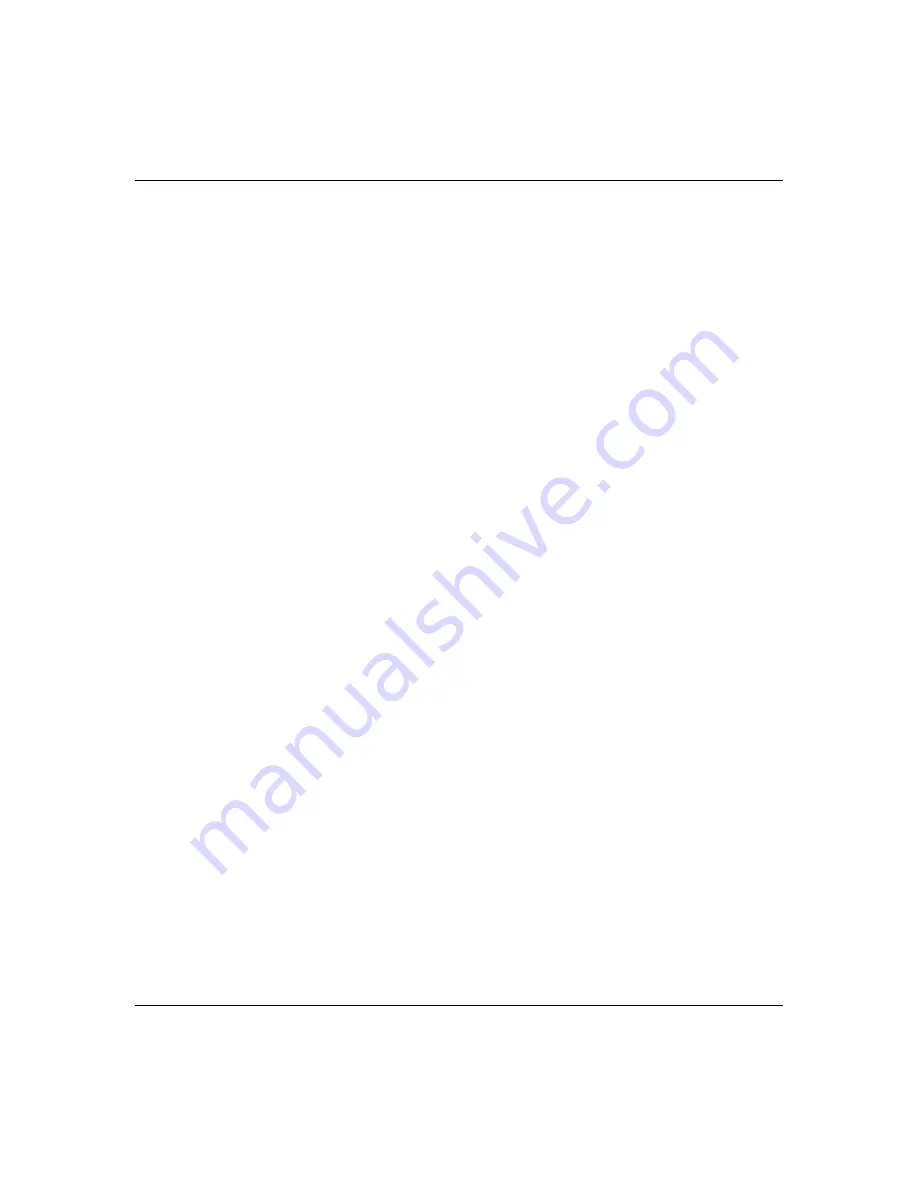
Description
Series 203 Variable Leak Valve Installation and Operating Instructions
3
3
Description
The Variable Leak consists of the Leak Valve, Driver Assembly and the
Mounting Bracket. The Leak Valve has a precisely machined 304 SS
nosepiece welded in the center of a thin 304 SS diaphragm. The diaphragm
is welded to the 304 SS body. The nosepiece seats on a carefully
proportioned pure silver gasket in the valve body.
The removable Driver Assembly actuates the nosepiece, changing the
effective aperture and thus changing the conductance. A high-ratio worm
and gear make it possible to accurately set any conductance value within
the operating range. The counter attached to the driver provides a
convenient method of reproducing approximate leak rates.
3.1 Conductance
The conductance of the Variable Leak is continuously variable from 400 cc
per second to 10-10 cc per second. When sealed, the leakage conductance
with one atmosphere across the seal is less than 10-10 standard cc per
second. All metal-to-metal seals suffer from hysteresis, especially at very
low flow rate. Hence, at low flow rates the conductance will, in general, be
higher at a given counter reading when the leak is being opened than at the
same counter reading when the leak is being closed.
If the leak is sealed after use at high flow rates, some gas will continue to
emerge from the seal for several minutes, even though the seal is mass
spectrometer leak tight. This is a normal condition with metal-to-metal
seals.
3.2 Throughput
The maximum throughput is 400 standard cc per second with atmospheric
pressure on the inlet. Larger throughputs are attained with higher inlet
pressures. Much lower throughputs may be achieved by reducing the inlet
pressure. Low inlet pressures are advantageous where very low flow rates
are required.
3.3 Maximum Inlet Pressures
The maximum inlet pressure depends on how the valve is connected to the
system. For inlet pressures less than one atmosphere either port may be
connected to the gas source. For gas pressures greater than one atmosphere
the gas source must be connected to the center port, to prevent damage to
the valve diaphragm. Inlet pressure should never exceed 200 psig.
3.4 Gases Controlled
All dry gases, non-corrosive to Leak Valve materials, can be controlled.
Moist gases, such as undried atmosphere or gases containing oil or other
condensable gases, are difficult to control because a liquid film forms
quickly on the sealing surfaces. This produces a liquid seal which has only
ON or OFF properties. If this condition occurs, a brief vacuum bakeout is
usually sufficient to restore the control properties of the metal-to-metal seal.
3.5 Materials
304 Stainless Steel and fine silver are the only materials in contact with
vacuum in all Leak Valves. All fabrication is by heliarc welding.
Summary of Contents for Granville-Phillips 203 Series
Page 2: ......
Page 4: ......
Page 6: ...ii Series 203 Variable Leak Valve Installation and Operating Instructions...
Page 15: ......