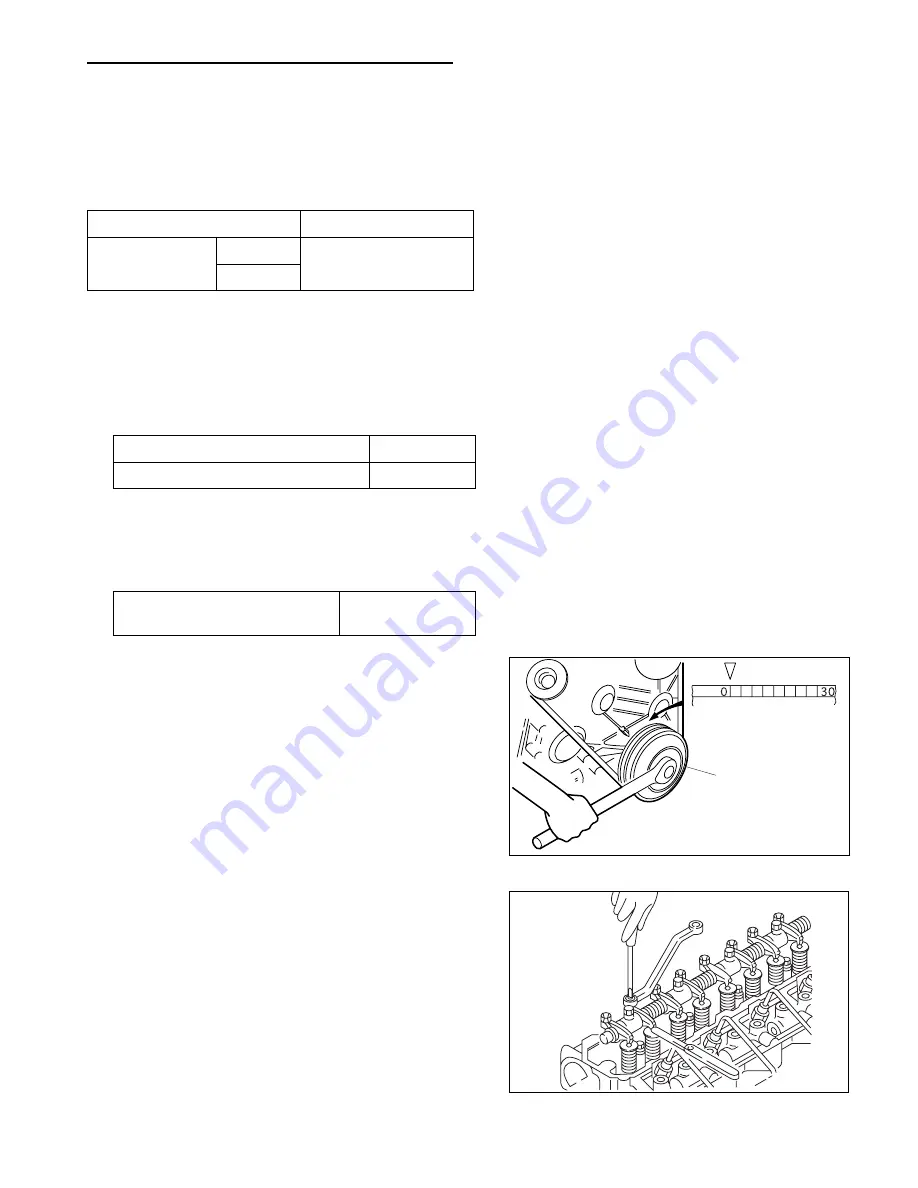
5-1
ADJUSTMENTS, BENCH TEST, PERFORMANCE TESTS
1.
Adjustments
1.1 Valve Clearance
Valve clearance should be inspected and adjusted when the
engine is cold.
(1) Inspection
(a) Inspect the valve clearance in the injection
sequence. To check, turn the crankshaft by the
specified crank angle in the normal direction to
bring the piston to the top dead center of the
compression stroke.
(b) Put socket (58309 - 73100) and ratchet handle on the
crankshaft pulley nut and turn the crankshaft in the
normal direction (clockwise as seen from the front
end).
(c) The top dead center on compression stroke of No.1
piston is identified by the timing mark “
0
” on the
crankshaft pulley and aligned with the pointer on the
gear case. With the piston so positioned, both the
inlet and exhaust valve rocker arms are not being
pushed up by their pushrods.
(d) Insert a feeler gauge in between the rocker arm and
valve cap, and check the clearance.
(2) Adjusting
(a) Loosen the lock nut of the adjusting screw. Adjust
the clearance by turning the screw in either direction
to the extent that the gauge is slightly gripped
between the rocker arm and valve cap.
(b) After adjusting the clearance, tighten the lock nut.
Inspect the clearance again and make sure that it is
correct.
Injection sequence
Crank angle
1 – 5 – 3 – 6 – 2 – 4
120°
Crankshaft pulley
Checking valve clearance (turning)
Item
Assembly Standard
Valve clearance
Inlet
0.25 mm (0.0098 in.)
(cold setting)
Exhaust
Width across flats of crankshaft
46 mm (1.81 in.)
pulley nut
Adjusting valve clearance