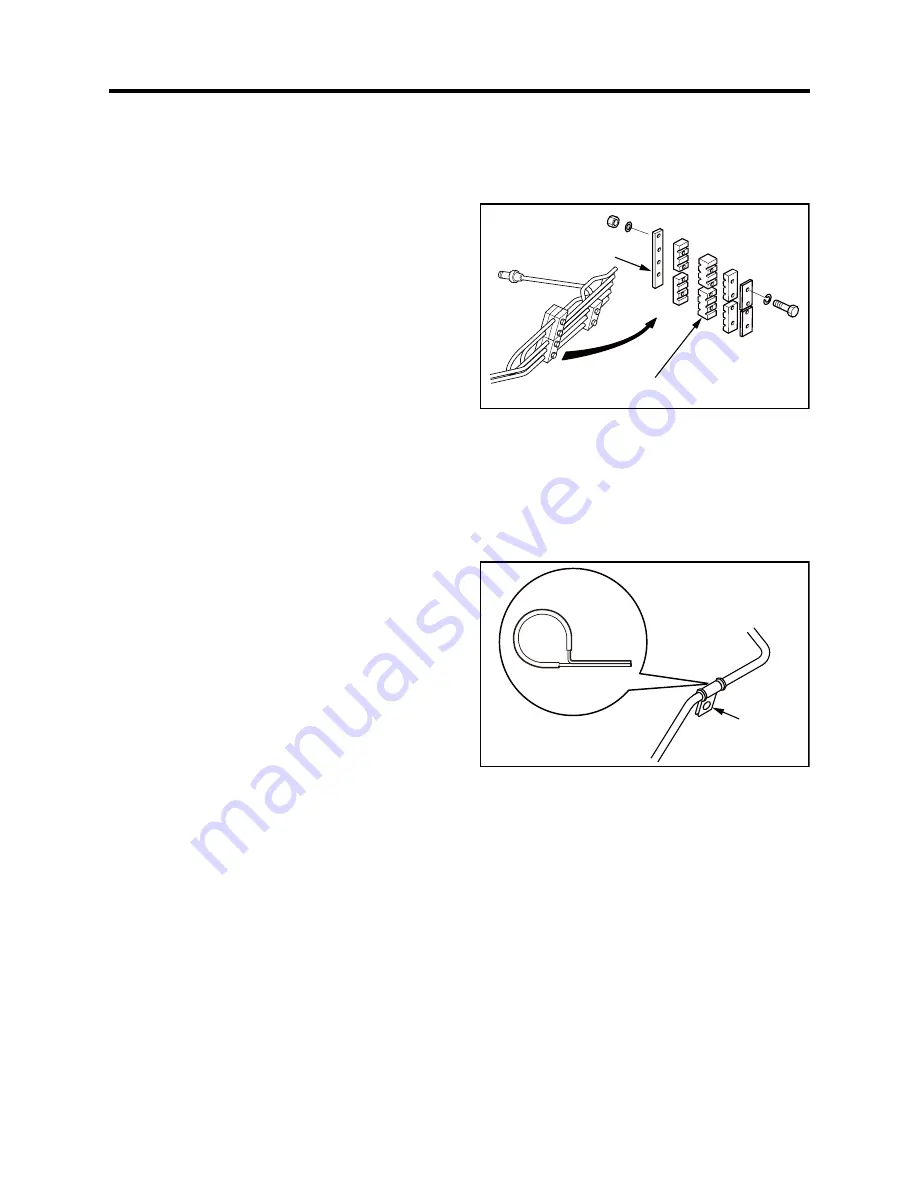
8-12
Chapter 8 PERIODIC INSPECTION AND MAINTENANCE PROCEDURES
Fuel Pipe - Inspect
High Pressure Fuel Injection Pipe and Clamp Seat - Inspect and Replace
Visual Inspection
Check clamp seat for cracks and wear. Check high
pressure fuel injection pipe for wear. If defective,
replace the clamp seat with a new one. Replace the
high pressure fuel injection pipe with a new one if
needed.
During Every Major Overhaul
Replace clamp seat with a new one. Also, check high
pressure fuel injection pipe for wear. If defective,
replace the high pressure fuel injection pipe with a
new one.
During Every Other Major Overhaul
Replace all high pressure fuel injection pipes with new
ones.
Fig. 8-13 High Pressure Fuel Injection Pipe and
Clamp Seat - Inspect and Replace
Low Pressure Fuel Pipe and Clip - Inspect
Visual Inspection During Overhaul
Loosen clamp retaining bolts and check for clip wear
and metal contact between pipe and clamp. If defec-
tive, replace the pipe assembly with a new one.
During Every Other Major Overhaul
Replace the pipe assembly with a new one.
Fig. 8-14 Low Pressure Fuel Pipe and Clip - Inspect
Clamp plate
Clamp seat
Clamp