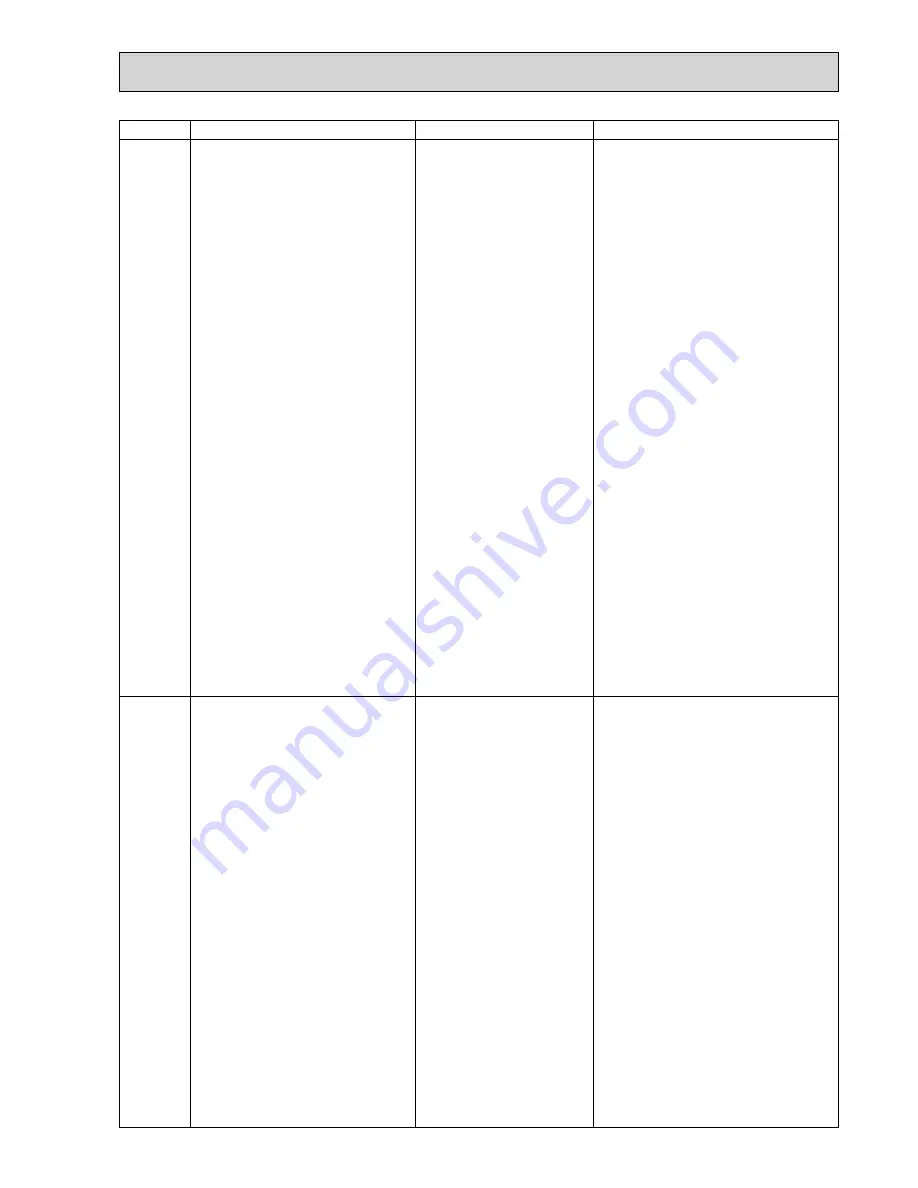
17
Error Code
Abnormal point and detection method
Cause
Countermeasure
P6
Freezing/overheating protection is work-
ing
1
Freezing protection (Cooling mode)
The unit is in 6-minute resume preven-
tion mode if pipe <liquid or condenser/
evaporator> temperature stays under
-15
:
for 3 minutes, 3 minutes after the
compressor started. Abnormal if it stays
under -15
:
for 3 minutes again within
16 minutes after 6-minute resume pre-
vention mode.
2
Overheating protection (Heating mode)
The units is in 6 minute resume
prevention mode if pipe <liquid or con-
denser/evaporator> temperature is
detected as over 70
:
after the com-
pressor started. Abnormal if the tem-
perature of over 70
:
is detected again
within 30 minutes after 6 minute resume
prevention mode.
P8
1
Slight temperature difference
between indoor room
temperature and pipe <liquid
or
condenser/evaporator>
temperature
thermistor
• Shortage of refrigerant
• Disconnected holder of pipe
<liquid or condenser/
evaporator> thermistor
• Defective refrigerant circuit
2
Converse connection of
extension pipe (on plural units
connection)
3
Converse wiring of indoor/
outdoor unit connecting wire
(on plural units connection)
4
Defective detection of indoor
room temperature and pipe
<condenser/evaporator>
temperature
thermistor
5
Stop valve is not opened
completely.
(Cooling or drying mode)
1
Clogged filter (reduced airflow)
2
Short cycle of air path
3
Low-load (low temperature)
operation out of the tolerance
range
4
Defective indoor fan motor
• Fan motor is defective.
• Indoor controller board is defec-
tive.
5
Defective outdoor fan control
6
Overcharge of refrigerant
7
Defective refrigerant circuit
(clogs)
(Heating mode)
1
Clogged filter (reduced airflow)
2
Short cycle of air path
3
Over-load (high temperature)
operation out of the tolerance
range
4
Defective indoor fan motor
• Fan motor is defective.
• Indoor controller board is defec-
tive.
5
Defective outdoor fan control
6
Overcharge of refrigerant
7
Defective refrigerant circuit
(clogs)
8
Bypass circuit of outdoor unit
is defective.
(Cooling or drying mode)
1
Check clogs of the filter.
2
Remove the blockage.
4
Refer to 10-6.
5
Check outdoor fan motor.
67
Check operating condition of refrigerant
circuit.
(Heating mode)
1
Check clogs of the filter.
2
Remove the blockage.
4
Refer to 10-6.
5
Check outdoor fan motor.
6
~
8
Check operating condition of refrigerant
circuit.
Pipe temperature
<Cooling mode>
Detected as abnormal when the pipe tem-
perature is not in the cooling range 3 min-
utes after compressor start and 6 minutes
after the liquid or condenser/evaporator
pipe is out of cooling range.
Note 1) It takes at least 9 minutes to
detect.
Note 2) Abnormality P8 is not detected in
drying mode.
Cooling range : -3 °C
]
(TH-TH1)
TH: Lower temperature between: liquid
pipe temperature (TH2) and condens-
er/evaporator temperature (TH5)
TH1: Intake temperature
<Heating mode>
When 10 seconds have passed after the
compressor starts operation and the hot
adjustment mode has finished, the unit is
detected as abnormal when condenser/
evaporator pipe temperature is not in heat-
ing range within 20 minutes.
Note 3) It takes at least 27 minutes to
detect abnormality.
Note 4) It excludes the period of defrosting.
(Detection restarts when defrosting
mode is over.)
Heating range : 3 °C
[
(TH5-TH1)
1
~
4
Check pipe <liquid or condenser/evapora-
tor> temperature with room temperature
display on remote controller and outdoor
controller circuit board.
Pipe <liquid or condenser/evaporator>
temperature display is indicated by set-
ting SW2 of outdoor controller circuit
board as follows.
23
Check converse connection of extension
pipe or converse wiring of indoor/outdoor
unit connecting wire.
Conduct temperature check with outdoor
controller circuit board after connecting
‘A-Control Service Tool (PAC-SK52ST)’.
(
)
Summary of Contents for Mr.Slim PLA-RP100BA3
Page 39: ...39...