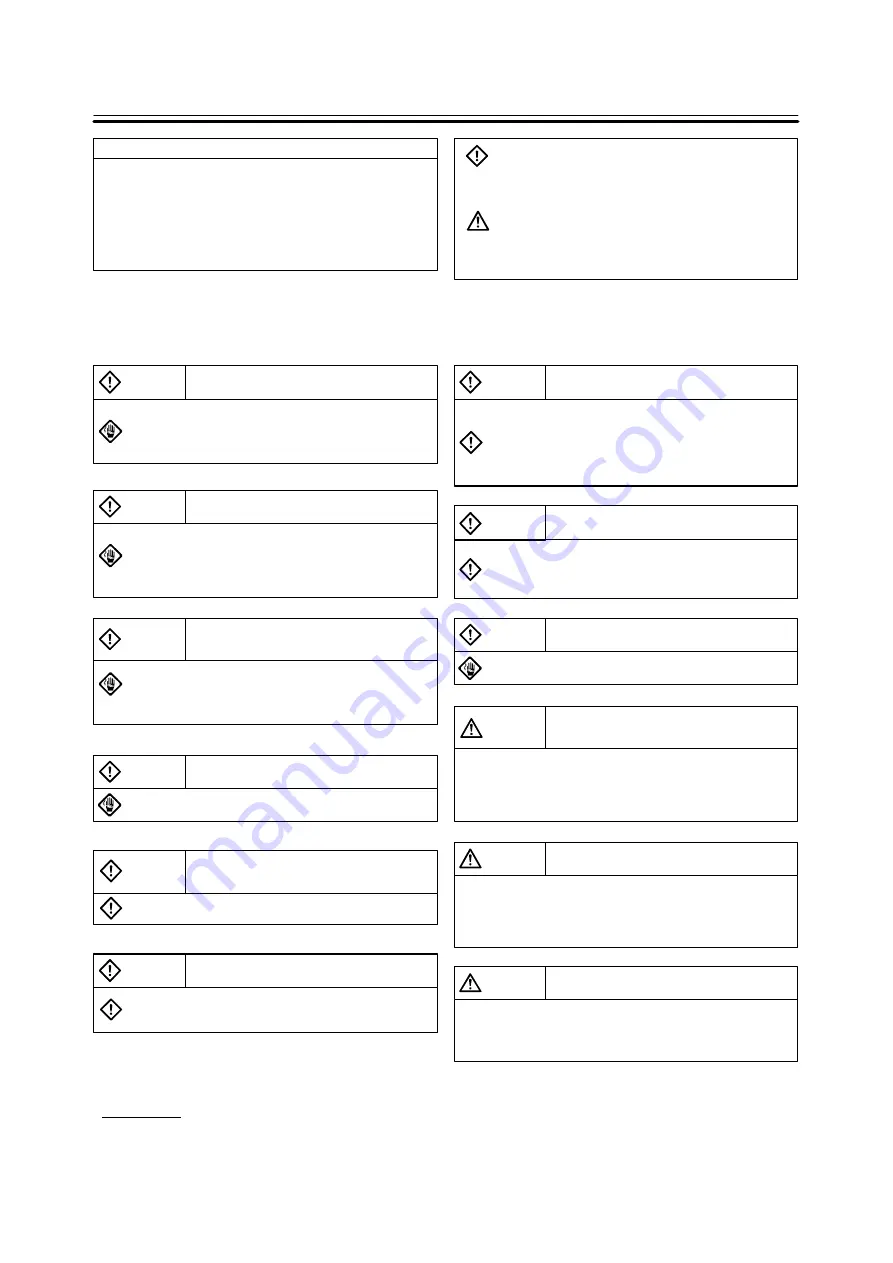
Cautions on Safety
(Make sure to read this page before using the unit .)
In this manual , cautions of safety are classified into "DANGER"
and "CAUTION".
Even an item is classified as "CAUTION", its contents are
important and it may lead to a serious result depending on the
situation. Make sure to observe every item .
DANGER:
CAUTION:
When the unit is handled incorrectly , a
dangerous situation may occur and the
possibility of death or serious injury is
expected.
When the unit is handled incorrectly , a
dangerous situation may occur and the
possibility of medium or slight injury is
expected or property damage exclusively
is expected.
CAUTION
•
We shall not be responsible for any damage caused by repair , disassembly, modification, etc. performed
by a third party other than MITSUBISHI or a company specified by MITSUBISHI .
•
The cautions on safety and the specifications described in the instruction manual are subject to change
without notice .
Never use the unit in an atmosphere where
inflammation or explosion can occur .
Otherwise, inflammation or explosion may occur .
Set up the emergency stop circuit
independently of the product .
Otherwise, the unit may become out of order and an
accident may occur when malfunction occurs in the
tension controller. Make sure to assemble the
emergency stop circuit outside the tension controller .
Do not use any unused terminals for any
external lines.
Correctly connect the AC power cable to the specified
terminal, and do not use any unused terminals for any
external lines. Improper connection may seriously
damage the product .
Never touch a switch with a wet hand .
Never touch a switch with a wet hand , otherwise,
electrical shock may occur.
Never drop cutting chips and wire chips
while screw holes are tapped and wiring
work is performed.
Damage , fume , fire, malfunction or others may be
caused in the unit .
Confirm the ambient enviroments .
Never install the unit with an enviroment where dusts , soot,
conductive dusts or corrosive gas is present or a place
exposed to high temperature , condensation or wind and
rain. Otherwise, the unit may be damaged , malfunction or
be deteriorated .
Never open the covers while the power is
supplied to the unit or when the unit is
operating.
Never supply the power to the unit nor operate the unit
while the main body cover and the terminal cover are
open. When the covers are open , a high voltage area
may be exposed and electrical shock may occur .
Turn off all the phases of the external power
supply before starting installation and wiring .
DANGER
Otherwise, electrical shock or damage in the unit may
occur. Make sure to turn off all the phases of the
external power supply before starting installation and
wiring.
Separate the wiring of the strong electric
system from the wiring of the weak electric
system.
CAUTION
Separate the wiring of the strong electric system from the
wiring of the weak electric system, and make sure that
noises are not superimposed on the wiring of the weak
electric system. Otherwise, the unit may not operate
correctly.
Never modify nor disassemble the unit
Never modify nor disassemble the unit . Otherwise, the
unit may become defective or an accident such as fire ,
damage , etc . may occur.
Design the installation plan using the wire
size suitable to the current capacity .
Use the wire size suitable to the current capacity to
supply the power to the load . If a wire having smaller
current capacity is used,the insulation sheath will be
melted and insulation will become defective . In this
situation, electrical shock or a short-circuit may occur,
and fire may occur .
To assure safety
•
Make sure the user thoroughly read this instruction manual
before using the unit , and pay attention in assuring safety
while using the unit .
•
The unit is manufactured under the severe quality control .
When a severe accident or loss is expected in the
equipment used due to failure of the unit , provide a backup
function or the fail -safe function in the system .
Perform grounding ( grounding registance
100
Ω
or less).
Otherwise, electrical shock may occur. Perform
grounding ( grounding registance 100
Ω
or less) to the
unit using a wire of 2 mm
2
or more, otherwise, electrical
shock may occur. Never share the grounding with a
strong electric system.
DANGER
DANGER
DANGER
DANGER
DANGER
DANGER
DANGER
DANGER
CAUTION
CAUTION
Summary of Contents for LE-40MTB-E
Page 2: ......
Page 4: ......
Page 79: ......
Page 80: ...JZ990D30801F TENSION CONTROLLER MODEL LE 40MTB E ...