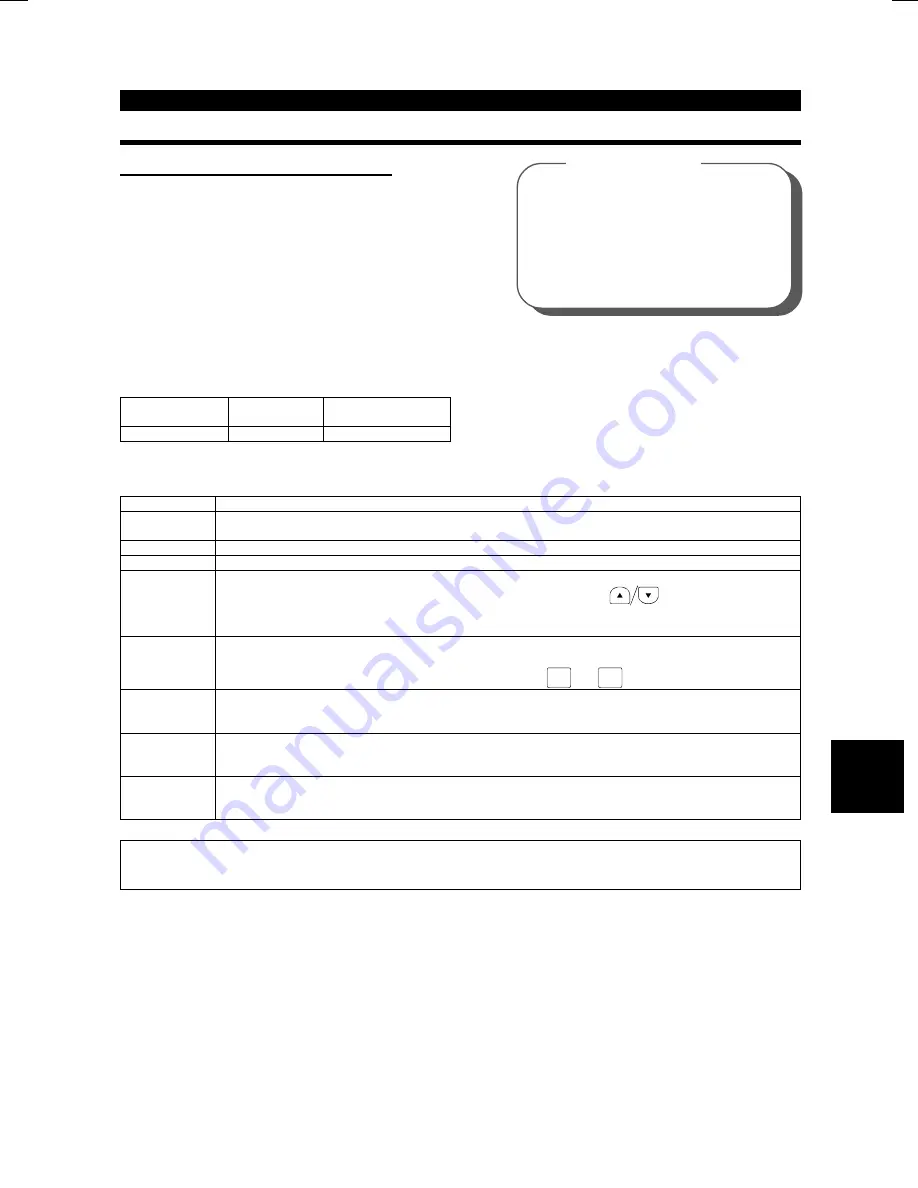
PARAMETERS
105
4.2.37 Operation mode selection (Pr. 79)
Pr. 79 "operation mode selection"
Used to select the operation mode of the inverter.
You can choose any of the operation modes: operation using external signals (external operation), operation
from the PU (FR-DU04/FR-PU04) (PU operation), combination of PU operation and external operation
(external/PU combined operation), and computer link operation (when the FR-A5NR option is used).
Parameter
Number
Factory
Setting
Setting Range
79
0
0 to 4, 6 to 8
<Setting>
Pr. 79 Setting
Function
0
External operation mode at power-on
PU or external operation can be selected.
1
PU operation mode
2
External operation mode
3
External/PU combined operation mode 1
Running frequency .....Set from the PU (FR-DU04/FR-PU04) (direct setting,
key) or external
signal input (multi-speed setting only)
Start signal .................External signal input (terminal STF, STR)
4
External/PU combined operation mode 2
Running frequency .....External signal input (terminal 2, 4, 1, jog, multi-speed selection)
Start signal .................Input from the PU (FR-DU04/FR-PU04) (
FWD
key,
REV
key)
6
Switch-over mode
Switch-over between PU operation, external operation and computer link operation (when the communication
option such as the FR-A5NR is used) modes can be done while running.
7
External operation mode (PU operation interlock)
X12 signal ON ............May be switched to PU operation mode (output stop during external operation)
X12 signal OFF ..........Switching to PU operation mode inhibited
8
Switching to other than external operation mode (disallowed during operation)
X16 signal ON ...........Switched to external operation mode
X16 signal OFF ..........Switched to PU operation mode
Note: 1. Either "3" or "4" may be set to select the PU/external combined operation. These settings differ in
starting method.
Pr. 15 "jog frequency"
Pr. 4 to Pr. 6, Pr. 24 to 27
(multi-speed operation)
Pr. 76 "alarm code output selection"
Pr. 180 to Pr. 186
(input terminal function selection)
Related parameters
4