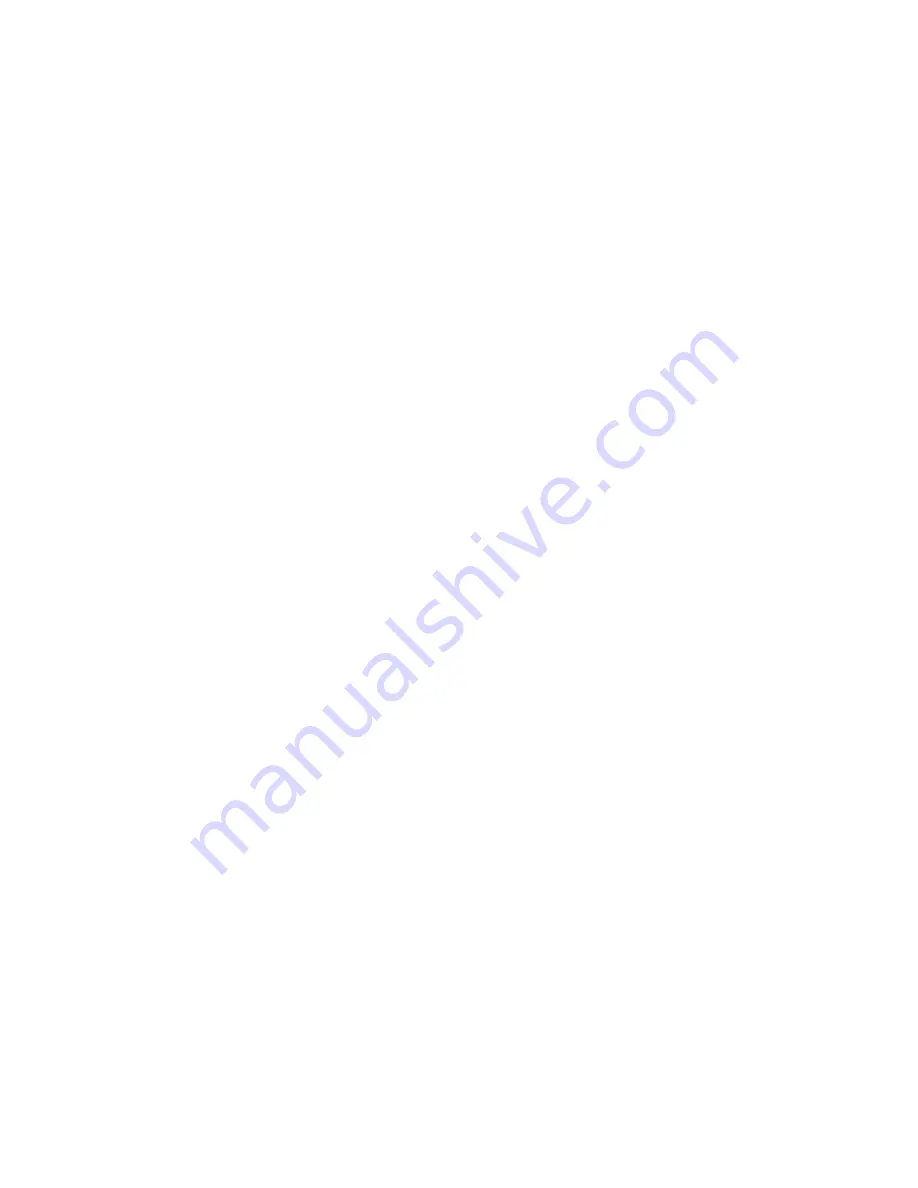
10. Always use tools that are in good condition and be
sure you understand how to use them before
performing any service work.
11. Reinstall all fasteners with same part number. Do
not use a lesser quality fastener if replacements are
necessary.
12. If possible, make all repairs with the truck parked
on a level, hard surface. Block truck so it does not
roll while working on or under truck.
13. Disconnect battery and discharge any capacitors
(electric trucks) before starting to work on truck.
Hang “Do not Operate” tag in the Operator’s
Compartment.
14. Repairs, which require welding, should be
performed only with the benefit of the appropriate
reference information and by personnel adequately
trained and knowledgeable in welding procedures.
Determine type of metal being welded and select
correct welding procedure and electrodes, rods or
wire to provide a weld metal strength equivalent at
least to that of parent metal.
15. Do not damage wiring during removal operations.
Reinstall the wiring so it is not damaged nor will it
be damaged in operation by contacting sharp
corners, or by rubbing against some object or hot
surface. Place wiring away from oil pipe.
16. Be sure all protective devices including guards and
shields are properly installed and functioning
correctly before starting a repair. If a guard or
shield must be removed to perform the repair work,
use extra caution.
17. Always support the mast and carriage to keep
carriage or attachments raised when maintenance
or repair work is performed, which requires the
mast in the raised position.
18. Loose or damaged fuel, lubricant and hydraulic
lines, tubes and hoses can cause fires. Do not bend
or strike high pressure lines or install ones which
have been bent or damaged. Inspect lines, tubes
and hoses carefully. Do not check for leaks with
your hands. Pin hole (very small) leaks can result
in a high velocity oil stream that will be invisible
close to the hose. This oil can penetrate the skin
and cause personal injury. Use cardboard or paper
to locate pin hole leaks.
19. Tighten connections to the correct torque. Make
sure that all heat shields, clamps and guards are
installed correctly to avoid excessive heat, vibration
or rubbing against other parts during operation.
Shields that protect against oil spray onto hot
exhaust components in event of a line, tube or seal
failure, must be installed correctly.
20. Relieve all pressure in air, oil or water systems
before any lines, fittings or related items are
disconnected or removed. Always make sure all
raised components are blocked correctly and be
alert for possible pressure when disconnecting any
device from a system that utilizes pressure.
21. Do not operate a truck if any rotating part is
damaged or contacts any other part during
operation. Any high speed rotating component that
has been damaged or altered should be checked for
balance before reusing.
22. When handling the parts containing asbestos, be
careful not to inhale the asbestos. Doing so is
hazardous to your health.
If the shop dust may contain asbestos, follow the
precautions described below.
a.
Do not use compressed air for cleaning.
b.
Do not brush or apply grinder on asbestos
containing materials.
c.
To clean asbestos containing materials, wipe
with moistened cloth or use a vacuum cleaner
with particle filter.
d.
If you have to handle the parts containing
asbestos for a long time, be sure to do it in a
well-ventilated area.
e.
If the asbestos in the air cannot be removed,
wear a mask.
f.
Be sure to observe the working rules and
regulations.
g.
When disposing of materials with asbestos, be
sure to observe the environmental protection
regulations of your area.
h.
Avoid working in the atmosphere where
asbestos particles may be suspended.