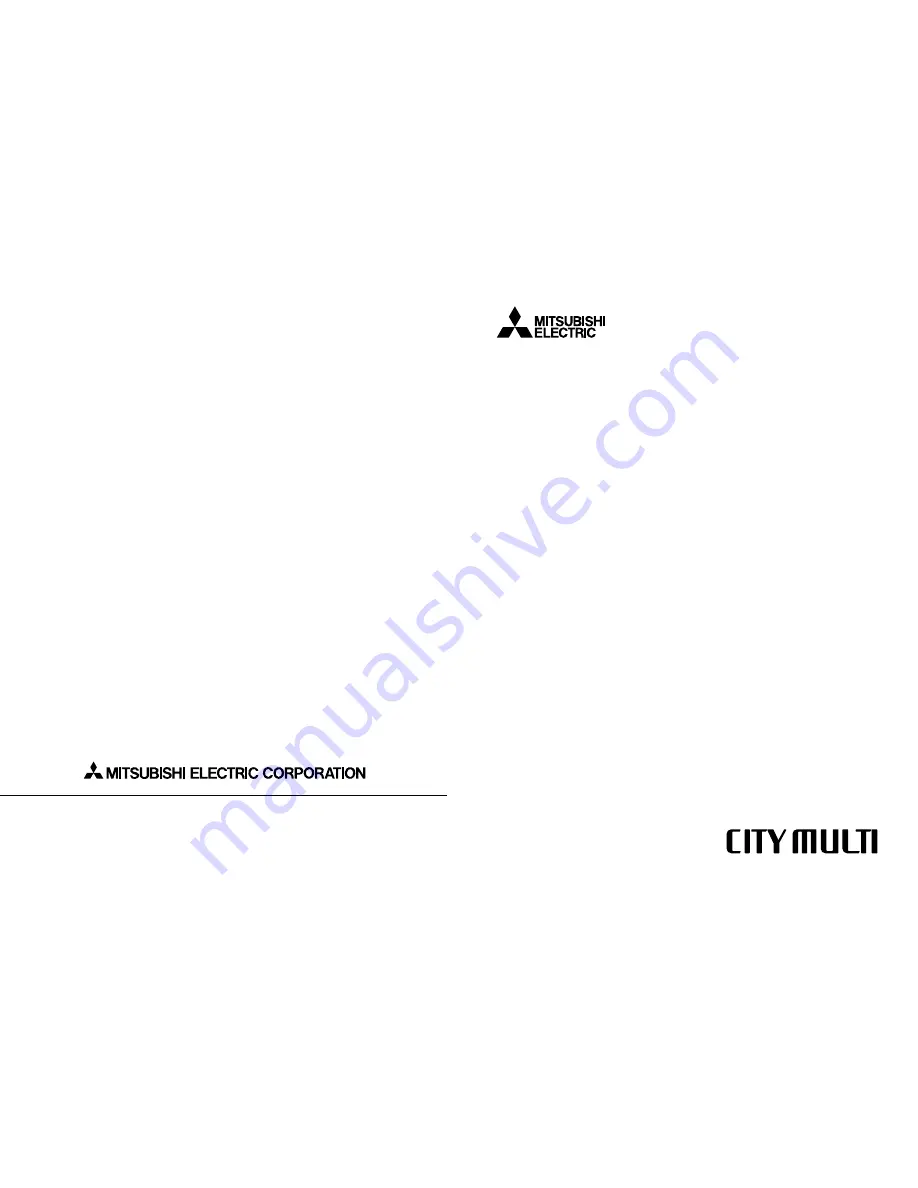
AIR CONDITIONERS CITY MULTI
Models
< Outdoor unit >
PUD-P250YMF-C
< Iutdoor unit >
PFD-P250VM-A
PFD-P500VM-A
Service Handbook
Service Handbook
PUD-P250YMF-C
PFD-P250VM-A
PFD-P500VM-A
Issued in Jun. 2004 MEE03K207-A
Printed in Japan
New publication effective Jun. 2004
Specifications subject to change without notice.
HEAD OFFICE: MITSUBISHI DENKI BLDG., 2-2-3, MARUNOUCHI, CHIYODA-KU, TOKYO 100-8310, JAPAN
Ser
vice Handbook Close Contr
ol PUD-P250YMF-C/PFD-P250,
P500VM-A