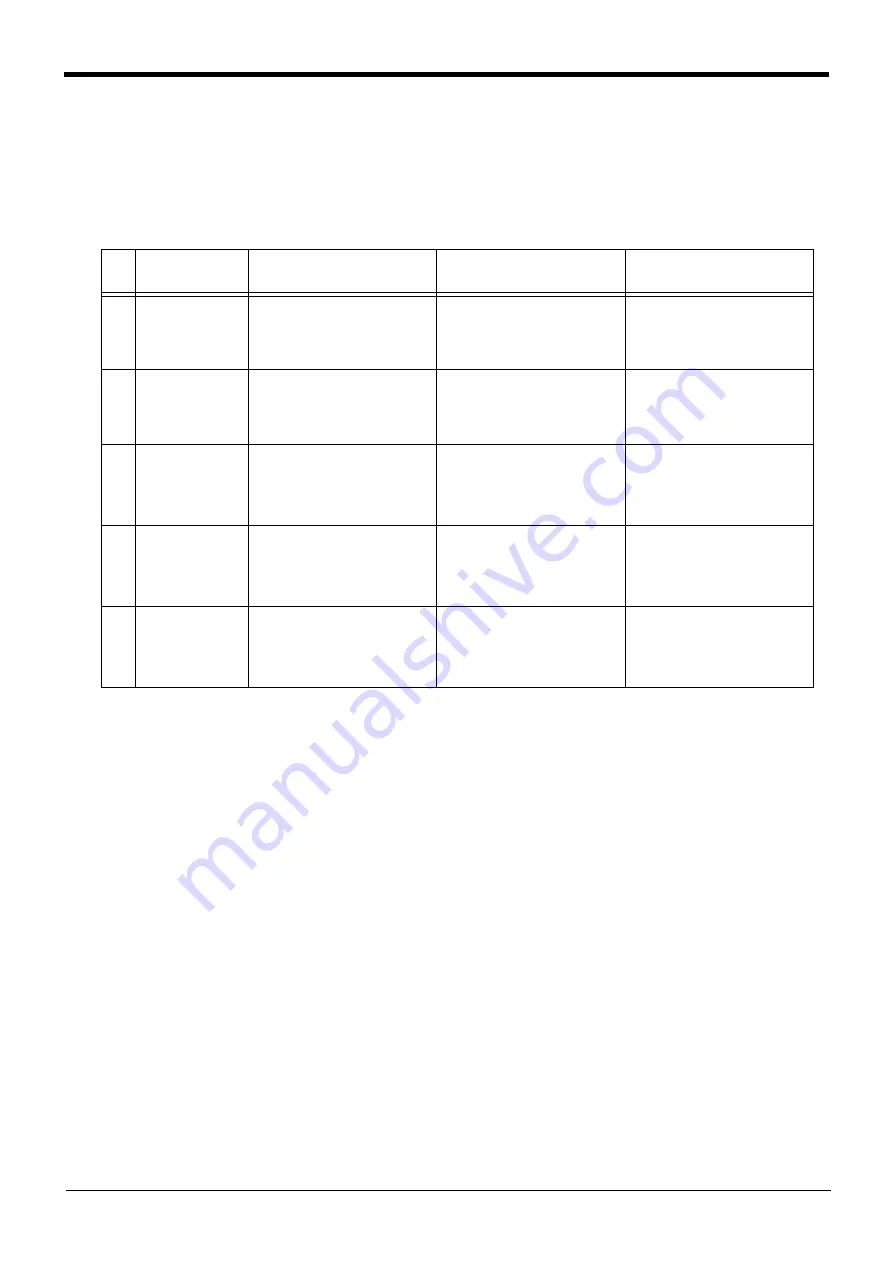
Resetting the origin
5 Maintenance and Inspection
5.6 Resetting the origin
The origin is set so that the robot can be used with a high accuracy. After purchasing the robot, always carry out
this step before starting work. The origin must be reset if the combination of robot and controller being used is
changed or if the motor is changed causing an encoder area. The origin setting methods and when each origin set
-
ting method is required are shown in
Table 5-8 : Origin setting method
[Caution]
・ The origin is set using the jig method (No.2) at factory default.
・ The value set with the jig method is encoded and used as the origin data to be input at the initial startup after
shipment. When the robot arm does not mechanically deviate (for example caused by replacement of the
reduction gear, motor, or timing belt) or does not lose the encoder data, the origin data input method at
shipment can be used to set the origin.
・ The origin data is inherent to the serial number of each robot arm.
・ The ABS origin method is used to restore the previous data by aligning the triangular marks to each other for
each axis to set the lost origin data.
(Although the setting position is confirmed visually, deviations within a half rotation of the motor can be
compensated.)
[Remarks]
・ The ABS origin method cannot be used when the robot arm mechanically deviates (for example caused by
replacement of the reduction gear, motor, or timing belt).
・After the origin setting is completed, move the robot arm to the position where the ABS marks align each other,
and check that the displayed joint coordinates of the position are correct.
For the details of the ABS mark position and the joint coordinates, refer to
Page 106, "5.6.3 ABS origin method"
No
Method
Explanation
Cases when setting the origin
is required
Remarks
1
Origin data input
method
The origin data set as the default is
input from the T/B.
Use this method at the initial
startup.
• At the initial startup
• When the controller is replaced
• When the data is lost due to flat
battery of the robot controller
(when C7500 occurs)
The setting method is explained in
Page 23, "2.3 Setting the origin"
2
Jig method
The origin posture is set with the
calibration jig installed.
• When a structural part of the
robot (motor, reduction gear,
timing belt, etc.) is replaced
•When deviation occurred by a col
-
lision.
The setting method is explained in
.
3
Mechanical stopper
method
This origin posture is set by
contacting each axis against the
mechanical stopper.
• When a structural part of the
robot (motor, reduction gear,
timing belt, etc.) is replaced
• When deviation occurred by a col
-
lision.
The accuracy is lower than that of
the jig method.
The setting method is explained in
Page 94, "5.6.1 Mechanical stopper
method"
.
4
ABS origin method
This method is used when the
encoder backup data lost in the
cause such as battery cutting.
• When the encoder data is lost due
to flat battery of the robot arm
(when H112n occurs)
Before using this method, the
origin must be set with the other
method with same encoder. The
setting method is explained in
106, "5.6.3 ABS origin method"
.
5
User origin method
A randomly designated position is
set as the origin posture.
• When an arbitrary position is set
as the origin
Before using this method, the
origin must be set with the other
method. The setting method is
explained in