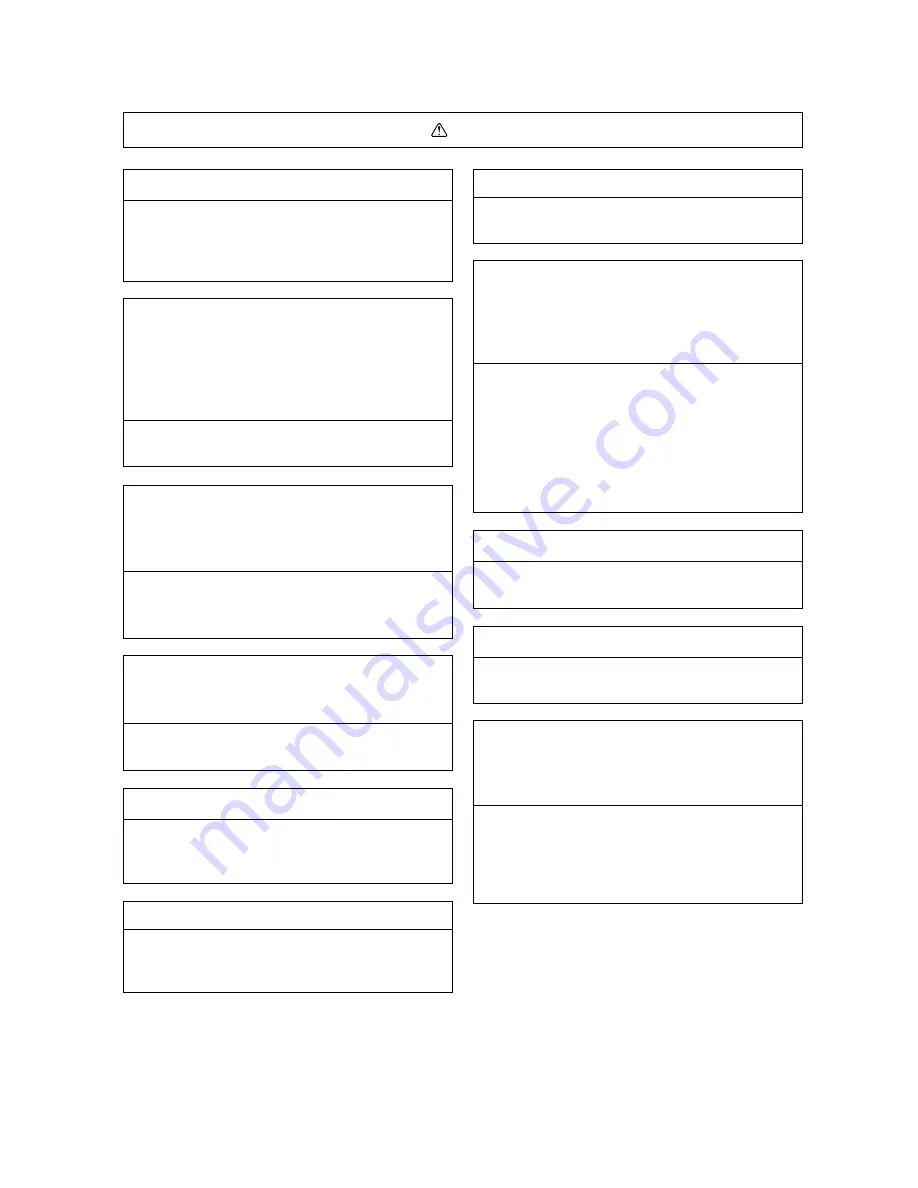
–3–
1
1
1
1
1
PRECAUTIONS FOR DEVICES THAT USE R407C REFRIGERANT
Caution
Do not use the existing refrigerant piping.
•
The old refrigerant and refrigerator oil in the existing
piping contains a large amount of chlorine which may
cause the refrigerator oil of the new unit to deterio-
rate.
Use refrigerant piping made of phosphorus deoxi-
dized copper and copper alloy seamless pipes and
tubes”. In addition, be sure that the inner and outer
surfaces of the pipes are clean and free of hazardous
sulphur, oxides, dust/dirt, shaving particles, oils,
moisture, or any other contaminant.
•
Contaminants on the inside of the refrigerant piping
may cause the refrigerant residual oil to deteriorate.
Store the piping to be used during installation indoors
and keep both ends of the piping sealed until just
before brazing. (Store elbows and other joints in a
plastic bag.)
•
If dust, dirt, or water enters the refrigerant cycle,
deterioration of the oil and compressor trouble may
result.
Use ester oil, ether oil or alkylbenzene (small
amount) as the refrigerator oil to coat flares and
flange connections.
•
The refrigerator oil will degrade if it is mixed with a
large amount of mineral oil.
Use liquid refrigerant to seal the system.
•
If gas refrigerant is used to seal the system, the com-
position of the refrigerant in the cylinder will change
and performance may drop.
Do not use a refrigerant other than R407C.
•
If another refrigerant (R22, etc.) is used, the chlorine
in the refrigerant may cause the refrigerator oil to de-
teriorate.
Use a vacuum pump with a reverse flow check valve.
•
The vacuum pump oil may flow back into the refriger-
ant cycle and cause the refrigerator oil to deteriorate.
Do not use the following tools that have been used
with conventional refrigerants.
(Gauge manifold, charge hose, gas leak detector, re-
verse flow check valve, refrigerant charge base,
vacuum gauge, refrigerant recovery equipment)
•
If the conventional refrigerant and refrigerator oil are
mixed in the R407C, the refrigerant may deterio-
rated.
•
If water is mixed in the R407C, the refrigerator oil
may deteriorate.
•
Since R407C does not contain any chlorine, gas
leak detectors for conventional refrigerants will not
react to it.
Do not use a charging cylinder.
•
Using a charging cylinder may cause the refrigerant
to deteriorate.
Be especially careful when managing the tools.
•
If dust, dirt, or water gets in the refrigerant cycle, the
refrigerant may deteriorate.
If the refrigerant leaks, recover the refrigerant in the
refrigerant cycle, then recharge the cycle with the
specified amount of the liquid refrigerant indicated
on the air conditioner.
•
Since R407C is a nonazeotropic refrigerant, if addi-
tionally charged when the refrigerant leaked, the com-
position of the refrigerant in the refrigerant cycle will
change and result in a drop in performance or abnor-
mal stopping.