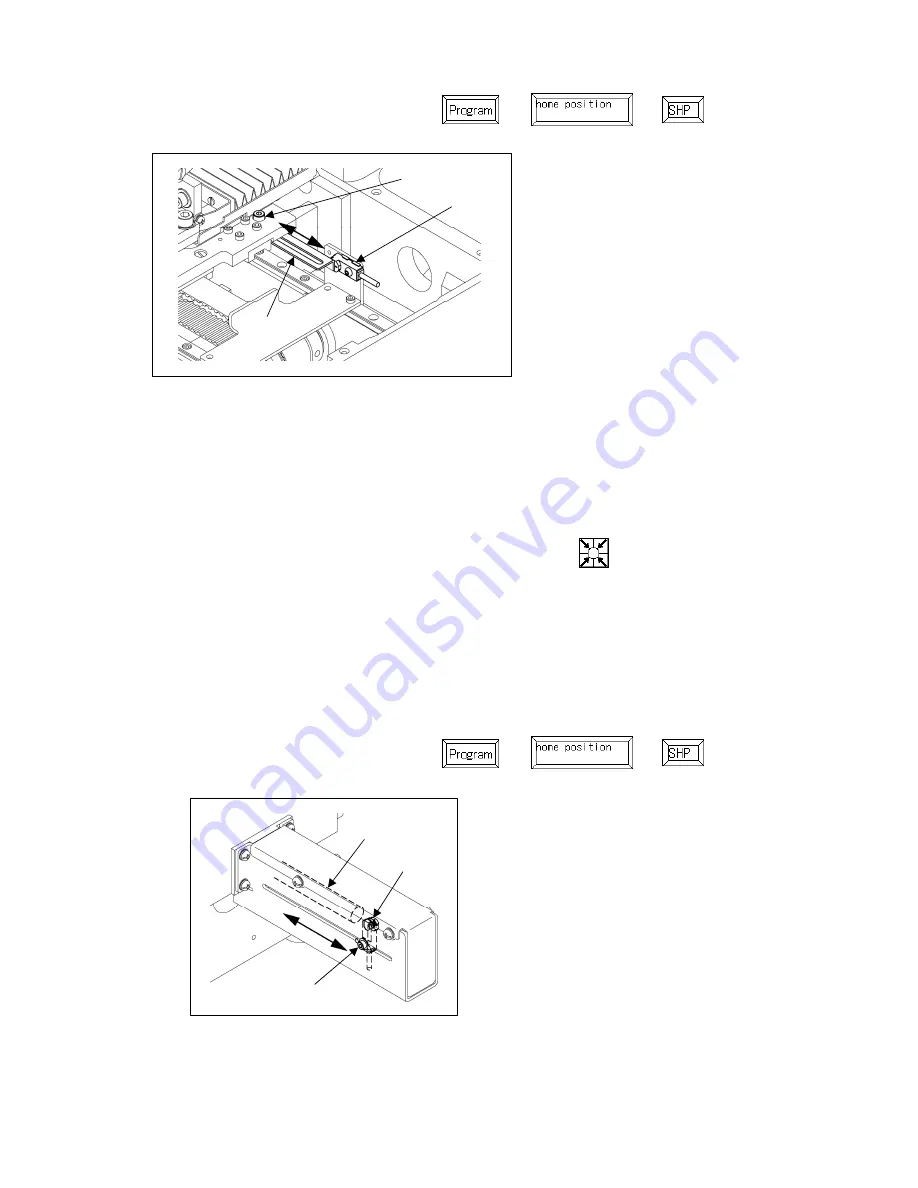
- 28 -
change the mechanical home position.
To use the sensor from the send returning, press
→
→
[Home
returning method since the second time returning] on the standard screen and set it ON.
7-21-2. Adjustment of the Y direction
(1) Turn the power switch off.
(2) The mechanical home position of the Y direction is the position where the detector (No.2) can detect
the edge of the Y drive (No.1).
(3) For the adjustment of the Y direction mechanical home position, loosen the detector set screw (No.3)
then, move the detector to the arrow direction as shown on the figure.
(4) Turn the power switch on. Press the home position return icon , and check the mechanical
home position.
(5) If the mechanical home position is not the desired position, carry out the same procedure (3) and (4)
again. In that case, turn the power switch off each time.
[Notice] The machine has a function that the motor memorizes the home position at the first home
position returning operation after the switch is turned on. Therefore, from the second home position
returning, it does not use the home position return sensor. Make sure to turn the power switch off to
change the mechanical home position.
To use the sensor from the send returning, press
→
→
[Home
returning method since the second time returning] on the standard screen and set it ON.
7-22. The X-Y drive timing belt tension
The X-Y drive timing belt tension is as follows as the factory default setting.
X : 150 (N) ± 10% Y : 150 (N) ± 10%
<1>: Detector plate X
<2>: Detector
<3>: Detector plate set screw
<1>: Y drive
<2>: Detector
<3>: Detector set screw
<3>
<2>
<1>
<2>
<1>
<3>