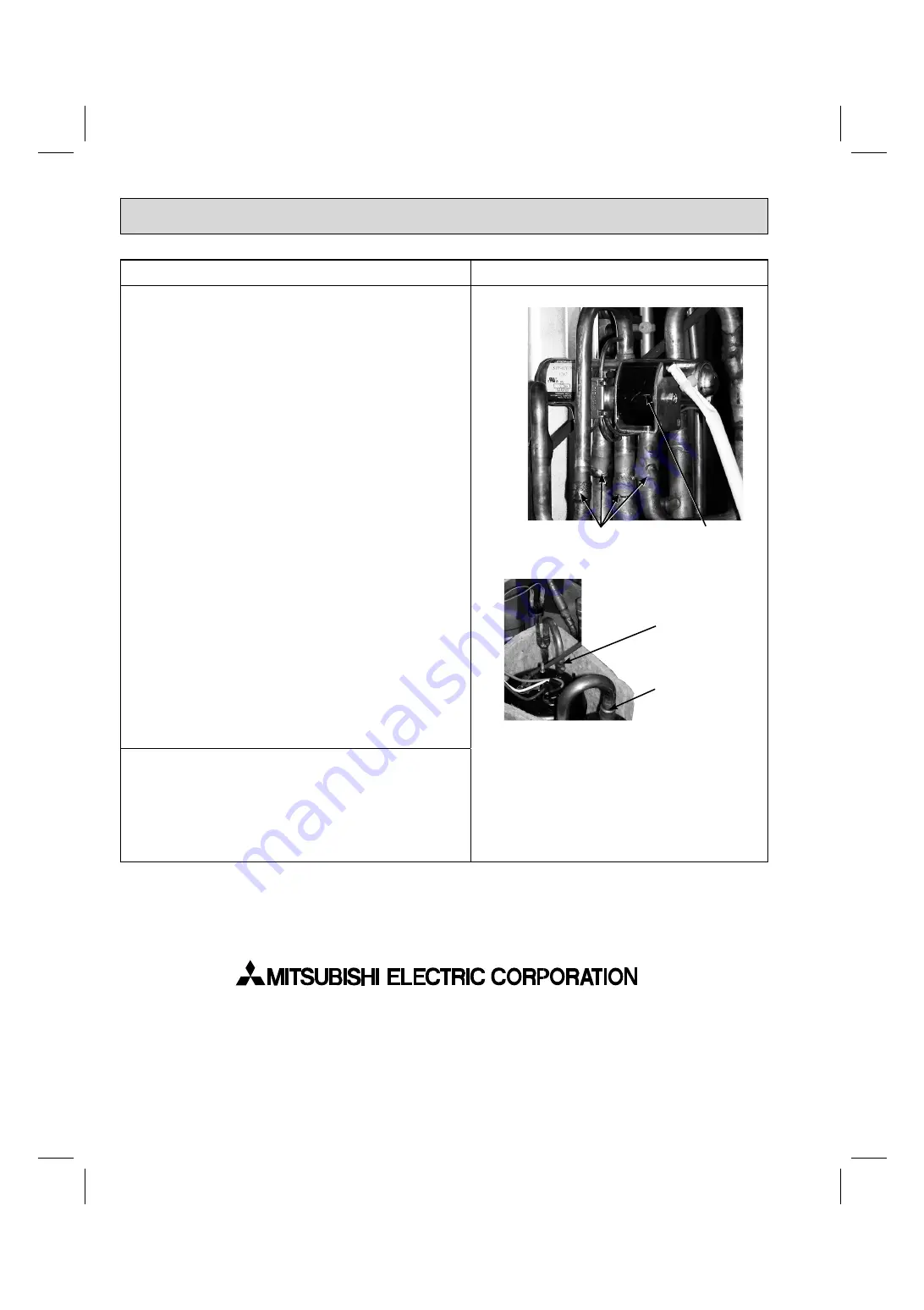
OPERATING PROCEDURE
PHOTOS
6. Removing the compressor and 4-way valve
(1) Remove the top panel, cabinet, service panel and the back
panel. (Refer to 1.)
(2) Remove the inverter assembly. (Refer to 2.)
(3) Remove the R.V. coil. (Refer to 3.)
(4) Recover gas from the refrigerant circuit.
NOTE:
Recover gas from the pipes until the pressure gauge
shows 0 PSIG.
(5) Detach the brazed part of the suction and the discharge
pipe connected with compressor.
(6) Remove the compressor nuts.
(7) Remove the compressor.
(8) Detach the brazed part of 4-way valve and pipe. (Photo 8)
7. Removing the reactor
(1) Remove the top panel, cabinet, service panel and the back
panel. (Refer to 1.)
(2) Disconnect the reactor lead wire.
(3) Remove the screws of the reactor, and remove the reactor.
Photo 9
Brazed parts of 4-way valve
R.V. coil
Photo 10
Brazed part of the
discharge pipe
Brazed part of the
suction pipe
HEAD OFFICE: TOKYO BLDG., 2-7-3, MARUNOUCHI, CHIYODA-KU, TOKYO 100-8310, JAPAN
© Copyright 2008 MITSUBISHI ELECTRIC CO.,LTD
Distributed in Jul. 2011. No. OBH502 REVISED EDITION-C
Distributed in Jan. 2009. No. OBH502 REVISED EDITION-B 5
Distributed in Mar. 2008. No. OBH502 REVISED EDITION-A 7
Distributed in Feb. 2008. No. OBH502 7
Made in Japan
New publication, effective Jul. 2011
Specifications subject to change without notice.