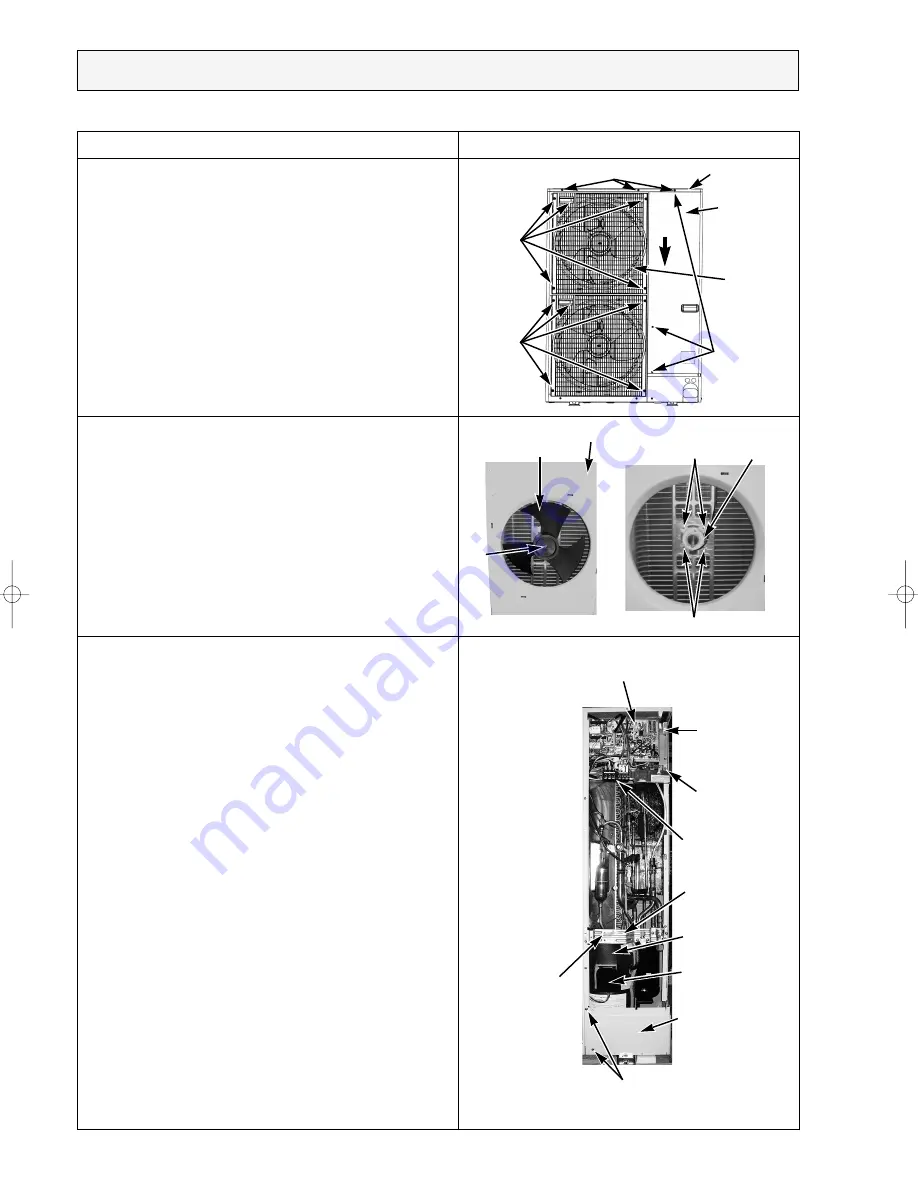
96
OPERATING PROCEDURE
PHOTOS & ILLUSTRATION
PUHZ-RP4VHA
1
PUHZ-RP5VHA
1
PUHZ-RP6VHA
1
1. Removing the service panel and top panel
(1) Remove 3 service panel fixing screws (5
✕
10) and slide
the hook on the right downward to remove the service
panel.
(2) Remove screws (3 for front, 3 for rear/5
✕
10) of the top
panel and remove it.
Figure 1
Top panel fixing screws
Top panel
Service panel
fixing screws
Service panel
Grille
fixing
screws
Fan grille
2. Removing the fan motor (MF1, MF2)
(1) Remove the service panel. (See figure 1.)
(2) Remove the top panel. (See figure 1.)
(3) Remove 5 fan grille fixing screws (5
✕
10) to detach the
fan grille. (See figure 1.)
(4) Remove a nut (for right handed screw of M6) to detach
the propeller. (See photo 1.)
(5) Disconnect the connectors, FAN11, FAN12, FAN21 and
FAN 22 on controller circuit board in electrical parts box.
(6) Remove 4 fan motor fixing screws (5
✕
25) to detach the
fan motor. (See photo 2.)
Fan motor fixing screws
Photo 3
3. Removing the electrical parts box
(1) Remove the service panel. (See figure 1.)
(2) Remove the top panel. (See figure 1.)
(3) Disconnect the indoor/outdoor connecting wire from
terminal block.
(4) Remove all the following connectors from controller circuit board;
fan motor, linear expansion valve, thermistor <Outdoor pipe>,
thermistor <Discharge>, thermistor <Outdoor 2-phase pipe>,
thermistor <Outdoor>, high pressure switch, low pressure
switch, solenoid valve coil <Four-way valve> and solenoid
valve coil <Bypass valve>. Then remove a screw (4
✕
8)
from the valve bad to remove the lead wire.
Pull out the disconnected wire from the electrical parts box.
<Diagram symbol in the connector housing>
• Fan motor (FAN11, FAN12, FAN21 and FAN22)
• Linear expansion valve (LEV-A and LEV-B)
• Thermistor <Outdoor pipe> (TH3)
• Thermistor <Discharge> (TH4)
• Thermistor <Outdoor 2-phase pipe, Outdoor> (TH6/7)
• High pressure switch (63H)
• Low pressure switch (63L)
• Solenoid valve coil <Four-way valve> (21S4)
• Solenoid valve coil <Bypass valve> (SV2)
(5) Remove the terminal cover and disconnect the
compressor lead wire.
(6) Remove an electrical parts box fixing screw (4
✕
10) and
detach the electrical parts box by pulling it upward. The
electrical parts box is fixed with 2 hooks on the left and 1
hook on the right.
Electrical
parts box
Controller circuit board
(C.B.)
Electrical parts
box fixing screw
Terminal cover
Cover panel
(Front)
Cover panel fixing screws
Motor for
compressor
(MC)
Photo 1
Fan
motor
Fan motor fixing screws
Propeller
Front panel
Nut
Terminal block
(TB1)
Photo 2
Valve bed
Screw
Grille
fixing
screws
Slide
OC294-D-4.qxp 05.3.9 11:06 AM Page 96