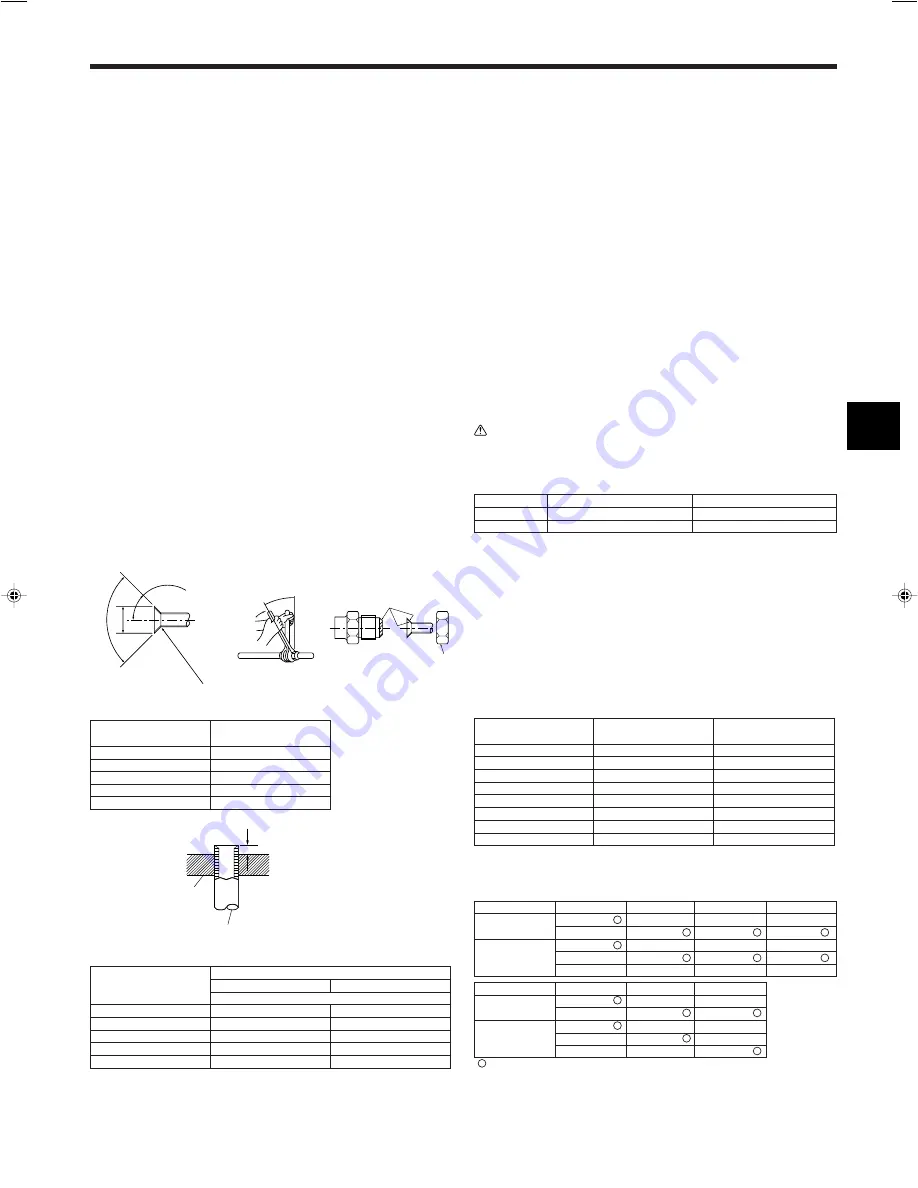
5
4. Installing the refrigerant piping
4.1. Precautions
4.1.1. For devices that use R407C refrigerant
• Do not use the existing refrigerant piping.
• Do not use crushed, misshapen, or discolored tubing. The inside of the tub-
ing should be clean and free from harmful sulfuric compounds, oxidants,
dirt, debris, oils and moisture.
• Store the piping to be used during installation indoors and keep both ends of
the piping sealed until just before brazing.
• Use ester oil, ether oil or alkylbenzene (small amount) as the refrigerator oil
to coat flares and flange connections.
• Use liquid refrigerant to fill the system.
• Do not use a refrigerant other than R407C.
• Use a vacuum pump with a reverse flow check valve.
• Do not use the tools that are used with conventional refrigerants.
• Do not use a charging cylinder.
• Be especially careful when managing the tools.
• Do not use commercially available dryers.
4.1.2. For devices that use R410A refrigerant
• Use ester oil, ether oil, alkylbenzene oil (small amount) as the refrigeration oil
applied to the flared sections.
• Use C1220 copper phosphorus, for copper and copper alloy seamless pipes,
to connect the refrigerant pipes. Use refrigerant pipes with the thicknesses
specified in the table to the below. Make sure the insides of the pipes are
clean and do not contain any harmful contaminants such as sulfuric com-
pounds, oxidants, debris, or dust.
Warning:
When installing or moving the air conditioner, use only the specified refriger-
ant (R410A) to charge the refrigerant lines. Do not mix it with any other refriger-
ant and do not allow air to remain in the lines. Air enclosed in the lines can
cause pressure peaks resulting in a rupture and other hazards.
RP35, 50
RP60-140
Liquid pipe
ø6.35 thickness 0.8 mm
ø9.52 thickness 0.8 mm
Gas pipe
ø12.7 thickness 0.8 mm
ø15.88 thickness 1.0 mm
• Do not use pipes thinner than those specified above.
4.2. Connecting pipes (Fig. 4-1)
• When commercially available copper pipes are used, wrap liquid and gas pipes
with commercially available insulation materials (heat-resistant to 100 °C or more,
thickness of 12 mm or more).
• The indoor parts of the drain pipe should be wrapped with polyethylene foam insu-
lation materials (specific gravity of 0.03, thickness of 9 mm or more).
• Apply thin layer of refrigerant oil to pipe and joint seating surface before tightening
flare nut.
• Use two wrenches to tighten piping connections.
• Use refrigerant piping insulation provided to insulate indoor unit connections. Insu-
late carefully.
B
Flare nut tightening torque
A
Flare cutting dimensions
Copper pipe O.D.
Flare dimensions
(mm)
øA dimensions (mm)
ø6.35
8.7 - 9.1
ø9.52
12.8 - 13.2
ø12.7
16.2 - 16.6
ø15.88
19.3 - 19.7
ø19.05
23.6 - 24.0
90
°
±
0.5
°
ø
A
R0.4~R0.8
A
45
°±
2
°
B
C
D
Fig. 4-1
A
Die
B
Copper pipe
A
A
B
Fig. 4-2
Copper pipe O.D.
A (mm)
(mm)
Flare tool for R-22·R407C
Flare tool for R410A
Clutch type
ø6.35 (1/4")
0 - 0.5
1.0 - 1.5
ø9.52 (3/8")
0 - 0.5
1.0 - 1.5
ø12.7 (1/2")
0 - 0.5
1.0 - 1.5
ø15.88 (5/8")
0 - 0.5
1.0 - 1.5
ø19.05 (3/4")
0 - 0.5
1.0 - 1.5
Copper pipe O.D.
Flare nut O.D.
Tightening torque
(mm)
(mm)
(N·m)
ø6.35
17
14 - 18
ø6.35
22
34 - 42
ø9.52
22
34 - 42
ø12.7
26
49 - 61
ø12.7
29
68 - 82
ø15.88
29
68 - 82
ø15.88
36
100 - 120
ø19.05
36
100 - 120
C
Apply refrigerating machine oil over the entire flare seat surface.
D
Use correct flare nuts meeting the pipe size of the outdoor unit.
Available pipe size
RP35, 50
RP60
RP71
RP100, 125, 140
Liquid side
ø6.35
ø6.35
–
–
ø9.52
ø9.52
ø9.52
ø9.52
ø12.7
–
–
–
Gas side
ø15.88
ø15.88
ø15.88
ø15.88
–
–
–
ø19.05
P25
P35, 50, 60, 71 P100, 125, 140
Liquid side
ø6.35
–
–
–
ø9.52
ø9.52
ø12.7
–
–
Gas side
–
ø15.88
–
–
–
ø19.05
: Factory flare nut attachment to the heat-exchanger.