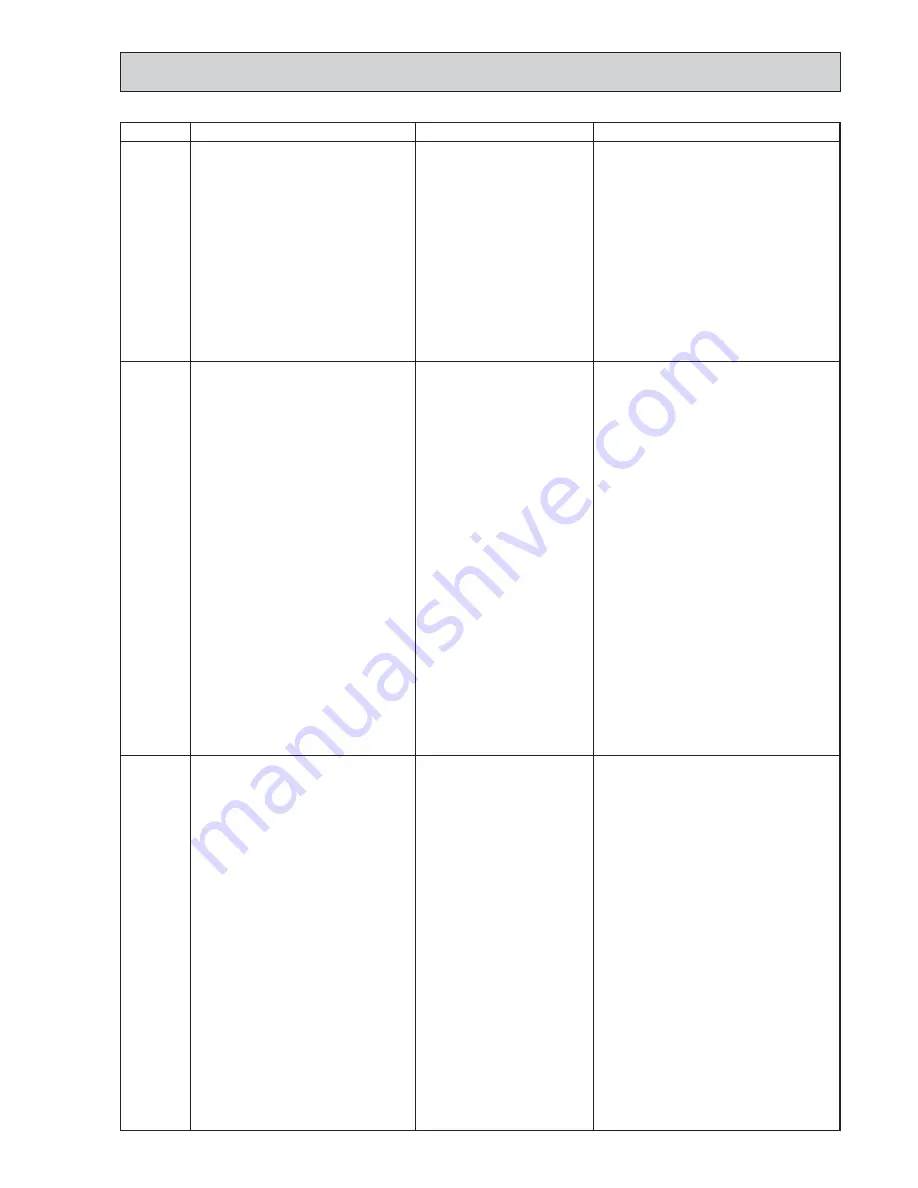
19
Error Code
Abnormal point and detection method
Cause
Countermeasure
P9
Abnormality of pipe temperature ther-
mistor / Condenser-Evaporator (TH5)
1
The unit is in three-minute resume pro-
tection mode if short/open of thermistor
is detected. Abnormal if the unit does
not get back to normal within three min-
utes. (The unit returns to normal opera-
tion, if it has normally reset.)
2
Constantly detected during cooling, dry-
ing, and heating operation (except
defrosting)
Short: 90˚C[194˚F] or more
Open: -40˚C[-40˚F] or less
1
Defective thermistor
characteristics
2
Contact failure of connector
(CN44) on the indoor controller
board (Insert failure)
3
Breaking of wire or contact
failure of thermistor wiring
4
Temperature of thermistor is
90˚C[194˚F] or more or
-40˚C[-40˚F] or less caused by
defective refrigerant circuit.
5
Defective indoor controller
board
1
–
3
Check resistance value of thermistor.
For characteristics, refer to (P1) above.
2
Check contact failure of connector (CN44)
on the indoor controller board.
Refer to 7-5.
Turn the power on and check restart after
inserting connector again.
4
Operate in test run mode and check pipe
<condenser / evaporator> temperature.
If pipe <condenser / evaporator> tempera-
ture is extremely low (in cooling mode) or
high (in heating mode), refrigerant circuit
may have defect.
5
When no problems are found in
1
-
4
above,
replace the indoor unit control board.
E0
or
E4
Remote controller transmission
error(E0)/signal receiving error(E4)
1
Abnormal if main or sub remote con-
troller can not receive normally any
transmission from indoor unit of refriger-
ant address “0” for three minutes.
(Error code : E0)
2
Abnormal if sub remote controller could
not receive for any signal for two min-
utes. (Error code: E0)
1
Abnormal if indoor controller board can
not receive normally any data from
remote controller board or from other
indoor controller board for three minutes.
(Error code: E4)
2
Indoor controller board cannot receive
any signal from remote controller for two
minutes. (Error code: E4)
1
Check disconnection or looseness of indoor
unit or transmission wire of remote controller.
2
Set one of the remote controllers “main”.
If there is no problem with the action above.
3
Check wiring of remote controller.
• Total wiring length: max.500m
(Do not use cable
✕
3 or more)
• The number of connecting indoor units:
max.16units
• The number of connecting remote con-
troller: max.2units
When it is not the above-mentioned problem of
1
~
3
4
Diagnose remote controllers.
a) When “RC OK” is displayed,
Remote controllers have no problem.
Turn the power off, and on again to check.
If abnormality generates again, replace
indoor controller board.
b) When “RC NG” is displayed,
Replace remote controller.
c) When “RC E3” is displayed,
d) When “ERC 00-06” is displayed,
[ c),d)
→
Noise may be causing abnormality. ]
∗
If the unit is not normal after replacing
indoor controller board in group control,
indoor controller board of address “0”
may be abnormal.
E3
or
E5
Remote controller transmission
error(E3)/signal receiving error(E5)
1
Abnormal if remote controller could not
find blank of transmission path for six
seconds and could not transmit.
(Error code: E3)
2
Remote controller receives transmitted
data at the same time, compares the
data, and when detecting it, judges
different data to be abnormal 30
continuous times. (Error code: E3)
1
Abnormal if indoor controller board could
not find blank of transmission path.
(Error code: E5)
2
Indoor controller board receives trans-
mitted data at the same time, compares
the data,and when detecting it, judges
different data to be abnormal 30
continuous times. (Error code: E5)
1
Set a remote controller to main, and the
other to sub.
2
Remote controller is connected with only one
indoor unit.
3
The address changes to a separate setting.
4
~
6
Diagnose remote controller.
a) When “RC OK”is displayed, remote con-
trollers have no problem.
Turn the power off,and on again to check.
When becoming abnormal again, replace
indoor controller board.
b)When “RC NG”is displayed, replace
remote controller.
c)When “RC E3”or “ERC 00-66”is displayed,
noise may be causing abnormality.
1
Contact failure at transmission
wire of remote controller
2
All remote controllers are set
as “sub” remote controller. In
this case, E0 is displayed on
remote controller, and E4 is
displayed at LED (LED1, LED2)
on the outdoor controller circuit
board.
3
Mis-wiring of remote controller
4
Defective transmitting receiving
circuit of remote controller
5
Defective transmitting receiving
circuit of indoor controller board
of refrigerant address “0”
6
Noise has entered into the
transmission wire of remote
controller.
1
Two remote controller are set
as “main.”
(In case of 2 remote con-
trollers)
2
Remote controller is connected
with two indoor units or more.
3
Repetition of refrigerant
address
4
Defective transmitting receiving
circuit of remote controller
5
Defective transmitting receiving
circuit of indoor controller
board
6
Noise has entered into trans-
mission wire of remote con-
troller.