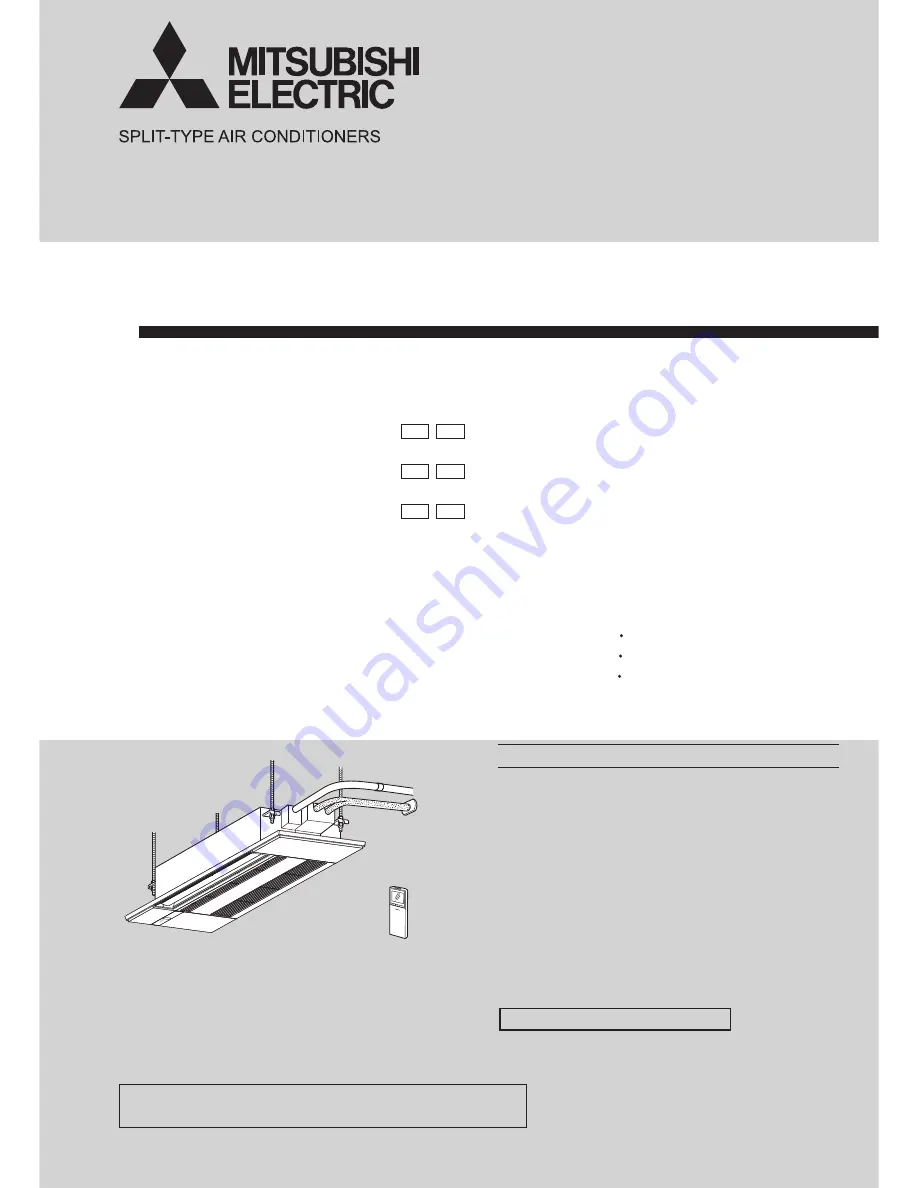
No. OBH801
Models
MLZ-KP25VF
-
E1
,
ER1
MLZ-KP35VF
-
E1
,
ER1
MLZ-KP50VF
-
E1
,
ER1
INDOOR UNIT
NOTE:
RoHS compliant products have <G> mark on the spec name plate.
MLZ-KP25VF
MLZ-KP35VF
MLZ-KP50VF
SERVICE MANUAL
Outdoor unit service manual
MXZ-D VA Series (OBH626)
MXZ-E VA Series (OBH723)
MXZ-F VF Series (OBH790)
PARTS CATALOG (OBB801)
CONTENTS
1. TECHNICAL CHANGES ··································· 2
2. SAFETY PRECAUTION ···································· 3
3. PART NAMES AND FUNCTIONS ···················· 7
4. SPECIFICATION ··············································· 8
5. NOISE CRITERIA CURVES ······························ 9
6. OUTLINES AND DIMENSIONS ······················ 10
7. WIRING DIAGRAM ···········································11
8. REFRIGERANT SYSTEM DIAGRAM ············· 12
9. SERVICE FUNCTIONS ··································· 13
10. MICROPROCESSOR CONTROL ···················· 16
11. TROUBLESHOOTING ····································· 24
12. DISASSEMBLY INSTRUCTIONS ··················· 38