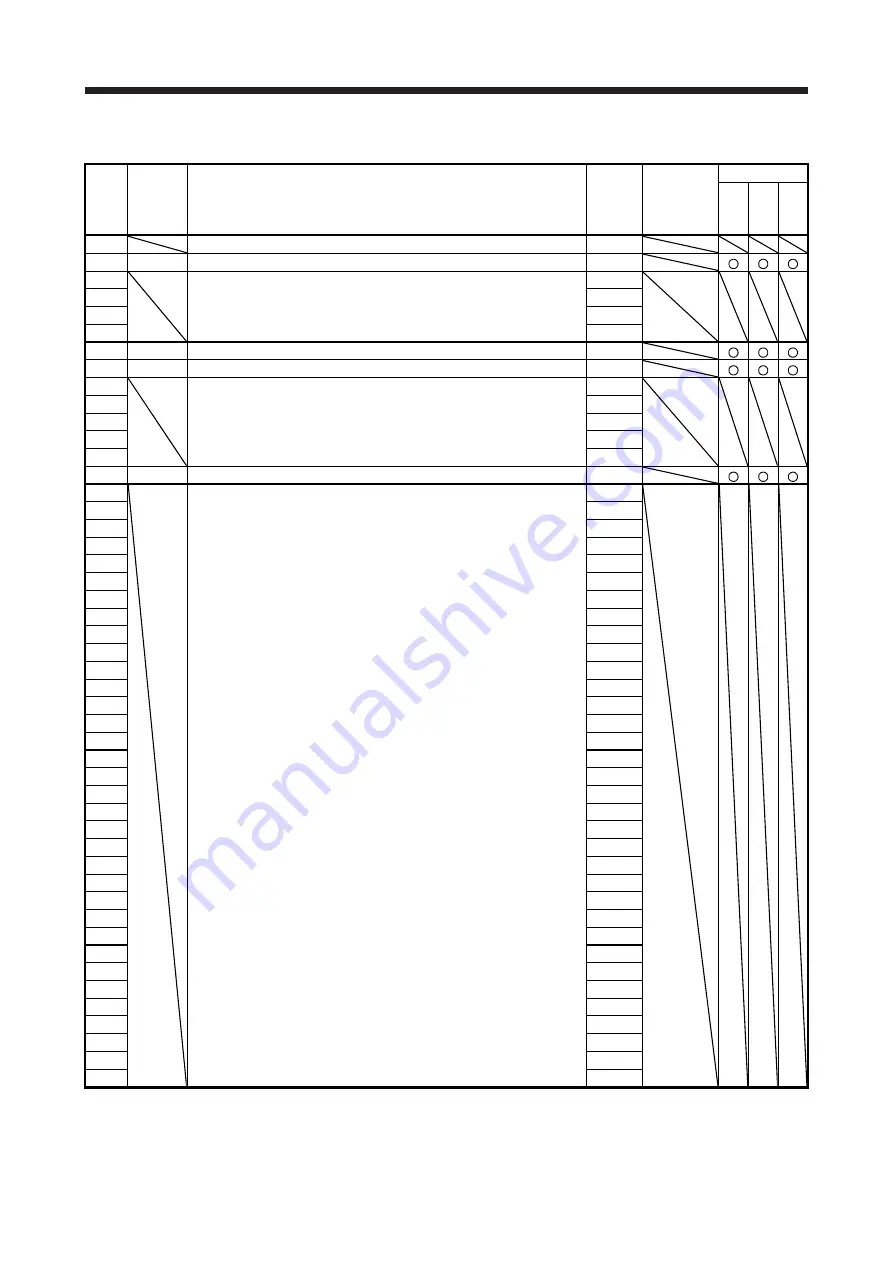
3. PARAMETERS
3 - 6
3.1.4 I/O setting parameters ([Pr. PD_ _ ])
No. Symbol
Name
Initial
value
Unit
Control mode
Position
Speed
Pr
essur
e
PD01
For manufacturer setting
0000h
PD02
*DIA2
Input signal automatic on selection 2
0000h
PD03 For manufacturer setting
0020h
PD04
0021h
PD05
0022h
PD06
0000h
PD07
*DO1
Output device selection 1
0005h
PD08
*DO2
Output device selection 2
0004h
PD09 For manufacturer setting
0003h
PD10
0000h
PD11
0004h
PD12
0000h
PD13
0000h
PD14
*DOP3 Function selection D-3
0000h
PD15 For manufacturer setting
0000h
PD16
0000h
PD17
0000h
PD18
0000h
PD19
0000h
PD20
0
PD21
0
PD22
0
PD23
0
PD24
0000h
PD25
0000h
PD26
0000h
PD27
0000h
PD28
0000h
PD29
0000h
PD30
0
PD31
0
PD32
0
PD33
0000h
PD34
0000h
PD35
0000h
PD36
0000h
PD37
0000h
PD38
0000h
PD39
0000h
PD40
0000h
PD41
0000h
PD42
0000h
PD43
0000h
PD44
0000h
PD45
0000h
PD46
0000h
PD47
0000h
PD48
0000h
Summary of Contents for MELSERVO MR-J4-B-LL Series
Page 9: ...A 8 MEMO ...
Page 31: ...1 FUNCTIONS AND CONFIGURATION 1 20 MEMO ...
Page 63: ...3 PARAMETERS 3 18 MEMO ...
Page 71: ...4 PRESSURE LOOP GAIN ADJUSTMENT 4 8 MEMO ...
Page 79: ...5 TROUBLESHOOTING 5 8 MEMO ...