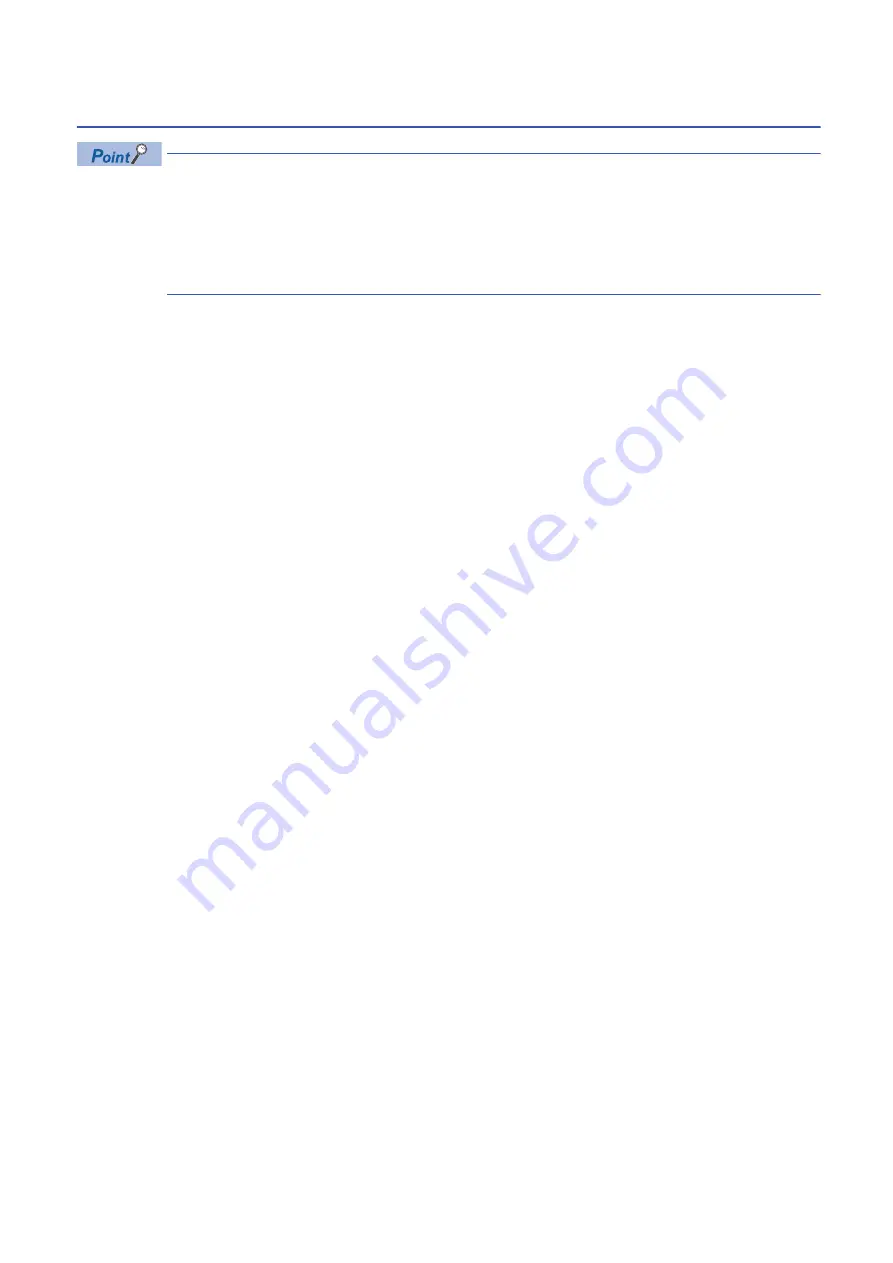
100
9 APPENDIX
9.4 Fabrication of the encoder cable
9.4
Fabrication of the encoder cable
It is recommended to use options indicated in the following section for the encoder cable.
When fabricating an encoder cable, use the recommended products described in the following sections.
Page 21 CONNECTORS USED FOR ROTARY SERVO MOTOR WIRING
Page 27 CONNECTION OF SERVO AMPLIFIER AND ROTARY SERVO MOTOR
When fabricating encoder cables, note the descriptions in this section, in order to ensure the reliability of communication.
Fabricate cables with the following procedure.
1.
Selection of connectors
• Check the cable clamp size.
Page 21 CONNECTORS USED FOR ROTARY SERVO MOTOR WIRING
Page 27 CONNECTION OF SERVO AMPLIFIER AND ROTARY SERVO MOTOR
• Obtain the specification, wiring guide for the connector, and other documents from the manufacturer.
• Purchase assembly jigs and similar parts as necessary.
2.
Selection of cables
• Select a recommended wire or equivalent indicated in chapter 5.
• Select a shielded twisted pair cable.
• Select a cable with a diameter that can be clamped with the connector cable clamp.
• Select a cable whose length, diameter, and bending life are appropriate.
3.
Assembly of the cable
• Check the wiring guide of the connector manufacturer to connect the connector properly.
• Check internal wiring described in chapter 5 to connect it properly.
• Perform a shielding process on the encoder cable properly.
• Do not connect anything to unused pins.
• When wiring the CN2 side connector, connect the external conductor of the shielded cable to the ground plate and fix it to
the connector shell.
• When wiring the connector on the rotary servo motor-side, connect the external conductor of the shielded cable to the SHD
terminal.
• Check if the pin arrangement is correct.
• Connect the twisted pair cable in correct combination.
• Check if the number of pairs of P5/LG wiring connected in parallel is correct.
• Fix the cable to the connector with a proper clamping torque.
4.
Inspection
• After assembly, perform conduction, insulation, and other inspections to check if the connection is correct.
• Check the surface for scratches and contamination.
• Check the connector pins for a distortion, bending, dent, and other problems.
• Check the connector pins for foreign matter adhesion, contamination, and discoloration.
5.
Complete