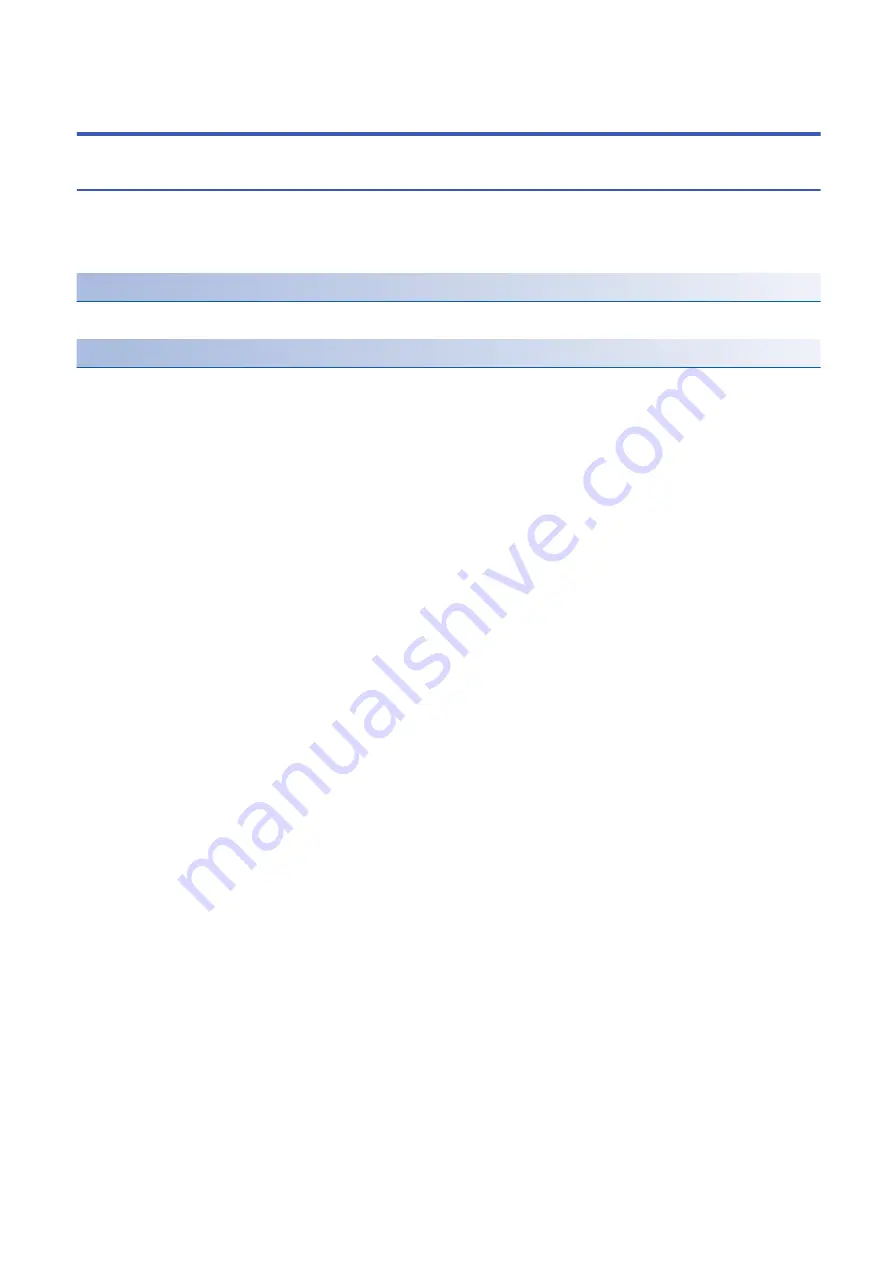
54
APPX
Appendix 1 I/O Conversion Characteristics
APPENDICES
Appendix 1
I/O Conversion Characteristics
An I/O conversion characteristic of D/A conversion is expressed by the slope of the straight line connecting the offset value
and the gain value at the time when a digital value written from the CPU module is converted to an analog output value
(voltage or current).
Offset value
This analog output value (voltage or current) corresponds to a digital value of 0 that is set through the CPU module.
Gain value
This analog output value (voltage or current) corresponds to a digital value of 32000 that is set through the CPU module.
Summary of Contents for MELSEC iQ-R60DA4
Page 1: ...MELSEC iQ R Digital Analog Converter Module User s Manual Startup R60DA4 R60DAV8 R60DAI8 ...
Page 2: ......
Page 17: ...1 PART NAMES 15 1 MEMO ...
Page 22: ...20 3 FUNCTION LIST MEMO ...
Page 24: ...22 4 PROCEDURES BEFORE OPERATION MEMO ...
Page 26: ...24 5 SYSTEM CONFIGURATION MEMO ...
Page 61: ...APPX Appendix 3 External Dimensions 59 A MEMO ...
Page 63: ...I 61 MEMO ...
Page 67: ......