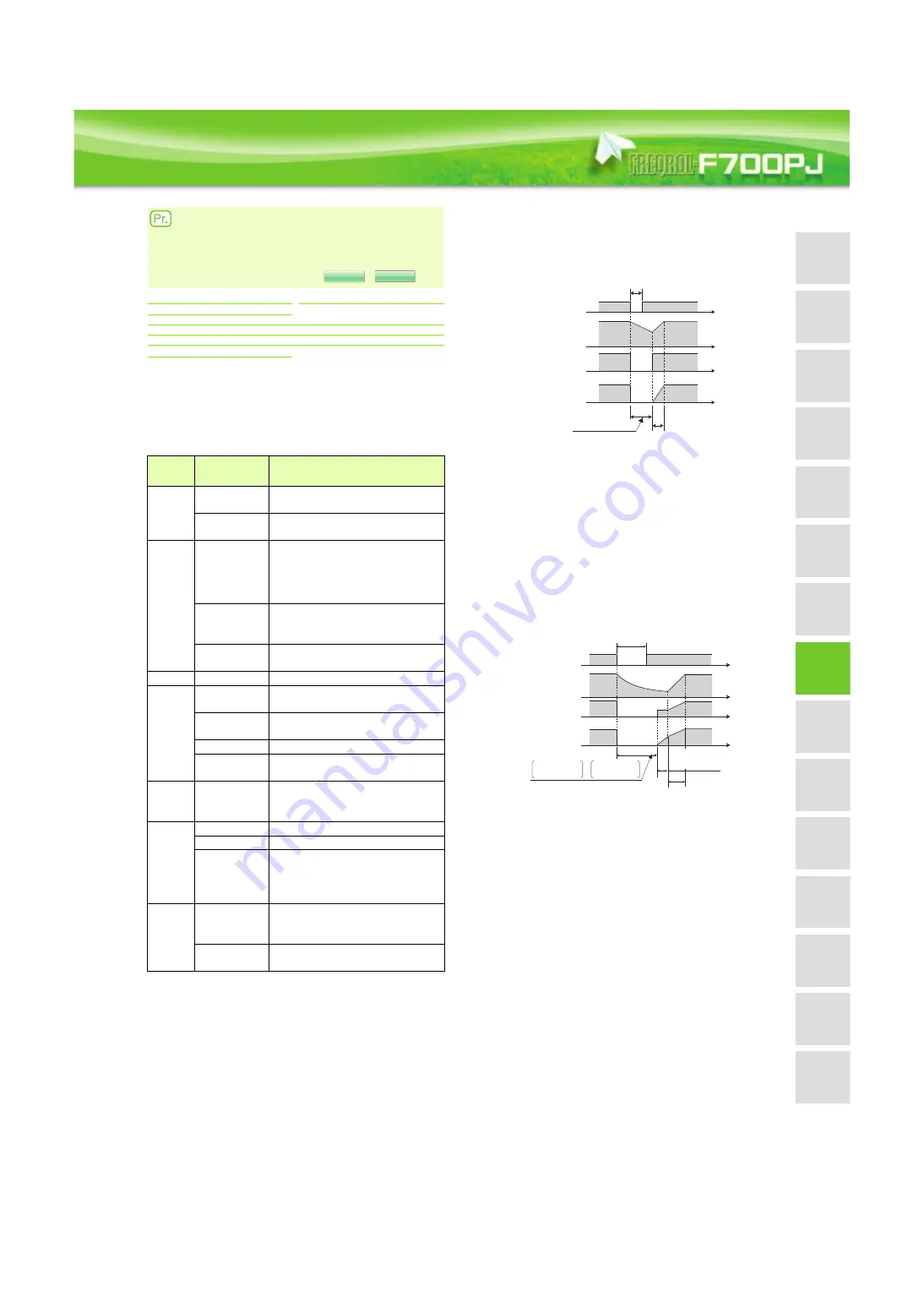
Features
Options
Precautions
Motor
Connection
example
Standard
specs.
Outline
dimensions
Parameter
list
Parameter
descriptions
Protective
functions
IPM motor
control
Compatibility
W
arranty
Te
rminal connection
diagrams
T
erminal specs.
Operation panel
Parameter unit
FR Configurator
39
When setting parameters, refer to the instruction manual (applied) and understand instructions.
The inverter can be restarted without stopping the motor under V/F
control and General-purpose magnetic flux vector control in the
following cases:
when power comes back on after an instantaneous power failure
when motor is coasting at start
For the operation under IPM motor control, refer to the next page.
When
Pr. 162
= "1 (initial value) or 11", automatic restart operation is
performed in a reduced voltage system, where the voltage is
gradually risen with the output frequency unchanged from prior to an
instantaneous power failure independently of the coasting speed of
the motor.
When "0 or 10" is set in
Pr. 162
, the inverter smoothly starts after
detecting the motor speed upon power restoration. (The motor
capacity should be equal to or one rank lower than the inverter
capacity)
When using the frequency search, perform offline auto tuning. Also,
there is a limit to the wiring length.
(Refer to page 73)
Even when the motor is rotating in the opposite direction, the
inverter can be restarted smoothly as the direction of rotation is
detected. (You can select whether to make rotation direction
detection or not with
Pr.299 Rotation direction detection selection at
restarting
. )
Restart operation after turning MRS (X10) signal ON then OFF using
Pr. 30
can be selected as in the table below. This function is used
when the high power factor converter (FR-HC2) is used and the
automatic restart after instantaneous power failure is selected.
(Refer
to page 36)
30, 57, 58, 162, 165, 299, 611
Automatic restart after instantaneous
power failure/flying start under General-
purpose motor control
Pr.30 Regenerative function selection
Pr.57 Restart coasting time
Pr.58 Restart cushion time
Pr.162 Automatic restart after instantaneous power failure selection
Pr.165 Stall prevention operation level for restart
Pr.299 Rotation direction detection selection at restarting
Pr.611 Acceleration time at a restart
Pr.
Number
Setting
Range
Description
30
0 (initial value),
1
The motor starts at the starting frequency
when MRS (X10) turns ON then OFF
2
Restart operation is performed when MRS
(X10) turns ON then OFF
57
0
1.5K or lower ............................ 1s
2.2K to 7.5K or higher............... 2s
11K, 15K ................................... 3s
The above times are coasting time.
0.1 to 5s
Set the waiting time for inverter-triggered
restart after an instantaneous power
failure.
9999
(initial value)
No restart
58
0 to 60s
Set a voltage starting time at restart.
162
0
Frequency search only performed at the
first start
1 (initial value)
Reduced voltage start only performed at
the first start (no frequency search)
10
Frequency search at every start
11
Reduced voltage start at every start (no
frequency search)
165
0 to 150%
Consider the rated inverter current as
100% and set the stall prevention
operation level during restart operation.
299
0 (initial value)
Without rotation direction detection
1
With rotation direction detection
9999
When
Pr. 78
=0, the rotation direction is
detected.
When
Pr. 78
=1,2, the rotation direction is
not detected.
611
0 to 3600s
Set the acceleration time that takes to
reach
Pr. 20
Acceleration/deceleration
reference frequency
setting at a restart.
9999
(initial value)
Acceleration time for restart is the normal
acceleration time (e.g.
Pr. 7
).
V/F
V/F
V/F
GP
MFVC
GP
MFVC
GP
MFVC
Instantaneous (power failure) time
Coasting time
Pr. 57
setting
Restart cushion time
(
Pr. 58
setting)
Power supply
(R/L1, S/L2, T/L3)
Motor speed N
(r/min)
Inverter output
frequency f (Hz)
Inverter output
voltage E (V)
∗
The output shut off timing differs according to the load condition.
∗
Instantaneous (power failure) time
Power supply
(R/L1, S/L2, T/L3)
Motor speed N
(r/min)
Inverter output
frequency f (Hz)
Inverter output
voltage E (V)
Coasting time
(
Pr. 57
)
Speed
detection time
+
Acceleration time
at a restart
(
Pr. 611
setting)
∗
∗
The output shut off timing differs
according to the load condition.
Restart cushion time
(
Pr. 58
setting)
Summary of Contents for F720PJ-11KF
Page 88: ...88 MEMO ...