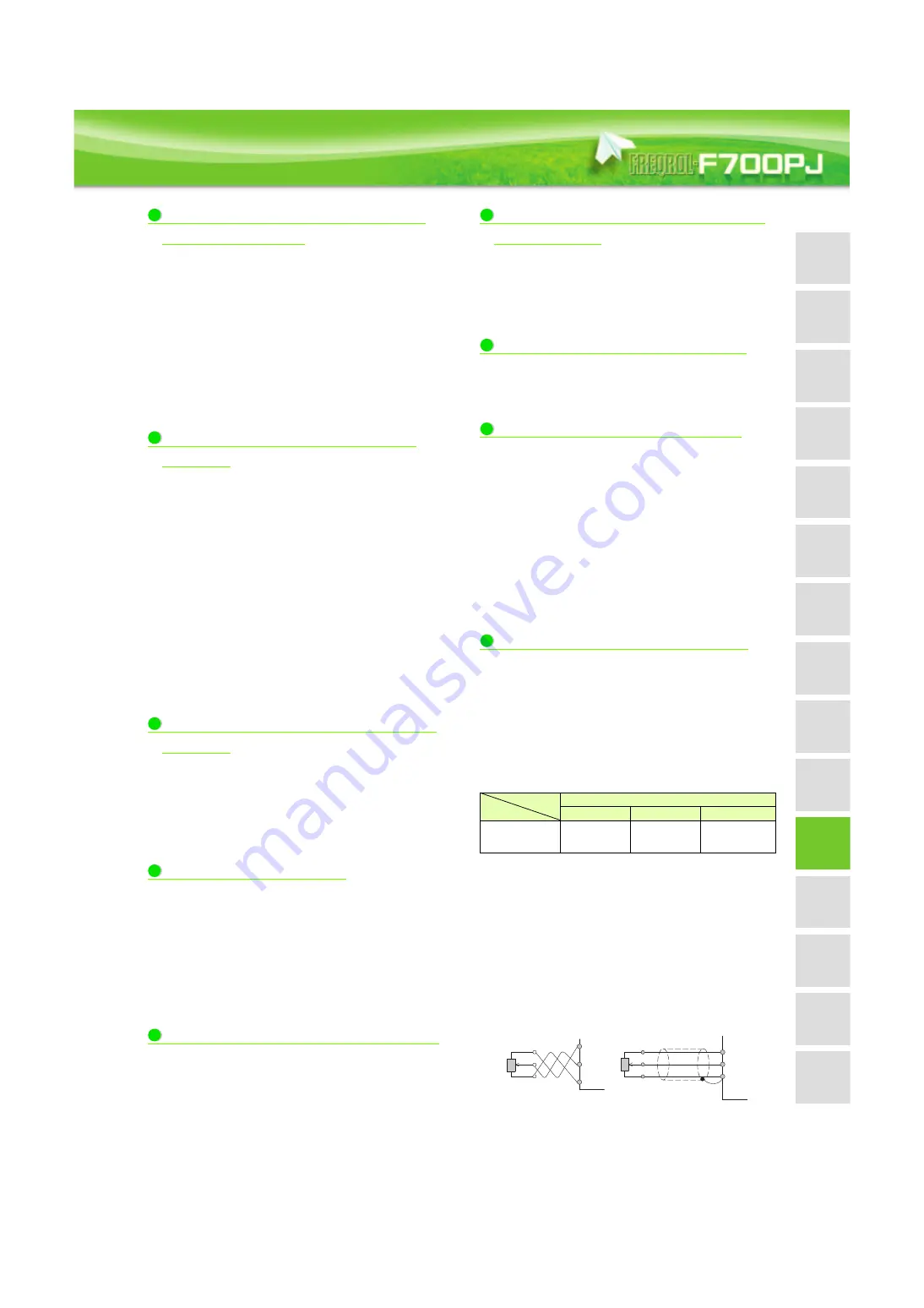
Features
Options
Precautions
Motor
Connection
example
Standard
specs.
Outline
dimensions
Parameter
list
Parameter
descriptions
Protective
functions
IPM motor
control
Compatibility
W
arranty
Te
rminal connection
diagrams
T
erminal specs.
Operation panel
Parameter unit
FR Configurator
73
Precautions for Peripheral Device Selection
Install a molded case circuit breaker (MCCB) on the power receiving
side to protect the wiring of the inverter primary side. For MCCB
selection, refer to
page 68
since it depends on the inverter power supply
side power factor (which changes depending on the power supply
voltage, output frequency and load). Note that the operation
characteristics of the completely electromagnetic MCCB changes
according to the higher harmonic current, so a larger capacity must be
selected. (Check it in the data of the corresponding breaker.) As an
earth (ground) leakage breaker, use the Mitsubishi earth (ground)
leakage breaker designed for harmonics and surges.
(Refer to page 69.)
When installing a molded case circuit breaker on the secondary side of
the inverter, contact each manufacturer for selection of the molded
case circuit breaker.
For operation via external terminal (terminal STF or STR used),
provide a primary side MC to prevent an accident caused by a
natural restart at power recovery after a power failure, such as an
instantaneous power failure, and to ensure safety for maintenance
work. Do not use this magnetic contactor to make frequent starts
and stops. (The switching life of the inverter input circuit is about
1,000,000 times.) For parameter unit operation, an automatic restart
after power failure is not made and the MC cannot be used to make
a start. Note that the primary side MC can stop the operation, but the
regenerative brake specific to the inverter does not operate and the
motor coasts to stop.
Installation of a magnetic contactor at the input side is
recommended. A magnetic contactor avoids overheat or burnout of
a brake resistor when heat capacity of the resistor is insufficient or a
brake regenerative transistor is damaged with short while
connecting an optional brake resistor. In this regard, shut off the
power with the magnetic contactor, for example, when an inverter
fault occurs due to an abnormal output.
Switch the magnetic contactor between the inverter and motor only
when both the inverter and motor are at a stop. When the magnetic
contactor is turned on while the inverter is operating, overcurrent
protection of the inverter and such will activate. When providing MCs to
use the commercial power supply, switch the MCs after both the
inverter and motor stop.
An IPM motor cannot be driven by the commercial power supply.
The inverter has an electronic thermal relay function to protect the
motor from overheating. However, when running multiple motors with
one inverter or operating a multi-pole motor, provide a thermal relay
(OCR) between the inverter and motor. In this case, set the electronic
thermal relay function of the inverter to 0A. And for the setting of the
thermal relay, add the line-to-line leakage current
(Refer to page 74)
to
the current value on the motor rating plate.
Self cooling ability of a motor reduces at low speed operation. A motor
with built-in thermistor is recommended.
Multiple IPM motors cannot be connected to an inverter.
When the wiring length between the inverter and motor is long, select
the device that has enough current rating.
Otherwise the measuring instrument or CT which is used especially for
the 400V class small-capacity inverter may generate heat due to the
influence of line leakage current.
The power factor improving capacitor and surge suppressor on the
inverter output side may be overheated or damaged by the harmonic
components of the inverter output. Also, since an excessive current
flows in the inverter to activate overcurrent protection, do not install a
capacitor or surge suppressor. To improve the power factor, use a DC
reactor (details in
page 60
) or Filterpack.
The input/output of the inverter main circuit (power circuit) includes high
harmonic components, which may interfere with the communication
devices (such as AM radios) or sensors used near the inverter. In this
case, a Filterpack can be used to minimize interference.
When a motor is driven by the inverter, axial voltage is generated on
the motor bearing, which may cause electrical corrosion of the bearing
in rare cases depending on: condition of the grease used for the
bearing, wiring, load, operating conditions of the motor, or specific
inverter settings (high carrier frequency, built-in capacitive filter ON).
Refer to JEM-TR169 (technical report issued by the Japan Electrical
Manufacturers' Association) or contact your sales representative to
take appropriate countermeasures for the motor.
The following shows examples of countermeasures for the inverter.
Decrease the carrier frequency.
Provide a common mode choke on the output side of the inverter.
Avoid using the capacitive filter.
Mitsubishi capacitive filter: FR-BIF, SF
, FR-E5NF-
, FR-S5NFSA
,
FR-BFP2-
When the wiring length between the inverter and motor is long, use
thick wires so that the voltage drop of the main circuit cable is 2% or
less especially at low frequency output. (A selection example for the
wiring distance of 20m is shown on
page 68
)
Especially at a long wiring distance, the maximum wiring length should
be within 500m since the overcurrent protection function may be
misactivated by the influence of a charging current due to the stray
capacitances of the wiring.
The overall wiring length for connection of multiple motors should be
within the value in the table below. (Refer to
page 71
for IPM motors.)
When using the automatic restart after instantaneous power failure
function during the general-purpose motor control with the wiring
length longer than 100m, select "without frequency search" by setting
Pr.162
= "1 or 11". When connecting a parameter unit, use a
recommended connection cable.
Use the recommended connection cable when installing the operation
panel away from the inverter unit or when connecting the parameter unit.
For remote operation via analog signal, wire the control cable between
the operation box or operation signal and inverter within 30m and away
from the power circuits (main circuit and relay sequence circuit) to
prevent induction from other devices.
When using the external potentiometer instead of the parameter unit to
set the frequency, use a shielded or twisted cable, and do not earth
(ground) the shield, but connect it to terminal 5 as shown below.
Installation and selection of molded
case circuit breaker
Handling of primary side magnetic
contactor
Handling of secondary side magnetic
contactor
Thermal relay installation
Secondary side measuring instrument
Disuse of power factor improving capacitor
(power capacitor)
Electromagnetic wave interference
Electrical corrosion of the bearing
Wire thickness and wiring distance
Wiring Length
50m or less
50m to 100m
Exceeding 100m
Pr. 72 PWM frequency
selection
Setting
(carrier frequency)
15 (14.5kHz)
or less
8 (8kHz) or less
2 (2kHz) or less
Twisted cable
Frequency
setting
potentiometer
(3)
(1)
(2)
10
2
5
Shielded cable
(3)
(2)
(1)
10
2
5
Frequency setting
potentiometer
Summary of Contents for F720PJ-11KF
Page 88: ...88 MEMO ...