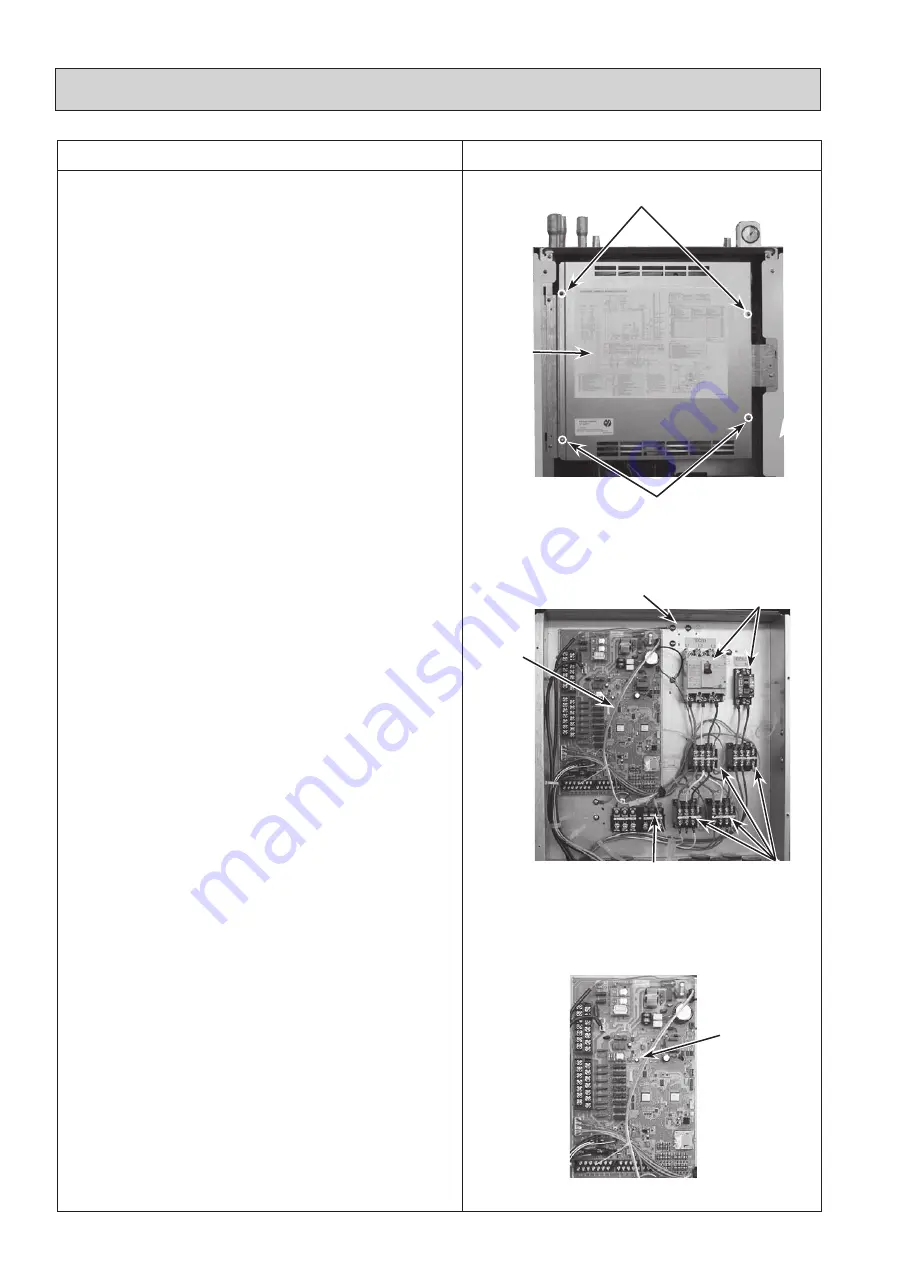
PHOTOS
70
71
DISASSEMBLY PROCEDURE
Photo 3-2
Photo 3-1
3. How to remove the electrical parts
(Steps (1) through (3) are applied to all the following parts.)
<Control box cover> (Photo 3-1)
(1) Remove the front panel. (Refer to Procedure 1).
(2) Remove the 4 screws holding the control box cover.
(3) Slightly lift and pull out the control box cover.
<Earth leakage circuit breaker> (Photo 3-2)
(4) Disconnect all the lead wires from the earth leakage cir
-
cuit breaker.
(5)
Remove the 2 screws on the earth leakage circuit breaker.
Note:
To avoid dropping of the breaker, hold the breaker by
hand when removing the last screws.
<Contactor>
(Photo 3-2)
(4) Disconnect all the lead wires from the contactors.
(5) Remove the 2 screws on each contactor.
Note:
To avoid dropping of the contactors, hold the contac-
tors by hand when removing the last screws.
To prevent an electrical shock, wait until all the LED
lamps on the FTC4 control board are turned off.
<Terminal block> (Photo 3-2)
(4) Disconnect all the lead wires from the terminal block. (To
disconnect the S1, S2 and S3 lead wires, disengage the
locks by pressing on the claws.)
(5) Remove the screw on the terminal block.
Note: To avoid dropping of the terminal block, hold the
terminal block by hand when removing the screw .
<Controller board> (Photo 3-3)
(4) Disconnect all the lead wires from the controller board.
(5) Remove the controller board from the 6 board supports.
w
The photos shown are of the EHST20C-YM9HB model.
Photo 3-3
Control box cover
fixing screws
Control box cover
fixing screws
Control box
cover
Terminal block (TB1)
Earth leakage circuit
breakers (ECB1, ECB)
Contactors
Control box
Controller
board
Controller
board
OCH531
Summary of Contents for ecodan EHPT20X- VM2HB
Page 89: ...89 OCH531 ...