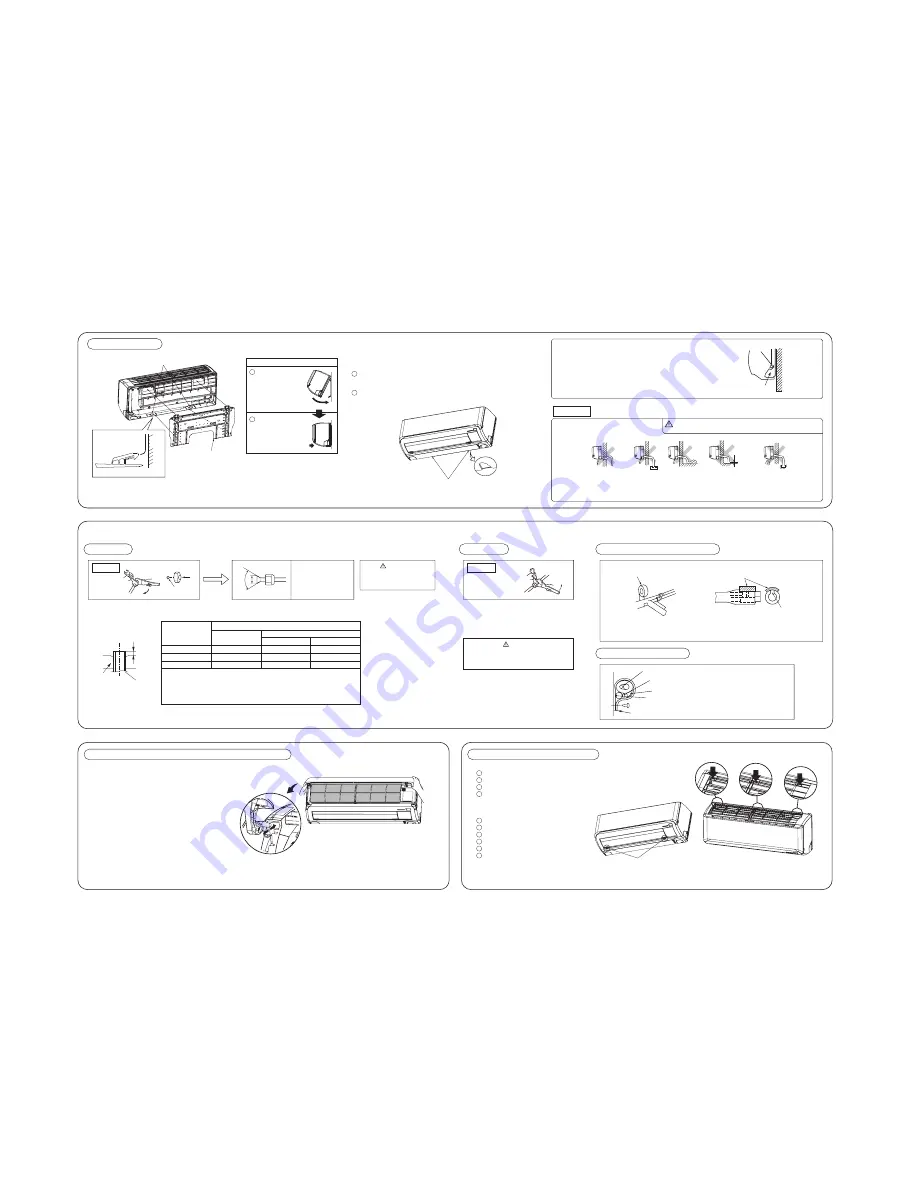
-
-
'11 • SRK-T-118
• Flaring work
Measurement B
Flaring
block
Copper pipe
Finishing work and fixing
Connection wiring,
Earth wiring
Outer tape
Refrigerant piping
Drain hose
Wood screw
Clamp
Cover the exterior portion with outer tape and
shape the piping so it will match the contours
of the route that the piping to take.
Also fix the wiring and pipings to the wall with
clamps.
RLA012A012B
Open/close and detachment/attachment of the air inlet panel
○
To open, pull the panel at both ends of lower part
and release latches, then pull up the panel until
you feel resistance.
(The panel stops at approx. 60
°
open position)
○
To close, hold the panel at both ends of lower
part to lower downward and push it slightly until
the latch works.
○
To remove, pull up the panel to the position
shown in right illustration and pull it toward you.
○
To install, insert the panel arm into the slot on the
front panel from the position shown in right
illustration, hold the panel at both ends of lower
part, lower it downward slowly, then push it
slightly until the latch works.
How to remove and fit the front panel
○
Removing
Remove the air inlet panel.
Remove the 2 set screws.
Remove the 3 latches in the upper section.
Move the lower part of the panel forward and
push upwards to remove.
1
2
3
4
○
Fitting
Do remove the air filter.
Cover the body with the front panel.
Fit the 3 latches in the upper section.
Tighten the 2 set screws.
Fit the air filter.
Fit the air inlet panel.
1
2
3
4
5
6
Set screws
○
Uncover the wireless remote control, and mount the batteries
[R03 (AAA, Micro),
×
2 pieces] in the body regularly.
(Fit the poles with the indication marks,
+
&
−
without fail)
○
Conventionally, operate the wireless remote control by holding
in your hand.
○
Avoid installing it on a clay wall etc.
Cover
CAUTION
Wood screws
ø3.5 X 16
Wireless remote control
Battery
INSTALLATION OF WIRELESS CONTROL
Mounting method of battery
Fixing to pillar or wall
Do not use new and
old batteries together.
2
6
5
Remove the lid.
Remove the terminal cover.
Remove the wiring clamp.
Connect the connecting wire securely to the terminal block.
1) Connect the connection wire securely to the terminal
block. If the wire is not affixed completely, contact will be
poor, and it is dangerous as the terminal block may heat
up and catch fire.
2) Take care not to confuse the terminal numbers for indoor
and outdoor connections.
Fix the connecting wire by wiring clamp.
Attach the terminal cover.
Attach the lid.
1
2
3
4
5
6
7
ELECTRICAL WIRING WORK
CAUTION
In case of faulty wiring connection, the indoor unit stops, and
then the run lamp turns on and the timer lamp blinks.
Use cables for interconnection wiring to avoid loosening of the
wires.
CENELEC code for cables Required field cables.
H05RNR4G1.5 (example) or 245IEC57
H Harmonized cable type
05 300/500 volts
R Natural-and/or synth, rubber wire insulation
N Polychloroprene rubber conductors insulation
R Stranded core
4or5 Number of conductors
G One conductor of the cable is the earth conductor
(yellow/green)
1.5 Section of copper wire (mm
2
)
Preparation of indoor unit
Mounting of connecting wires
Terminal block
Lid
Terminal
cover
Clamp
The screws of the lid and the terminal
cover are tightened securely.
1
3
2 N
• Forced cooling operation
Turn on a power supply again after a while after turn off a power supply.
Then press continually the ON/OFF button 5 seconds or more.
○
Install the removed flared nuts to the pipes to be connected,
then flared the pipes.
○
Remove the flared nuts. (on both liquid and gas sides)
Keep the openings of the pipes covered with tapes etc. to prevent dust, sand, etc. from entering them.
CONNECTION OF REFRIGERANT PIPINGS
Preparation
(Do not turn)
Press
Remove
A
90
±
0.5˚
Dimension A
Liquid side ø6.35 : 9.1 (mm)
Gas side ø9.52 : 13.2 (mm)
ø12.7 : 16.6 (mm)
CAUTION
Do not apply refrigerating machine
oil to the flared surface.
Indoor
Copper pipe diameter
Use a flare tool designed for R410A or a conventional flare tool.
Please note that measurement B (protrusion from the flaring block) will vary depending on the
type of a flare tool in use.
If a conventional flare tool is used, please use a copper pipe gauge or a similar instrument to
check protrusion so that you can keep measurement B to a correct value.
Clutch type flare tool for
R410A
Conventional (R22) flare tool
ø6.35
ø9.52
ø12.7
0.0 - 0.5
0.0 - 0.5
0.0 - 0.5
1.0 - 1.5
1.0 - 1.5
1.0 - 1.5
1.5 - 2.0
1.5 - 2.0
2.0 - 2.5
Measurement B (mm)
Clutch type
Wing nut type
CAUTION
Do not apply excess torque to the flared nuts.
Otherwise, the flared nuts may check depending.
○
Arrange the drain hose in a downward angle.
○
Avoid the following drain piping.
○
Pour water to the drain pan located under the heat exchanger, and ensure that the water is discharged outdoor.
○
When the extended drain hose is indoor, securely insulate it with a heat insulator available in the market.
CAUTION
Wall
Gutter
Pipe accommodating section
Since this air conditioner has been designed to collect dew drops on the rear
surface to the drain pan, do not attach the power cord above the gutter.
Drainage
Go through all installation steps and check if the
drainage is all right. Otherwise water leak may occur.
Higher than specified
The drain hose
tip is in water.
Wavy
The drain hose
tip is in the gutter.
The gap to the ground is
5 cm or less.
Odor from
the gutter
2
1
Installation Steps
Pass the pipe through
the hole in the wall,
and hook the upper
part of the indoor unit
to the installation board.
Gently push the lower
part to secure the unit.
• How to remove the indoor unit from the installation board
Fixing of indoor unit
Push up at the marked portion of the indoor unit base lower latch, and slightly
pull it toward you. (both right and left hand sides) (The indoor unit base lower
latch can be removed from the installation board)
Push up the indoor unit upward. So the indoor unit will be removed from the
installation board.
1
2
The marked portion of the indoor unit base lower latch.
Indoor unit
Installation board
Installation board
Indoor unit base latch
Wall
Latch (2 locations)
CONCERNING TERMINAL CONNECTION FOR AN INTERFACE
Remove the front panel and lid of control.
Remove the control.
There is a terminal (respectively marked with CNS) for the indoor control board.
In connecting an interface, connect to the respective terminal securely with the connection harness
supplied with an optional “Interface connection kit SC-BIKN-E” and fasten the connection harness
onto the indoor control box with the clamp supplied with the kit.
For more details, please refer to the user’s manual of your “Interface connection kit SC-BIKN-E”.
1
2
3
INSTALLATION TEST CHECK POINTS
After installation
The power supply voltage is correct as the rating.
No gas leaks from the joints of the operation valve.
Power cables and crossover wires are securely fixed to the terminal board.
The screws of the lid and the terminal cover are tightened securely.
Operation valve is fully open.
The pipe joints for indoor and outdoor pipes have been insulated.
Air conditioning operation is normal.
No abnormal noise.
Water drains smoothly.
Protective functions are not working.
The remote control is normal.
Operation of the unit has been explained to the customer.
(Three-minutes restart preventive timer)
When the air conditioner is restarted or when changing the operation, the unit
will not start operating for approximately 3 minutes.
This is to protect the unit and it is not a malfunction.
Test run
Check the following points again after completion of the installation, and before turning on the power. Conduct a test run again and ensure that the unit operates properly.
At the same time, explain to the customer how to use the unit and how to take care of the unit following the user’s manual.
○
Connect the pipes on both liquid and gas sides.
○
Tighten the nuts to the following torque.
Liquid side (ø6.35) : 14.0 - 18.0 N·m (1.4 - 1.8 kgf·m)
Gas side (ø9.52) : 34.0 - 42.0 N·m (3.4 - 4.2 kgf·m)
(ø12.7) : 49.0 - 61.0 N·m (4.9 - 6.1 kgf·m)
Connection
Insulation of the connection portion
Indoor
Liquid side
Gas side
(Do not turn)
• Cover the indoor unit s flare-connected joints, after they are checked for a gas leak,
with an indoor unit heat insulating material and then wrap them with a tape with an
attached insulation pad placed over the heat insulating material’s slit area.
Cover the coupling with insulator and then cover it with tapes.
Vinyl tape
Use an attached insulation pad for heat insulation.
Position it so that the slit area faces upward.
Installing the air-cleaning filters
Filter holder
Air-cleaning filter
1. Open the air inlet panel and remove the air filters.
2. Install the filter holders, with the air-cleaning filters installed in the holders.
In the air conditioner.
• Each air-cleaning filter can be installed in the left or right filter holder.
3. Install the air filters and close the inlet panel.
Connect charge hose to check joint of outdoor unit.
Liquid side : Close the liquid valve with hexagon wrench key.
Gas side : Fully open the gas valve.
Carry out cooling operation. (If indoor temperature is low, operate
forced cooling operation.)
After low pressure gauge become 0.01MPa, stop cooling operation
and close the gas valve.
1
2
3
<How to pump down>
○
In order to protect the environment, be sure to pump down (recovery of refrigerant).
○
Pump down is the method of recovering refrigerant from the indoor unit to the
outdoor unit when the pipes are removed from the unit.
HOW TO RELOCATE OR DISPOSE OF THE UNIT
Unit ON/OFF button
Indoor unit PCB
CNS terminal
Lid of control
Summary of Contents for DXK09ZJ-S
Page 2: ......
Page 3: ...TECHNICAL MANUAL ...
Page 12: ... 11 SRK T 118 3 Remote controller a Wireless remote controller Unit mm 60 17 3 150 ...
Page 66: ... 63 11 SRK T 118 09 SRK DB 087D Service data record form 57 ...
Page 74: ... 71 11 SRK T 118 09 SRK DB 087D 11 Outdoor unit inspection points DXC09ZJ S 12ZJ S 73 73 64 ...
Page 87: ... 84 11 SRK T 118 11 3 Super link E board SC ADNA E F SL2NA E and SL3N AE BE to control ...
Page 88: ... 85 11 SRK T 118 ...
Page 89: ... 86 11 SRK T 118 ...
Page 103: ... 100 CRBE0323 6 13 11 18 12 15 16 3 17 14 2 4 9 8 7 5 1 8 19 8 10 PANEL FAN ASSY ...
Page 107: ... 104 CRBE0323 6 13 11 18 12 15 16 3 17 14 2 4 9 8 7 5 1 8 19 8 10 PANEL FAN ASSY ...
Page 111: ... 108 CRBE0324 9 13 15 16 14 17 7 6 4 19 1 8 3 11 5 18 10 10 10 2 12 PANEL FAN ASSY ...