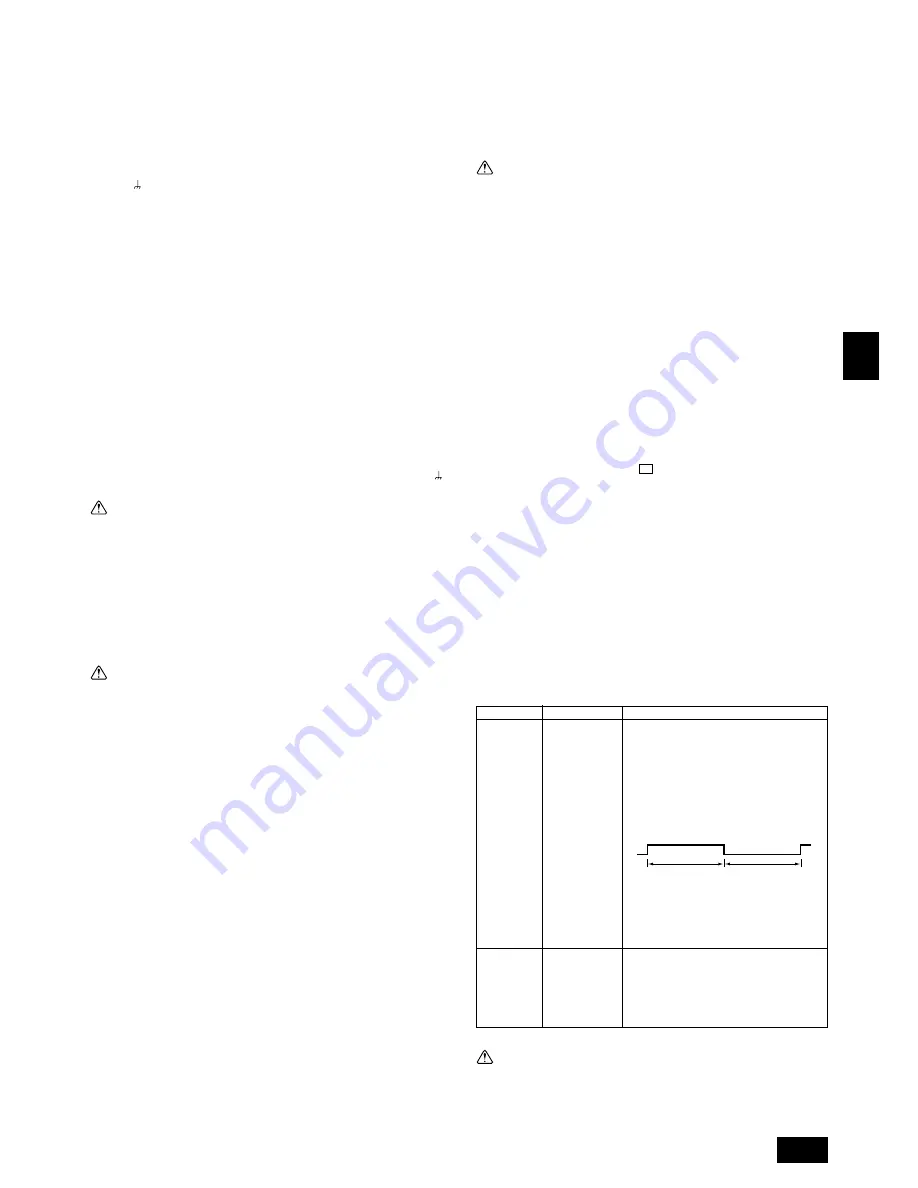
13
GB
D
F
I
NL
E
P
GR
RU
TR
7.5. External I/O Specifications
I/O Specifications
Input
7.4. Setting addresses
(Be sure to operate with the main power turned OFF.)
•
There are two types of rotary switch setting available: setting addresses 1 to 9
and over 10.
<How to set addresses>
Example: If Address is “3”, remain SW12 (for over 10) at “0”, and match
SW11(for 1 to 9) with “3”.
Caution:
Setting the address of the indoor unit controller
•
For the Model 500
The top side indoor controller address of the indoor unit must always be
odd number. The bottom side indoor controller address must be 1 more
than the top side indoor controller address.
•
Setting the address of the outdoor unit controller
The address must be 50 more than the address of the indoor units using
the same refrigerant.
* If the address is not correctly set, operation will not run correctly.
After setting the address, enter the set address on the product nameplate on the
front panel using a permanent marker.
•
The rotary switches are all set to “0” when shipped from the factory. These
switches can be used to set unit addresses.
•
The determination of indoor unit addresses varies with the system at site. Set
them referring to technical data.
•
If connecting a controller inside a central controller, the address of the two con-
trollers inside the Model 500 indoor unit must always be set in the same group.
[Fig. 7.4.1]
(P.5)
• When there is a single Model 250 unit
A
CN41 as it is
*1 The numbers shown in the square (
) are addresses.
*2 The Model 250 indoor unit contains one indoor controller board.
[Fig. 7.4.2]
(P.5)
• When there is a single Model 500 unit
A
Replace CN41 with CN40
B
CN41 as it is
* The Model 500 indoor unit contains two indoor controller boards.
[Fig. 7.4.3]
(P.5)
• When connected to G-50
A
CN41 as it is
B
Group 1
C
Group 2
D
Power supply unit
E
DC Power supply (DC 12V)
Function
Start/Stop
Application
Turning ON/
OFF the indoor
unit
Signal specifications
Pulse [Factory setting: Dip SW1-9 ON]
(a-contact with voltage/without voltage)*1
<With voltage>
Power Source: DC12~24V
Electrical Current:
Approximately 10mA (DC12V)
<Standard Pulse>
* 1 Use minute-current contact (DC12V 1mA)
Caution:
1. Wiring should be covered by insulation tube with supplementary insula-
tion.
2. Use relays or switches with IEC or equivalent standard.
3. The electric strength between accessible parts and control circuit should
have 2750 V or more.
•
Daisy-chain terminals M1 and M2 of the terminal block for transmission line for
centralized control (TB7) on each outdoor unit (OC). * Only use shielded ca-
bles.
•
Disconnect the male power supply connector from CN41 and connect it to
CN40 on only one outdoor unit.
•
Daisy-chain the S terminal of terminal block (TB7) on each outdoor unit with
each other with the grounding wire of the shielded cable.
•
Connect the S terminal of terminal block (TB7) on the outdoor unit whose male
power supply switch connector has been connected to CN40 to the earth ter-
minal on the control box.
•
Install a remote controller following the manual supplied with the remote con-
troller.
•
Connect the “1” and “2” on indoor unit TB15 to a MA remote controller. (Non-
polarized 2-wire)
[Fig. 7.2.1]
(P.3) MA Remote controller
<A> Model 250
<B> Model 500
A
Terminal block for indoor transmission cable
B
Terminal block for outdoor transmission cable
C
MA Remote controller
•
DC 9 to 13 V between 1 and 2 (MA remote controller)
[Fig. 7.2.2]
(P.3) MA Remote controller
<A> Model 250
<B> Model 500
A
Non-polarized
B
Upper level
C
Lower level
D
MA Remote Controller
Note:
1. Ensure that the wiring is not pinched when fitting the terminal box cover.
Pinching the wiring may cut it.
2. Put the transmission cable earth via the outdoor unit’s earth terminal
to the ground.
Caution:
Install wiring so that it is not tight and under tension. Wiring under tension
may break, or overheat and burn.
•
Fix power source wiring to control box by using buffer bushing for tensile force.
(PG connection or the like.) Connect transmission wiring to transmission ter-
minal block through the knockout hole of control box using ordinary bushing.
•
After wiring is complete, make sure again that there is no slack on the connec-
tions, and attach the cover onto the control box in the reverse order removal.
7.3. Connecting electrical connections
(Be sure to prevent terminal screws from loosening.)
Caution:
•
Fix the site wiring firmly in place with wiring clamps.
•
Ensure that wiring installation work does not result in tension being ap-
plied to the wiring. Such tension may result in breaks in wiring, and con-
sequent overheating, smoke, or flame.
Step 1. Turn the key in the center of the panel at the bottom of the unit to
open the panel. Next, remove the four screws in the control box cover
to remove the cover.
Step 2. Install electrical wiring, internal and external connecting wiring, and
earth wiring, as shown in [Fig. 7.3.1]. Refer to “7.5. External I/O Speci-
fications” if installing wiring when external I/O terminals are used.
Step 3. When wiring is complete, check for less connections and wiring mis-
takes, and close the panel.
<In the case of two refrigerant circuits>
Changes to the connector connection and switch settings are required as shown in
[Fig.7.3.2].
[Fig. 7.3.1]
(P.4) MA Remote controller
<A> Model 250
<B> Model 500
A
Transformer
B
External I/O board
C
No.1 Transmission line terminal block
D
No.2 Transmission line terminal block (Note: Connect to top terminal block)
E
Connect transmission line to outdoor unit
F
Fix in place after connecting wiring.
G
Earth
H
Fuse
I
Control box
J
Bottom panel
[Fig. 7.3.2]
(P.4)
<When connected to a 2-refrigerant circuit>
The unit is shipped ready to be connected to a single-refrigerant circuit.
When connected to a 2-refrigerant circuit, make the connection changes and switch
setting changes (SW 2, 3, and 4 on both No. 1 and No.2 boards) as shown in [Fig. 7.3.2]
on site.
over 200ms
(Pulse interval)
over 200ms
(Pulse powering time)
Level [Dip SW1-9 OFF]
Short: operate
Open: stop
Level
Refer to the wiring diagram <Dehumidifica-
tion command>.
Sending a
command to
perform
dehumidifica-
tion with
priority
Dehumidifi-
cation signal