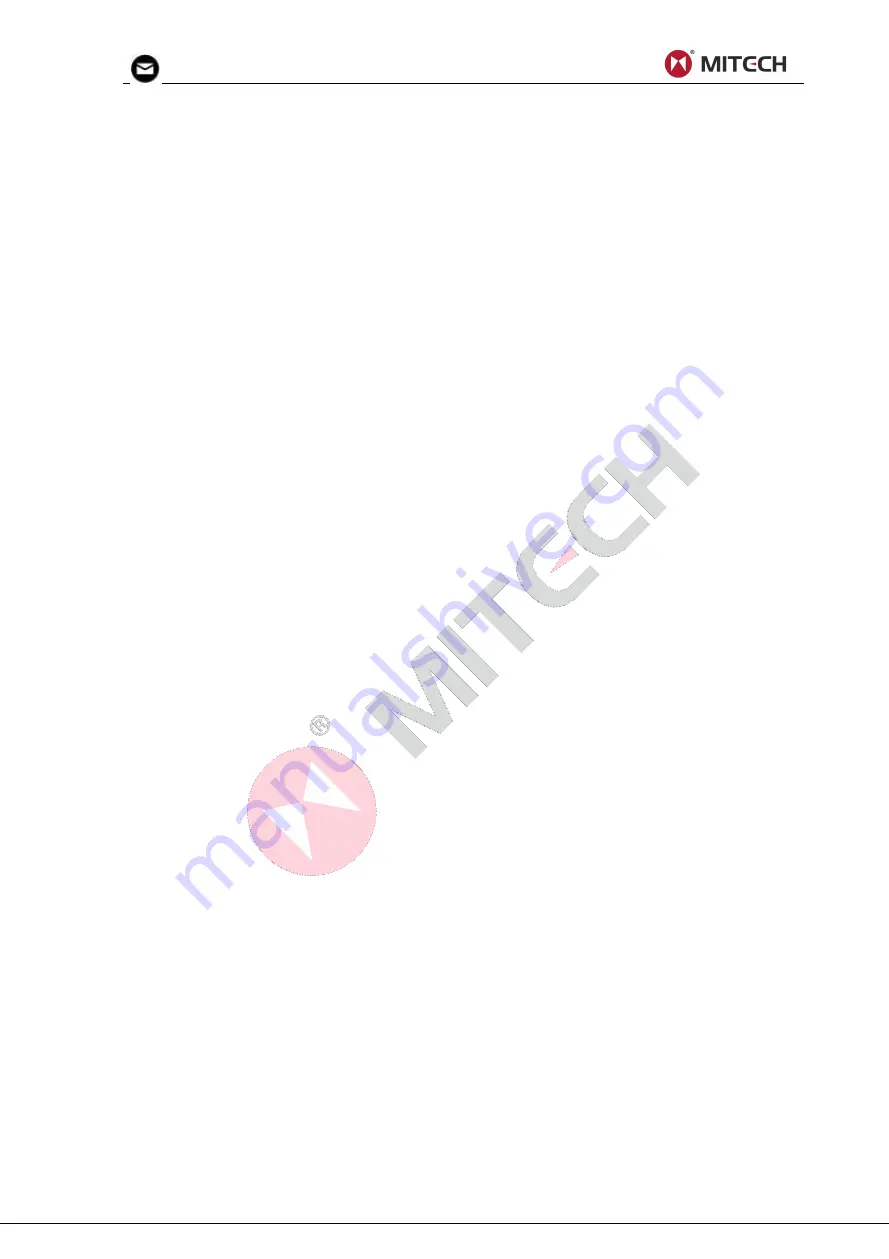
mvip@mitech-ndt.com
Measuring through paints and coatings are also unique, in that the velocity of the paint/ coating will
be significantly different form the actual material being measured. A perfect example of this would
be a mild steel pipe with approximately 0.6mm of coating on the surface. Where the velocity of the
pipe is 5920m/s, and the velocity of the paint is 2300m/s. If the user is calibrated for mild steel pipe
and measures through both materials, the actual coating thickness will appear to be 2.5 times
thicker than it actually is, as a result of the differences in velocity. This error can be eliminated by
using a special echo-echo mode to perform measurements for applications such as these. In
echo-echo mode, the paint/ coating thickness will be eliminated entirely and the steel will be the
only material measured.
Suitability of materials
Ultrasonic thickness measurements rely on passing a sound wave through the material being
measured. Not all materials are good at transmitting sound. Ultrasonic thickness measurement is
practical in a wide variety of materials including metals, plastics, and glass. Materials that are
difficult include some cast materials, concrete, wood, fiberglass, and some rubber.
Couplants
All ultrasonic applications require some medium to couple the sound from the transducer to the
test piece. Typically a high viscosity liquid is used as the medium. The sound used in ultrasonic
thickness measurement does not travel through air efficiently.
A wide variety of couplant materials may be used in ultrasonic gauging. Propylene glycol is
suitable for most applications. In difficult applications where maximum transfer of sound energy is
required, glycerin is recommended. However, on some metals glycerin can promote corrosion by
means of water absorption and thus may be undesirable. Other suitable couplants for
measurements at normal temperatures may include water, various oils and greases, gels, and
silicone fluids. Measurements at elevated temperatures will require specially formulated high
temperature couplants.
Inherent in ultrasonic thickness measurement is the possibility that the instrument will use the
second rather than the first echo from the back surface of the material being measured while in
standard pulse-echo mode. This may result in a thickness reading that is TWICE what it should be.
The Responsibility for proper use of the instrument and recognition of these types of phenomenon
rests solely with the user of the instrument.