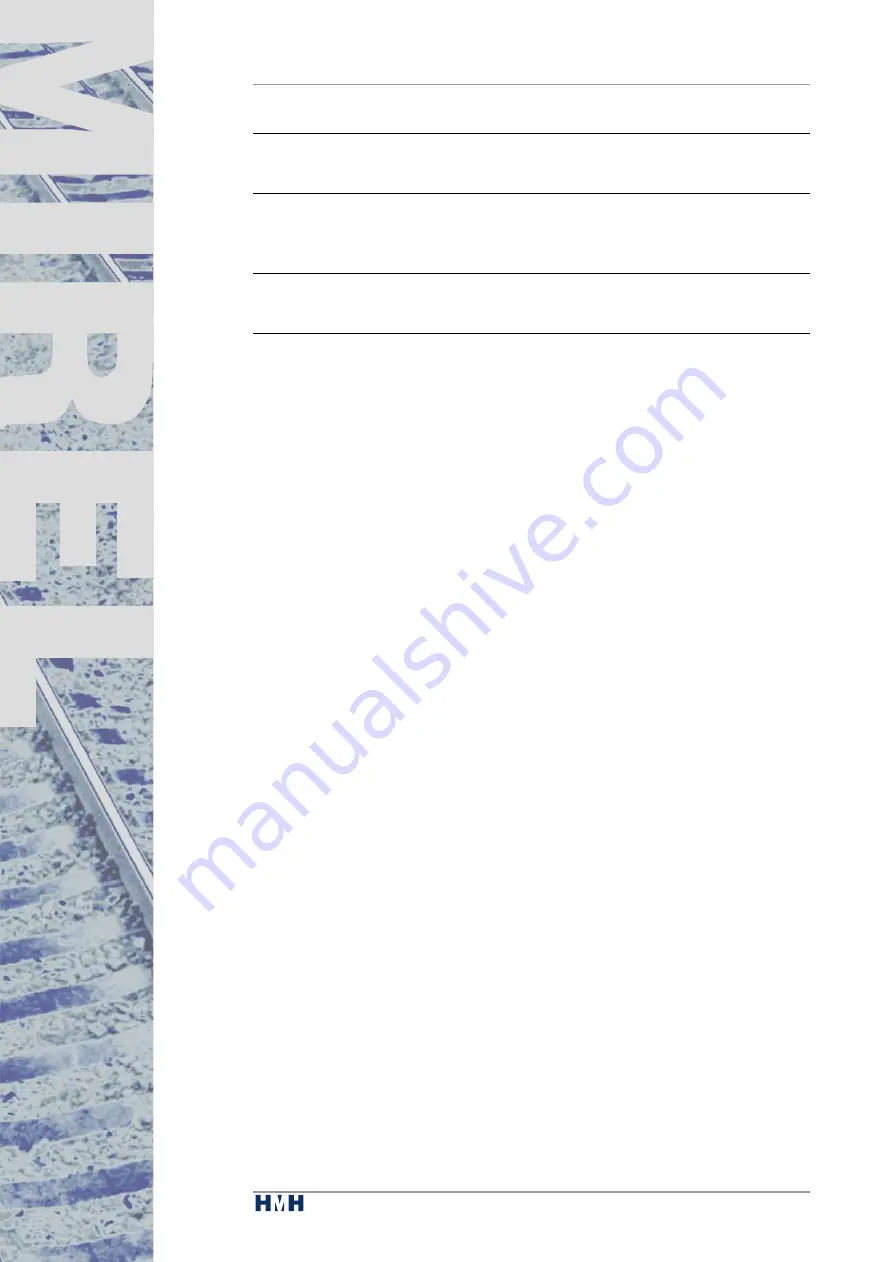
154VZ1 : 190111
15 / 33
6.2 D2 – Continuous Diagnostic Control
Purpose:
This control verifies the status, integrity and functionality of the system during its operation.
Execution:
The train protection system automatically executes this control without intervention by the
operator or maintenance.
Schedule:
During the operation of the train protection system
Description:
The train protection system executes continuous diagnostics using both watchdog circuits
comparing evaluations of channels M and C in the central unit, comparing the indicator and
control channel in the signal repeaters and conducting other continuous tests that check for
proper operation of the train protection system. The train protection system continuously
compares the results of the main (PMM) and comparison (PMC) processor module. Contin-
uous self-diagnostics detect a system fault in the event of differences and place the train
protection system into safe mode. Communication between the central unit and the signal
repeaters is another operation that the train protection system diagnoses continuously. The
train protection system blocks subsequent operation in the event of a serious communica-
tion fault involving the signal repeater in the active cab (where the control switch is on). If a
communication fault is detected in the signal repeater at the inactive cab, the system will
continue to operate in a limited scope and operational repairs are required.
Tests conducted during continuous self-diagnostic controls:
Watchdog circuit test
– both processor modules of the central unit and all signal repeater
modules are equipped with a pair of watchdog circuits. One monitors the proper operation of
the processor itself and the second monitors the operation of the processor in cooperation
with the other circuits. Watchdog circuits monitor the proper operation of the processors,
correct execution of the program, timer activity and the functionality of processor interruption
systems. The watchdog circuits operate with a time base of 16 ms and 100 ms. When a
watchdog fault is detected, the given functional block is re-initialised and an error message
is generated for the entire system. The error code for a fault involving a processor module
(PMM, PMC) of the central unit is
E01
. The error code for a fault involving a signal repeater
indicator module is
E03
. The error code for a fault involving a signal repeater control module
is
E50
.
Integrity test of defined operating parameters
– the central unit and the signal repeater
permanently monitor for consistency between defined parameters and the valid parameters
in the central unit. This concerns the selected working regime and the defined train speed
setting. The time limit for matching the defined and valid parameters is 1 second. If the pa-
rameters are inconsistent during system operation (e.g. there is a communication fault be-
tween the central unit and a signal repeater) or if the central unit does not confirm the ac-
cepted newly set parameters within the defined period of time, the system detects an
integrity fault of the defined parameters and the corresponding error code is
E31
or
E03
.
Evaluation channels M and C in the central unit mutually compare the active working re-
gime. A fault is detected if the active working regime is inconsistent between channels M
and C for longer than 3 seconds and the error code is
E27
. The active working regime in
both channels is permanently tested against the configuration permissions for the specific
train protection system application. The system detects a fault if the active working regime is
Summary of Contents for VZ1
Page 33: ...154VZ1 190111 33 33 12 Notes ...