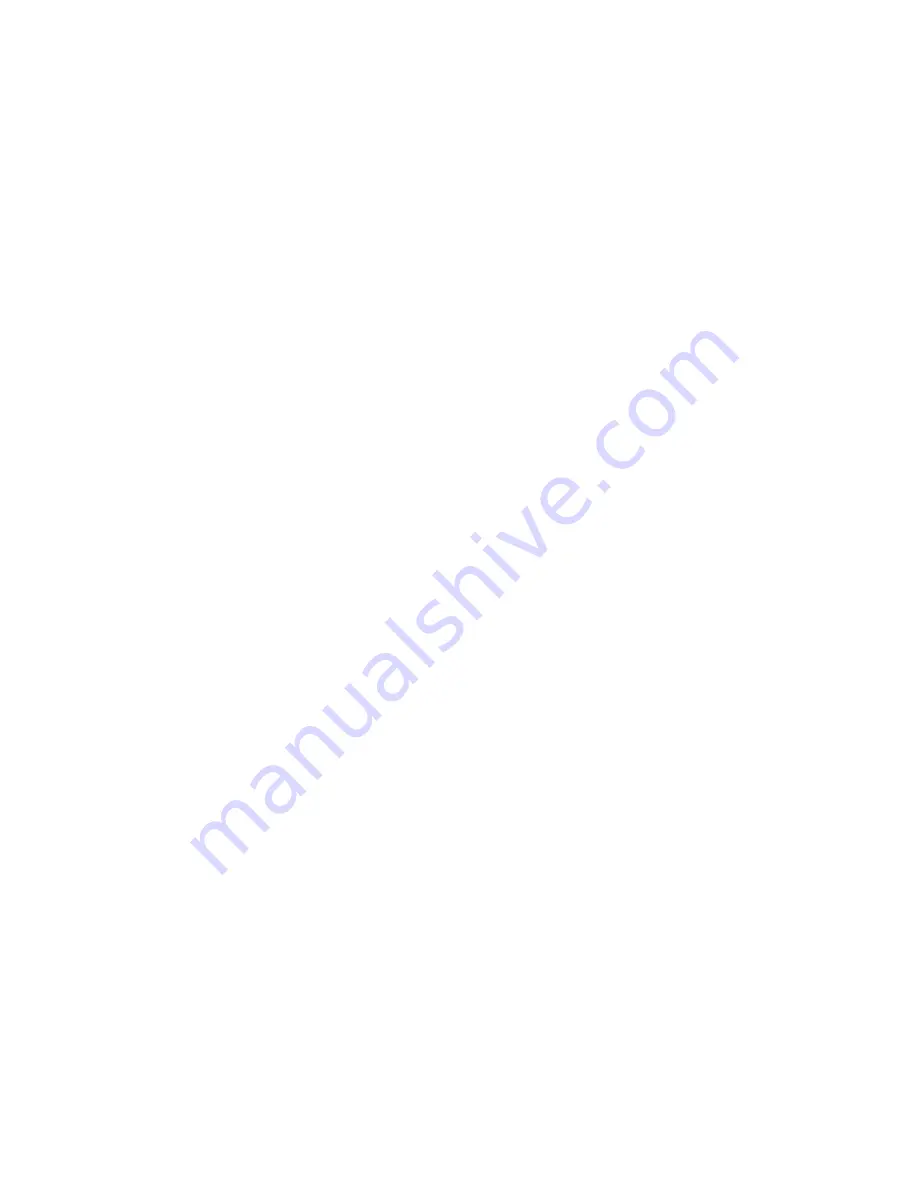
26
Maintenance Procedure - Thermostatic Cartridge
Removal
(refer to Figure 3)
1.
Isolate the supplies to the shower control, and open the flow control to release
pressure and to assist the draining of residual water.
2.
Remove the the lever cap and remove the grubscrew in the top of the shower
control lever with the with a 2.5mm hexagon key (supplied).
3.
Remove the shower control lever, valve shield and shield adaptor.
4.
Using a suitable spanner, unscrew and remove the thermostatic cartridge.
Warning!
Some residual water may be released.
Cleaning/Renewal of Parts
5.
The interior surface of the shower control body must be clean before refitting the
cartridge. If scale or deposition is present, clean
(without thermostatic, flow
and checkvalve cartridges fitted)
using a mild proprietary inhibited scale solvent,
e.g. domestic kettle descalent. After descaling, rinse body thoroughly in clean
water before refitting cartridges.
Note!
The body interior must be cleaned carefully and not damaged in any way.
Do not use any abrasive material.
6.
Cartridges may only be cleaned by flushing through under a jet of clean water to
remove lodged particles.
Do not descale.
Cartridges are not serviceable,
and must not be dismantled.
Cartridges cannot be tested individually, service condition should be assessed
as part of the performance check; refer to
Commissioning Checks
.
7.
Examine all accessible seals for signs of deformation or damage, and if necessary
renew, taking care not to damage seal grooves (a Service Pack is available,
containing all seals).
8.
Lightly coat all rubber seals with a
silicone-only based lubricant
to assist
reassembly (see
lubricants
).