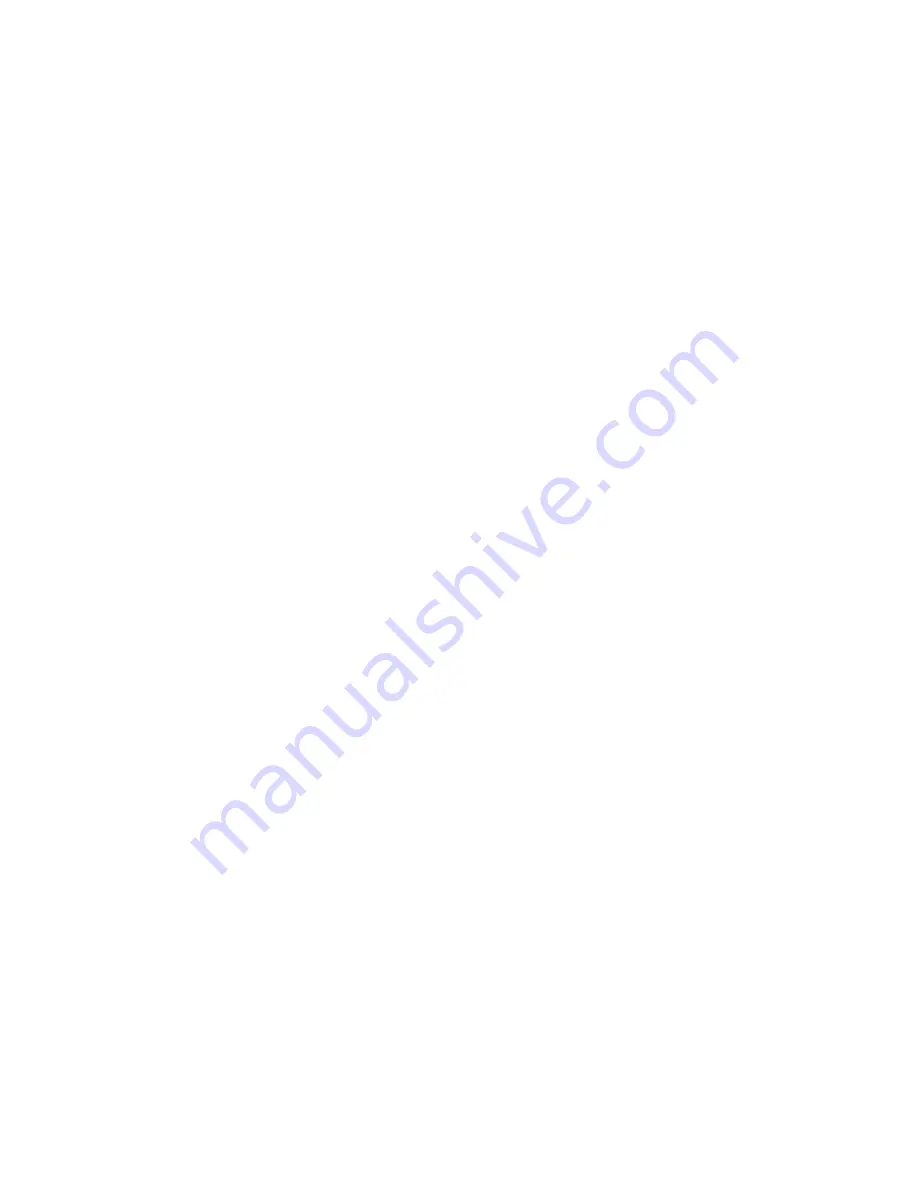
3
Once the initial functions listed above have been performed, press the “I” button on the control panel
to turn the machine on. This will illuminate the “ON” light found on the control panel and activate the
battery condition meter.
Before operating the machine, check the condition of the batteries. The battery condition meter can
be read by looking at which light is illuminated on the meter. The green light on the right end of the
meter indicates that the batteries are fully charged. As the batteries discharge, the light moves to the
left. When the light under “1/2” is illuminated, the batteries are 1/2 charged. Once the meter shows
approximately 1/4 charge, there is not enough power left in the batteries to start the burnishing motor
and the batteries need to be recharged.
The machine can be used in either an “Automatic” mode or a “Manual” mode. In the “Automatic”
mode, the burnishing head is automatically raised or lowered to compensate for irregularities in the
floor. This produces an even finish. In the “Manual” mode, the height of the burnishing head is set by
the operator. The head stays at this height until it is adjusted again by the operator. In either mode,
the motion of the machine is controlled by the handles that are located on either side of the console.
By squeezing the right handle against the console, the machine will move forward. By squeezing the
left handle against the console, the machine will move backwards. The speed of the machine is
controlled by the knob located on the control panel. The speed (in both directions) is increased by
turning the knob clockwise.
The vertical array of five lights in the middle of the control panel under “Pad Pressure” gives an
indication of pad pressure. The top light under the word “MIN” is illuminated when the pad is minimally
touching the floor. The light directly above the word “MAX” is illuminated to give indication of the
maximum amount of pad pressure. The remaining three lights designate varying levels of pad
pressure between “MIN” and “MAX”. It is normal in “AUTOMATIC” mode for the lights to periodically
“bounce” up and down on the display. This “bouncing” is a result of the machine encountering high
and low areas in the floor. As a high spot is encountered, the lights will move down the array. If a low
spot is encountered, the lights will move up the array. It is also normal for the motor to sound like it is
slowing down over a high spot. If the motor did not slow down, there is a possibility that the floor
finish could be damaged.
There are (2) circuit breakers at the bottom left rear corner of the machine. The top one (70A) is for
the burnishing motor. The bottom one (18A) is for the traction drive. If the machine is not operating
properly, check to see if the circuit breakers have popped. If so, depress the top of them to reset.