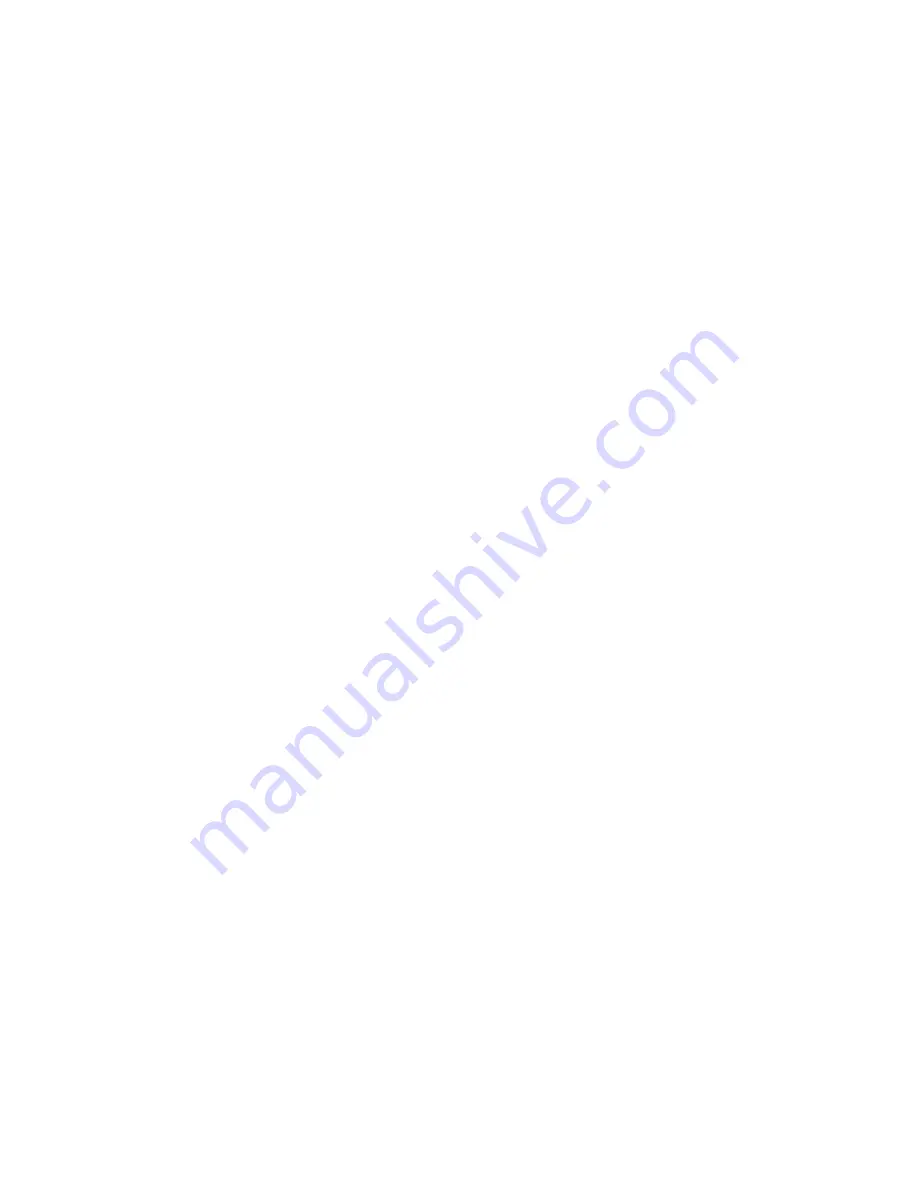
6
MANUAL ZERO ACQUISITION
In Manual Zero operation, the Gross weight is zeroed each time the function
is executed. The function is activated by a key press or user input transition. If
the total accumulated zero offset exceeds the Zero Acquisition Range, the
function is disabled. In this case, the indicator must be re-calibrated to the load
sensing device, in order to reset the true system zero and hence the accumulated
zero offset. The accumulated zero offset itself is reset whenever any of the input
scaling parameters are altered.
The indicator displays a brief message
rEsEt
whenever a zero operation
occurs. The indicator displays
NO
whenever the total accumulated zero exceeds
the value of the Zero Acquisition parameter. In this case, the zero operation is
blocked.
“B-GNT” Operating Mode
In the “
b-6Nt
” operating mode, the Basic, Gross, Net and Tare Weight can be
displayed and controlled. In this mode, indicator functions that pertain to Max
and Min reading memory and the Totalizer are disabled. This is the default mode.
“HILOT” Operating Mode
In the “
HILOt
” operating mode, the Max, Min and Totalizer indicator
functions can be displayed and controlled. In this mode, the Gross, Net and Tare
weight displays and control are disabled (Basic display only.). The table lists the
correspondence of the display annunciators in this mode.
*
Only functional in “HILOT” operating mode.
SETPOINT ALARMS
The indicator has two setpoint alarm Plug-in cards. Only one of these cards
can be installed at a time. These are:
Dual relay, FORM-C
Quad relay, FORM-A
The setpoint alarms can be independently configured for a variety of operating
modes. It is also possible to set the alarms to trigger from the totalizer value.
Each setpoint alarm can be programmed to trigger from the Brutto/Gross weight
or the Net weight. The setpoint alarm figures illustrate the operating modes:
Setpoint Alarm Values
When setpoint alarm is programmed as deviation or band acting, the effective
trigger point is offset by SP1. In these modes, SP1 acts as a master setpoint, that
the other setpoints track.
An alternate list of setpoint values can be stored and recalled as needed.
Select the alternate list with a function key or user input and program the
setpoint values. This allows for quick changeover for a new process condition.
Setpoint Alarm Hysteresis and On/Off Time Delay
Depending on the application, hysteresis or On/Off time delays can be used.
When the setpoint is a control output, hysteresis is usually used to control the
cycle period. Optionally, time delay can also be employed to ensure minimum
On/Off times. This is useful to limit the cycling of mechanical control equipment.
On/Off time delays are effective when the setpoint is used as an alarm output.
The time delays can be used to prevent false triggering during process transient
events, while hysteresis eliminates output chatter at the switch point.
The hysteresis value can be selected to act in the balanced mode or
unbalanced mode. In the balanced mode, the hysteresis action is centered about
the trigger point, while in the unbalanced mode the hysteresis acts on one side
of the trigger point. When the setpoint is a control output, usually balanced
hysteresis is used. This tends to center the oscillation around the setpoint value.
For alarm applications, usually unbalanced hysteresis is used. This makes the
alarm activate precisely at the trigger value.
Setpoint Alarm Output Phase and Panel Annunciator
The output phase (logic) of each setpoint can be reversed. While the front
panel indicator follows the output state, it can be programmed to reverse as
well; or flash for added emphasis.
Setpoint Alarm Reset Modes, Standby Operation
Each setpoint alarm can be programmed for auto or latching reset modes.
Standby operation can be used to prevent the triggering of a low alarm until the
process first exceeds the alarm value. This suppresses false alarms during
system start-up.
OUTPUT
ON CONDITION
RELAY
Energized
Annunciator
Readout
B/G
Max reading
NET
Min Reading
T
Totalizer/Integrator