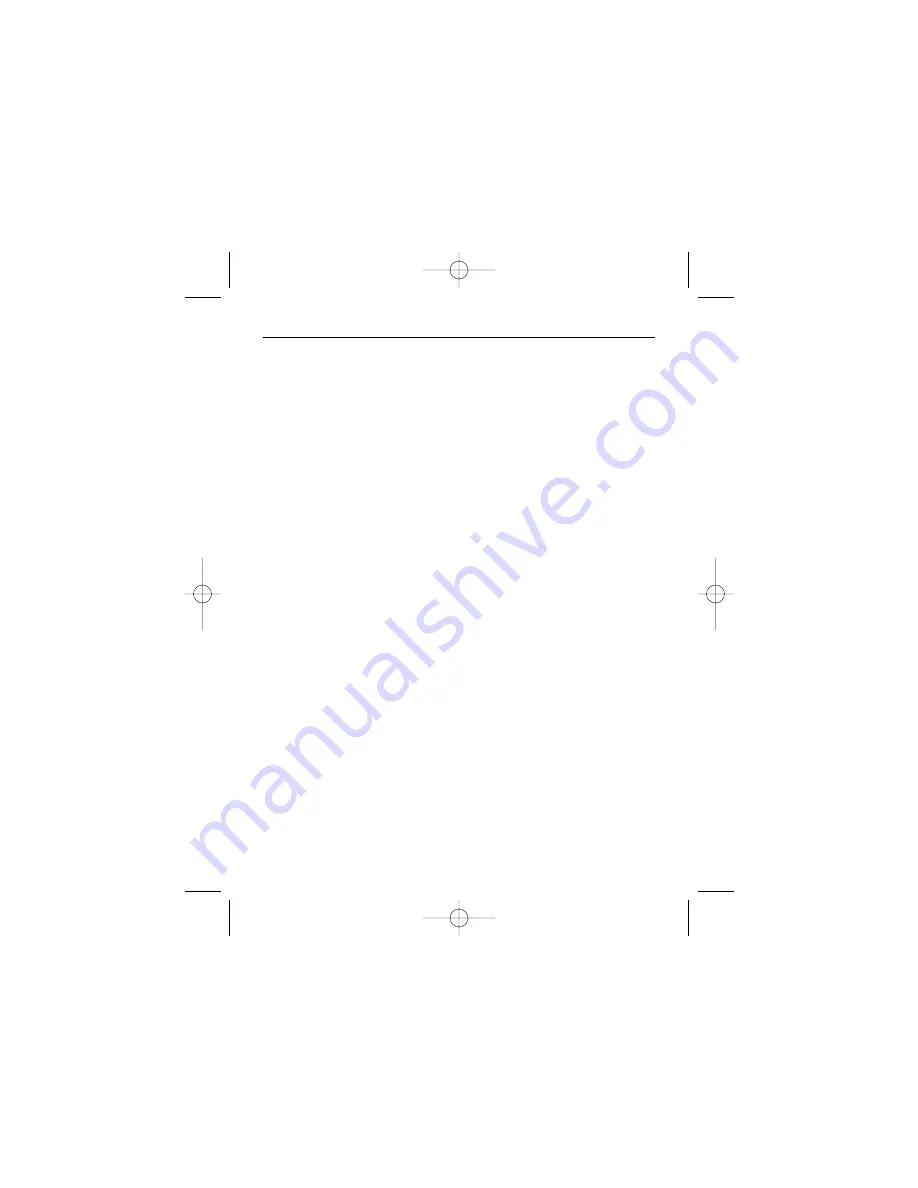
v
Minarik Models DLC300 and DLC400 Digi-Lok® Converters are
used with conventional analog speed controls to produce closed-
loop digital systems capable of controlling motor speed precisely
and with excellent reproducibility.
The Digi-Lok® Converter (DLC) receives the feedback signal
generated by a sensor that monitors a rotating element driven by
the motor. The sensor assembly can be a magnetic pickup with
ferromagnetic gear, or a NPN-type optical encoder or inductive
proximity switch, or a Hall effect sensor with magnetic wheel.
An important distinction exists between any Digi-Lok®
Converter system and a conventional servo drive. The Digi-Lok
Converter reads a velocity-dependent feedback signal and corrects
its output to bring the motor back to its set speed. The Digi-Lok®
Converter will not compensate for any positioning errors caused
by very minor speed fluctuation.
Industrial applications for Digi-Lok® Converter control systems
include many within the food processing, chemical, and
pharmaceutical industries, for example. Blending, mixing,
grinding, pumping, and other such processes often require strict
repeatability to ensure product uniformity. The digital speed-
setting feature of the Digi-Lok® Converter and the closed-loop
design provide that reliability and reproducibility.
Introduction
250-0112-rev3.qxd 7/18/00 10:46 AM Page v
Summary of Contents for DIGI-LOK DLC300
Page 4: ...250 0112 rev3 qxd 7 18 00 10 46 AM Page ii...
Page 10: ...viii 250 0112 rev3 qxd 7 18 00 10 46 AM Page viii...
Page 12: ...2 250 0112 rev3 qxd 7 18 00 10 46 AM Page 2...
Page 14: ...4 250 0112 rev3 qxd 7 18 00 10 46 AM Page 4...
Page 25: ...Installation 15 Figure 3 DLC300 400 connections 250 0112 rev3 qxd 7 18 00 10 46 AM Page 15...
Page 26: ...16 250 0112 rev3 qxd 7 18 00 10 46 AM Page 16...