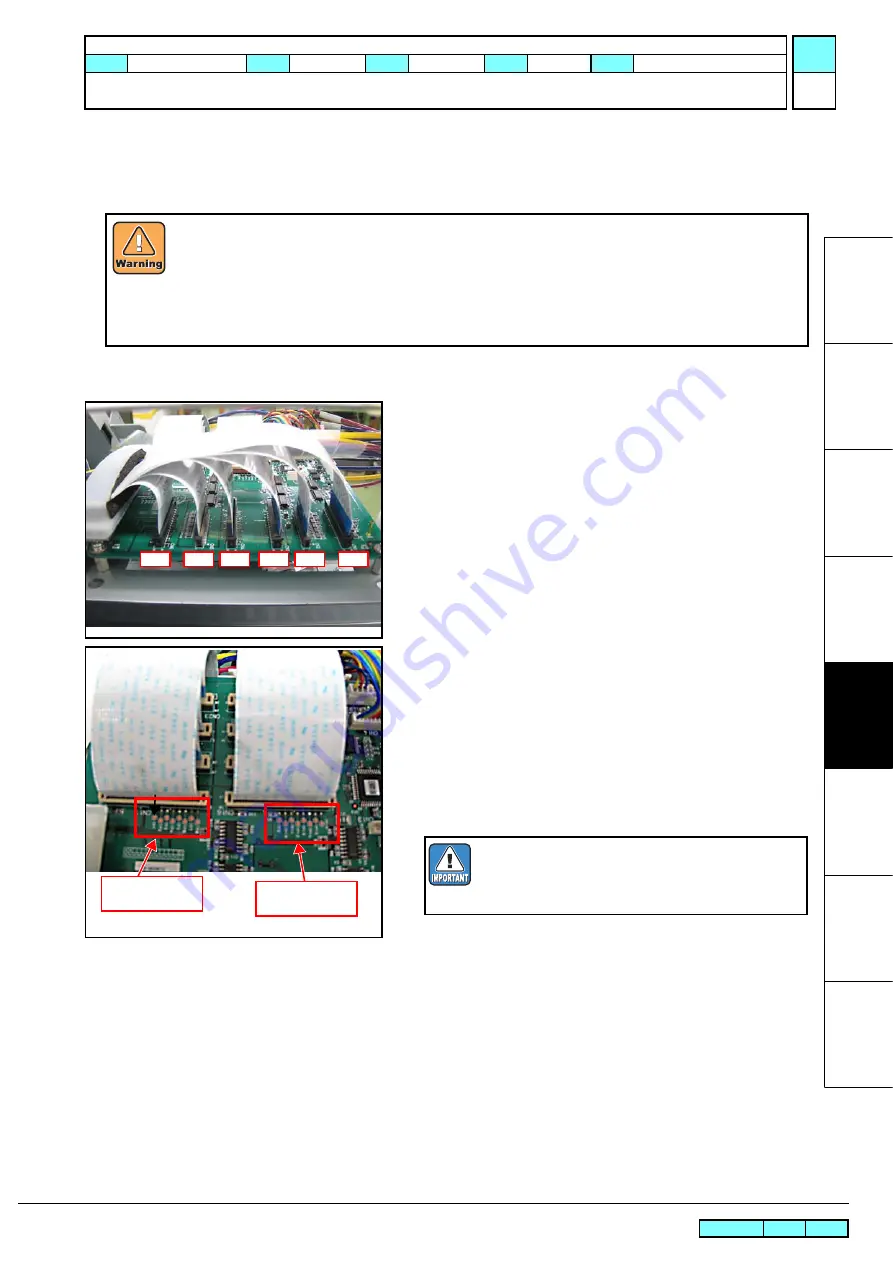
© 2011 MIMAKI ENGINEERING CO.,LTD.
5.2.2
P.1
R.1.0
MAINTENANCE MANUAL > Test Items > Other Test > Checking Damage of the Print Heads
Model
TS34-1800A
Issued 2011.10.17 Revised
F/W ver
1.20
Remark
1.0
5.2.2 Checking Damage of the Print Heads
Outline
Check whether the COM line between the print head and the slider PCB has trouble or not.
Procedure
1. Release the locks on both sides of the HDC_FFC ASSY con-
nected to CN1 to CN6 on the slider PCB ASSY. And then pull
out the HDC_FFC ASSY.
Measure a resistance between the test pin TP1 to 16 and GND
on the ink slider PCB to determine the value. Connect the nega-
tive terminal of the tester to the GND test pin (TPG 1) and mea-
sure the resistance by getting the positive terminal touch to TP1
to 16.
When the result of TP1 to 8 is 10M
Ώ
and more, the head 2 has
no defect.
When the result of TM9 to 16 is 10M
Ω
and more, the head 1
has no defect.
After turning off the sub and main power switches in order, unplug the power code.
Check if no electric charge is remaining in the PCB.
Refer to the "4.4.2 Electric charge checking when replace the Electrical Parts"
It is very dangerous if sleep mode functions mistakenly during the operation.
Moreover, the PCB may be damaged in case electric charge still remains inside.
Also there is a possibility of electric shock because of high power voltage applied the high-pressure part
of the power supply PCB assy. Take care to avoid contact with it.
CN1
CN2
CN3
CN4
CN5
CN6
TP1
6
TP1
5
TP1
4
TP1
3
TP1
2
TP1
1
TP1
0
TP9
TP8
TP7
TP6
TP5
TP4
TP3
TP2
TP1
If any of the head COM line defect is found, the print
head may be broken. Replace the print heads first.
Connecting the normal main PCB without replacing
the broken head will break the PCB continuously.