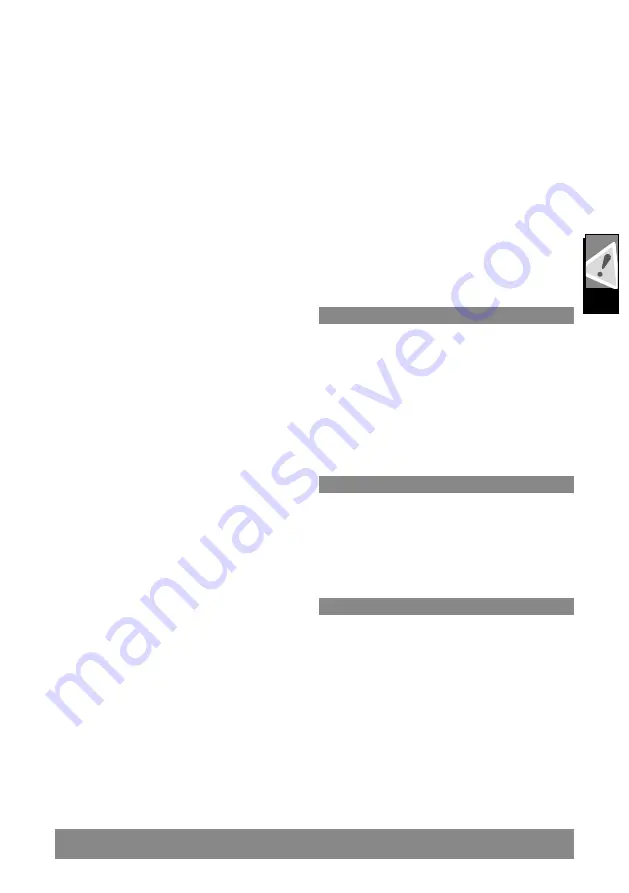
13
13
I
VIII
English
e) Always use undamaged wheel flanges that are of correct
size and shape for your selected wheel.
Proper wheel flanges
support the wheel thus reducing the possibility of wheel breakage.
Flanges for cut-off wheels may be different from grinding wheel
flanges.
f) Do not use worn down wheels from larger power tools.
Wheel intended for larger power tool is not suitable for the higher
speed of a smaller tool and may burst.
Additional Safety Warnings Specific for Abrasive Cutting-Off
Operations:
a) Do not “jam” the cut-off wheel or apply excessive pressure.
Do not attempt to make an excessive depth of cut.
Overstressing
the wheel increases the loading and susceptibility to twisting or
binding of the wheel in the cut and the possibility of kickback or wheel
breakage.
b) Do not position your body in line with and behind the
rotating wheel.
When the wheel, at the point of operation, is moving
away from your body, the possible kickback may propel the spinning
wheel and the power tool directly at you.
c) When wheel is binding or when interrupting a cut for any
reason, switch off the power tool and hold the power tool
motionless until the wheel comes to a complete stop. Never
attempt to remove the cut-off wheel from the cut while the
wheel is in motion otherwise kickback may occur.
Investigate
and take corrective action to eliminate the cause of wheel binding.
d) Do not restart the cutting operation in the workpiece. Let
the wheel reach full speed and carefully re-enter the cut.
The
wheel may bind, walk up or kickback if the power tool is restarted in
the workpiece.
e) Support panels or any oversized workpiece to minimize the
risk of wheel pinching and kickback.
Large workpieces tend to sag
under their own weight. Supports must be placed under the workpiece
near the line of cut and near the edge of the workpiece on both sides
of the wheel.
f) Use extra caution when making a “pocket cut” into existing
walls or other blind areas.
The protruding wheel may cut gas or
water pipes, electrical wiring or objects that can cause kickback.
Safety Warnings Specific for Sanding Operations:
a) Do not use excessively oversized sanding disc paper.
Follow manufacturers recommendations, when selecting
sanding paper.
Larger sanding paper extending beyond the
sanding pad presents a laceration hazard and may cause snagging,
tearing of the disc or kickback.
Safety Warnings Specific for Wire Brushing Operations:
a) Be aware that wire bristles are thrown by the brush
even during ordinary operation. Do not overstress the wires
by applying excessive load to the brush.
The wire bristles can
easily penetrate light clothing and/or skin.
b) If the use of a guard is recommended for wire brushing,
do not allow any interference of the wire wheel or brush
with the guard.
Wire wheel or brush may expand in diameter due
to work load and centrifugal forces.
Additional Safety and Working Instructions
When grinding metal, flying sparks are produced. Take care that
no persons are endangered. Because of the danger of fire, no
combustible materials should be located in the vicinity (spark flight
zone). Do not use dust extraction.
Avoid flying sparks and sanding dust hit your body.
Never reach into the danger area of the machine when it is running.
Immediately switch off the machine in case of considerable vibra-
tions or if other malfunctions occur. Check the machine in order to
find out the cause.
Under extreme conditions (e.g. smooth-grinding metals with
the arbour and vulcanized fibre grinding wheel), significant
contamination can build up on the inside of the angle grinder. For
safety reasons, in such conditions a ground fault interrupter must
be connected in series. If the ground fault interrupter trips the
machine must be sent for service.
Chips and splinters must not be removed while the machine is
running.
Do not let any metal parts enter the airing slots - danger of short
circuit!
MAINS CONNECTION
Connect only to single-phase AC system voltage as indicated on
the rating plate. It is also possible to connect to sockets without an
earthing contact as the design conforms to safety class II.
Appliances used at many different locations including wet room
and open air must be connected via a residual current device (FI,
RCD, PRCD) of 30mA or less.
Only plug-in when machine is switched off.
Inrush currents cause short-time voltage drops. Under unfavoura-
ble power supply conditions, other equipment may be affected. If
the system impedance of the power supply is lower than 0,2 Ohm,
disturbances are unlikely to occur.
SPECIFIED CONDITIONS OF USE
The angle grinder is intended for grinding and cutting metal, stone
and ceramic materials as well as sanding and wire brushing.
Use the cutting guard from the accessories range for cutting
application.
Please refer to the instructions supplied by the accessory manu-
facturer.
The machine is suitable only for working without water.
WORKING INSTRUCTIONS
For accessories intended to be fitted with threaded hole wheel,
ensure that the thread in the wheel is long enough to accept the
spindle length.
Always use and store the cutting and grinding wheels according to
the manufacturer‘s instructions.
Always use the correct guard for cutting and grinding.
The adjusting nut must be tightened before starting to work with
the machine.
Always use the auxiliary handle.
The workpiece must be fixed if it is not heavy enough to be steady.
Never move the workpiece towards the rotating wheel by hand.
Summary of Contents for 4933451577
Page 1: ...Original instructions AG 13 125 XSPD AGV 13 125 XSPDE AGV 13 115 XSPDE ...
Page 2: ......
Page 3: ......
Page 4: ......
Page 6: ...2 2 I I AGV 13 125 XSPDE AGV 13 115 XSPDE AG 13 125 XSPD ...
Page 7: ...3 3 I II 1 2 4 3 2 1 ...
Page 8: ...4 4 I III 0 0 30 30 60 60 60 60 30 30 6 0 6 0 30 30 6 0 6 0 0 0 30 30 ...
Page 9: ...5 5 I IV 2 1 3 6 mm 6 mm 4 ...
Page 10: ...6 6 I IV 3 2 1 ...
Page 12: ...8 8 I VI TIP 30 30 ...
Page 13: ...9 9 I VII 1 2 1 2 Accessory ...
Page 14: ...10 10 I VII 1 2 2 1 Accessory ...