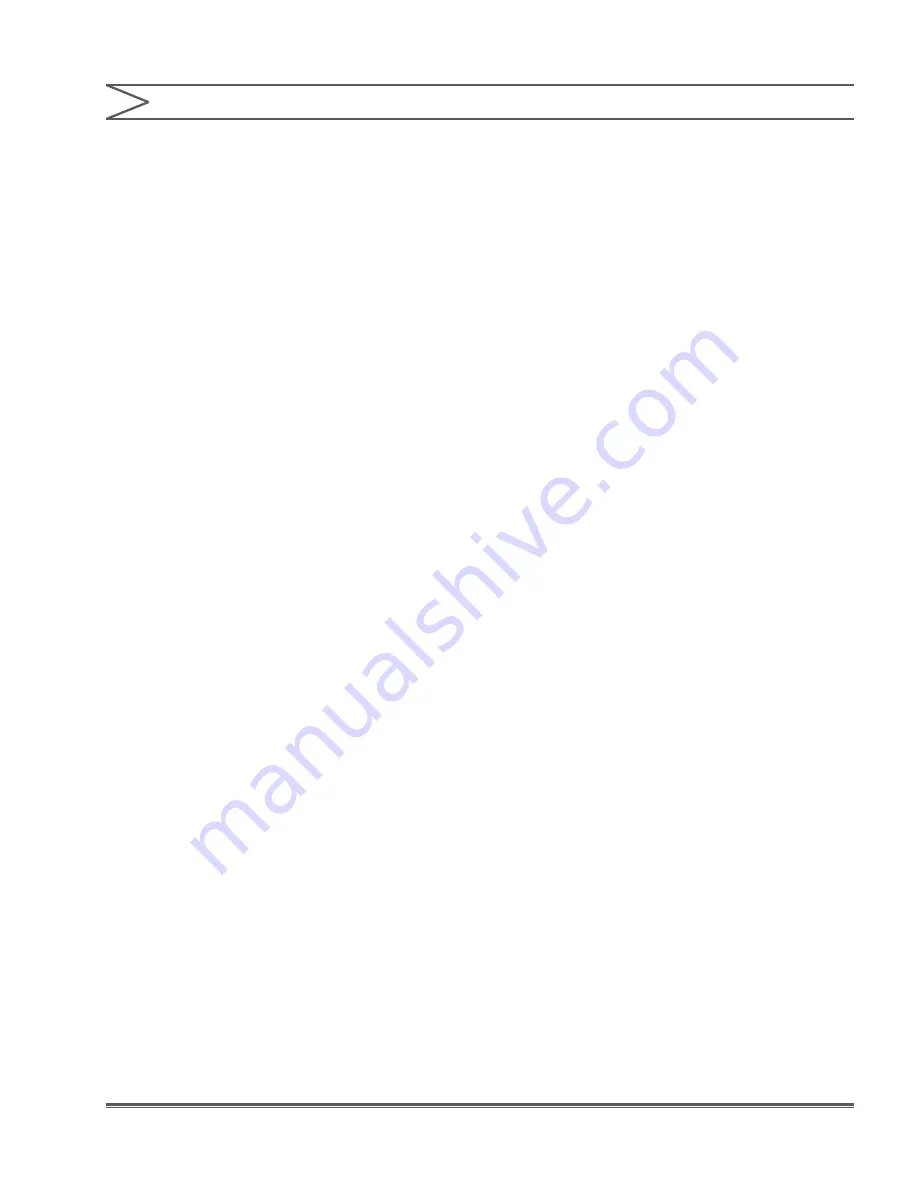
13
Instruction Manual
SECTION 3 - OPERATION
3.2.2 Relief Valve Adjustment (Without an
Adjustable System Back Pressure Valve).
If no adjustable back pressure valve is present
in the discharge line, use the following simplified
procedure to check and/or set the relief valve
setting.
1. If pump is in a relief condition at normal
operating pressure, the relief valve setting
should be increased. Remove valve cover (850)
and increase relief valve setting by turning the
adjustment screw (890) clockwise until only a
few drops of oil escape on each pump stroke
(normal leakage past air bleed ball) (970).
Turn adjustment screw an additional ½ turn to
provide an adequate buffer zone. Lock-in relief
valve setting by tightening locking nut (900)
while holding adjustment screw (890) stationary.
The relief valve is now properly adjusted.
Reinstall valve cover (850).
2. If pump is not in a relief condition at normal
operating pressure, and the operator wishes
to reset the valve setting to approximately 15%
above operating pressure(recommended),
use the following procedure. Remove valve
cover (850) and decrease the relief valve
setting by turning the adjustment screw (890)
counterclockwise until a stream of oil flows
from the drain tube (640) on each pump stroke.
Now slowly turn adjustment screw clockwise
until only a few drops of oil escape on each
pump stroke (normal leakage past air bleed
ball). Turn screw an additional ½ turn to provide
an adequate buffer zone. Lock-in relief valve
setting by tightening locking nut (900) while
holding adjustment screw (890) stationary.
The relief valve is now properly adjusted.
Reinstall valve cover (850).
3.3 USE OF AIR PURGE BUTTON
Refer to Figure 7 & 8
:
As with any hydraulically actuated diaphragm
pump, dissolved air will come out of solution
during normal operation which can negatively
impact pump performance if not removed
from the pump displacement chamber.
The MILROYAL
®
G hydraulic 3- function valve is
equipped with two mechanisms for removal of this
gas: a continuous air bleed and an air purge button.
The continuous air bleed portion of the valve is
composed of a sealed ball (970) which allows for a
controlled leakage of a few drops of oil, and any small
accumulations of evolved gas, on each pump stroke.
Larger quantities of air can be quickly removed by
pressing the spring-loaded purge button (860), until
it reaches its mechanical stop, for a few seconds.
Upon doing so, the operator will observe a stream
of oil and air escaping from the drain tube (640).
The need for use of the purge button to remove
a large quantity of air can be caused by several
factors:
1. Blocked suction line: A partially or fully blocked
suction line can create a vacuum pressure
condition in the hydraulic system which pulls
significant quantities of dissolved gas from
solution.
2. Oil Change: The recommended annual
changing of the oil in the pump drive can lead to
the presence of air pockets in the displacement
chamber (600).
3. Diaphragm Replacement: Results in significant
loss of oil from the displacement chamber.
4. Pump Start- up After Long Idle Period: If the
pump has sat idle for a significant time, gas
may come out of solution from the oil and collect
into pockets which can negatively impact pump
flow. Depression of the purge button will quickly
evacuate these pockets and restore the pump
to desired performance.