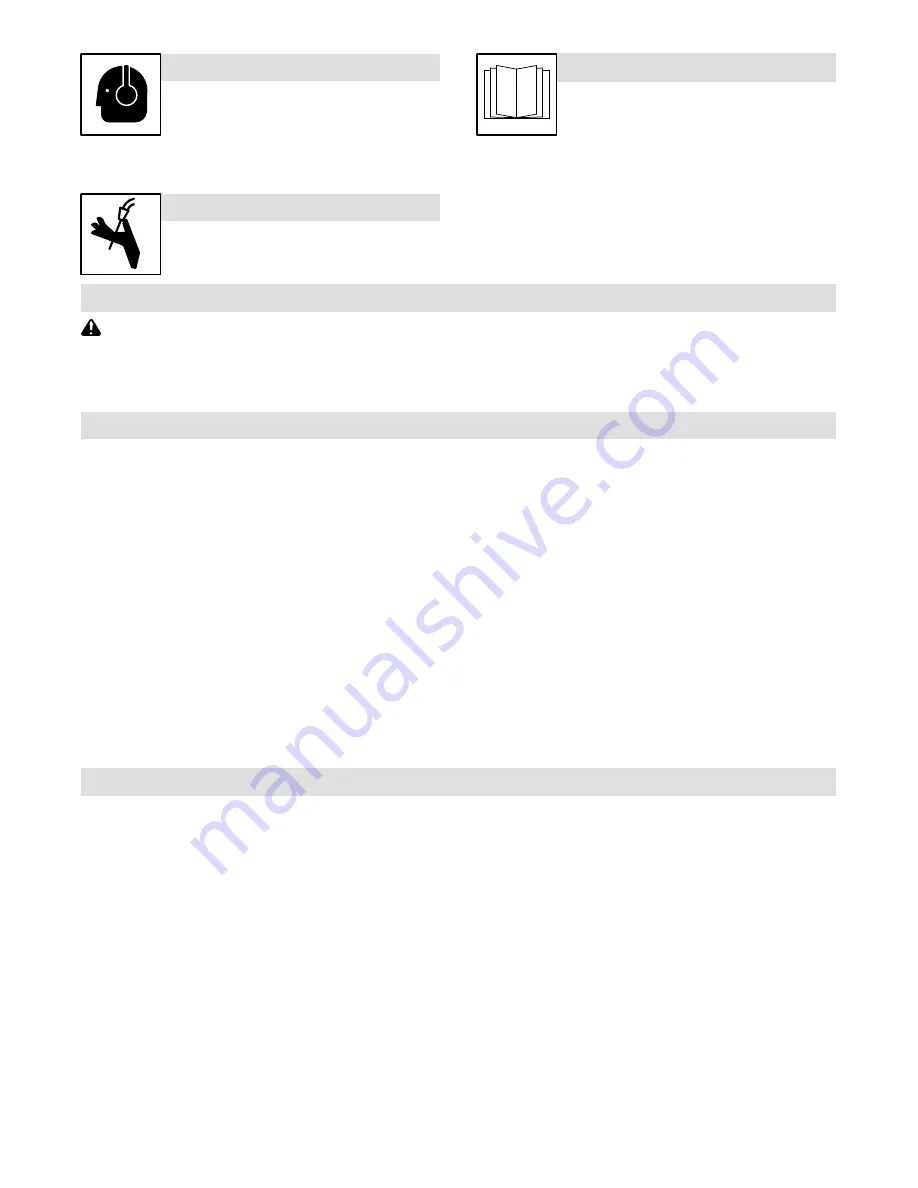
OM-227398 Page 2
NOISE can damage hearing.
Noise from some processes or equipment can
damage hearing.
D
Check for noise level limits exceeding those
specified by OSHA.
D
Use approved ear plugs or ear muffs if noise level is high.
D
Warn others nearby about noise hazard.
WELDING WIRE can injure.
D
Keep hands and body away from gun tip when
trigger is pressed.
READ INSTRUCTIONS.
D
Read and follow all labels and the Owner’s
Manual carefully before installing, operating, or
servicing unit. Read the safety information at
the beginning of the manual and in each
section.
D
Use only genuine replacement parts from the manufacturer.
D
Perform installation, maintenance, and service according to the
Owner’s Manuals, industry standards, and national, state, and
local codes.
1-3.
Proposition 65 Warnings
WARNING: This product can expose you to chemicals in-
cluding lead, which are known to the state of California to
cause cancer and birth defects or other reproductive
harm.
For more information, go to www.P65Warnings.ca.gov.
1-4.
Principal Safety Standards
Safety in Welding, Cutting, and Allied Processes, ANSI Standard Z49.1,
is available as a free download from the American Welding Society at
http://www.aws.org or purchased from Global Engineering Documents
(phone: 1-877-413-5184, website: www.global.ihs.com).
Safe Practice For Occupational And Educational Eye And Face Protec-
tion, ANSI Standard Z87.1, from American National Standards Institute,
25 West 43rd Street, New York, NY 10036 (phone: 212-642-4900, web-
site: www.ansi.org).
Safe Practices for the Preparation of Containers and Piping for Welding
and Cutting, American Welding Society Standard AWS F4.1, from Glob-
al Engineering Documents (phone: 1-877-413-5184, website: www.glo-
bal.ihs.com).
Safe Practices for Welding and Cutting Containers that have Held Com-
bustibles, American Welding Society Standard AWS A6.0, from Global
Engineering Documents (phone: 1-877-413-5184,
website: www.global.ihs.com).
National Electrical Code, NFPA Standard 70, from National Fire Protec-
tion Association, Quincy, MA 02169 (phone: 1-800-344-3555, website:
www.nfpa.org and www. sparky.org).
Safe Handling of Compressed Gases in Cylinders, CGA Pamphlet P-1,
from Compressed Gas Association, 14501 George Carter Way, Suite
103, Chantilly, VA 20151 (phone: 703-788-2700, website:
www.cganet.com).
Safety in Welding, Cutting, and Allied Processes, CSA Standard
W117.2, from Canadian Standards Association, Standards Sales, 5060
Spectrum Way, Suite 100, Mississauga, Ontario, Canada L4W 5NS
(phone: 800-463-6727, website: www.csagroup.org).
Safe Practice For Occupational And Educational Eye And Face Protec-
tion, ANSI Standard Z87.1, from American National Standards Institute,
25 West 43rd Street, New York, NY 10036 (phone: 212-642-4900, web-
site: www.ansi.org).
Standard for Fire Prevention During Welding, Cutting, and Other Hot
Work, NFPA Standard 51B, from National Fire Protection Association,
Quincy, MA 02169 (phone: 1-800-344-3555, website: www.nfpa.org).
OSHA, Occupational Safety and Health Standards for General Indus-
try, Title 29, Code of Federal Regulations (CFR), Part 1910.177 Subpart
N, Part 1910 Subpart Q, and Part 1926, Subpart J, from U.S. Govern-
ment Printing Office, Superintendent of Documents, P.O. Box 371954,
Pittsburgh, PA 15250-7954 (phone: 1-866-512-1800) (there are 10 OS-
HA Regional Offices—phone for Region 5, Chicago, is 312-353-2220,
website: www.osha.gov).
1-5.
EMF Information
Electric current flowing through any conductor causes localized electric
and magnetic fields (EMF). The current from arc welding (and allied pro-
cesses including spot welding, gouging, plasma arc cutting, and induc-
tion heating operations) creates an EMF field around the welding circuit.
EMF fields can interfere with some medical implants, e.g. pacemakers.
Protective measures for persons wearing medical implants have to be
taken. For example, restrict access for passers−by or conduct individu-
al risk assessment for welders. All welders should use the following pro-
cedures in order to minimize exposure to EMF fields from the welding
circuit:
1.
Keep cables close together by twisting or taping them, or using a
cable cover.
2.
Do not place your body between welding cables. Arrange cables
to one side and away from the operator.
3.
Do not coil or drape cables around your body.
4.
Keep head and trunk as far away from the equipment in the
welding circuit as possible.
5.
Connect work clamp to workpiece as close to the weld as
possible.
6.
Do not work next to, sit or lean on the welding power source.
7.
Do not weld whilst carrying the welding power source or wire
feeder.
About Implanted Medical Devices:
Implanted Medical Device wearers should consult their doctor and the
device manufacturer before performing or going near arc welding, spot
welding, gouging, plasma arc cutting, or induction heating operations.
If cleared by your doctor, then following the above procedures is recom-
mended.
Summary of Contents for XR-AlumaPro Series
Page 38: ...Notes...