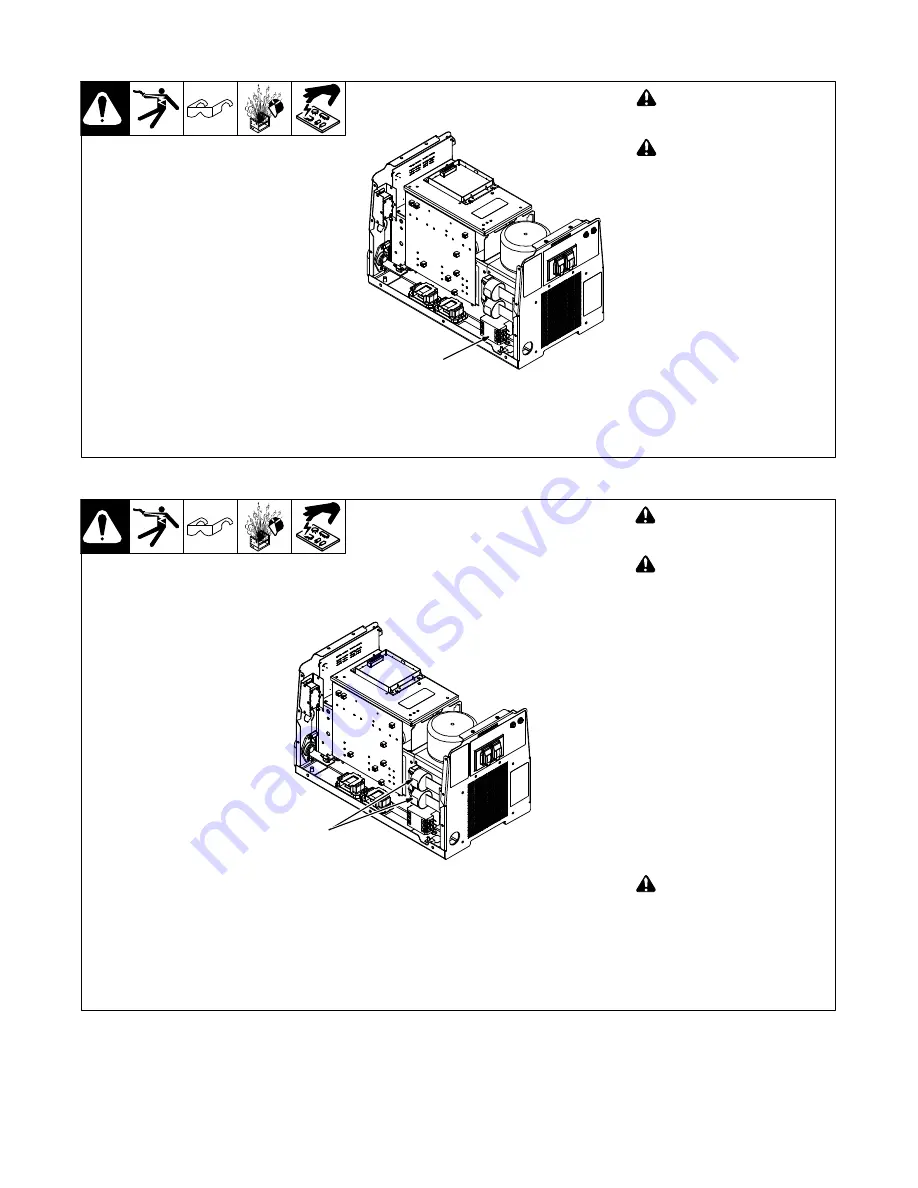
PRE-POWER CHECKS
TM-257 220 Page 43
XMT 450 CC/CV
10-7. Input Contactor W1
255 761-A
!
Read and follow safety
information in Section 10-1
before proceeding.
!
Wear an earth grounded
wrist strap when performing
pre-power and power off
checks. Remove wrist strap
before performing any
checks or procedures with
power applied to the ma-
chine.
1
Verify normally-open contacts
of W1 are not stuck shut by
measuring with DVM set to
ohms.
2
Check resistance of W1 coil.
It should measure
approximately 7 ohms.
Input Contactor W1
10-8. Tank Capacitors C1, C2
Ref. 255 761-A
!
Read and follow safety
information in Section 10-1
before proceeding.
!
Wear an earth grounded
wrist strap when performing
pre-power and power off
checks. Remove wrist strap
before performing any
checks or procedures with
power applied to the ma-
chine.
1
Verify C1 and C2 are not
shorted by measuring with
DVM set to ohms.
.
This is not a conclusive test.
For best results, use a
capacitor tester to check
capacitance.
2
Check capacitance of C1 and
C2. They are in parallel and
should measure
approximately .68
μ
F.
Disconnect lead at
interconnect PC2 for proper
measurement.
!
Pre-power checks are now
complete. Remove earth
grounded wrist strap before
performing any checks or
procedures with power ap-
plied to the machine.
Tank Capacitors C1, C2
Summary of Contents for XMT 450 CC
Page 4: ......
Page 68: ...TM 257 220 Page 64 XMT 450 CC CV Notes...
Page 71: ...TM 257 220 Page 67 XMT 450 CC CV 256 909 A...
Page 73: ...TM 257 220 Page 69 XMT 450 CC CV 256 916 C...
Page 75: ...TM 257 220 Page 71 XMT 450 CC CV 256 916 C...
Page 76: ...TM 257 220 Page 72 XMT 450 CC CV Notes...
Page 83: ...Notes...