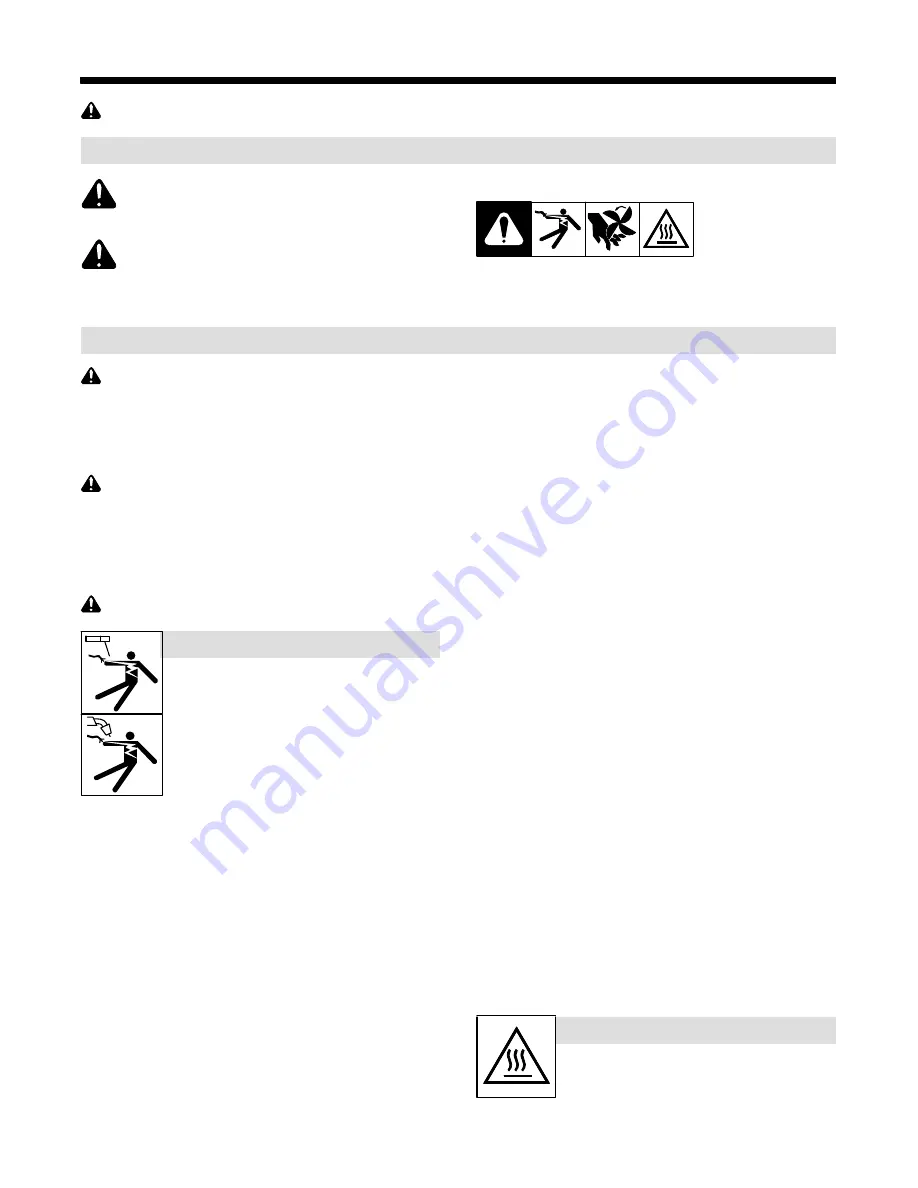
OM-2208 Page 1
SECTION 1
−
SAFETY PRECAUTIONS - READ BEFORE USING
som 2018
−
01
7
Protect yourself and others from injury —
read, follow, and save these important safety precautions and operating instructions.
1-1. Symbol Usage
DANGER!
−
Indicates a hazardous situation which, if
not avoided, will result in death or serious injury. The
possible hazards are shown in the adjoining symbols
or explained in the text.
Indicates a hazardous situation which, if not avoided,
could result in death or serious injury. The possible
hazards are shown in the adjoining symbols or ex-
plained in the text.
NOTICE
−
Indicates statements not related to personal injury.
.
Indicates special instructions.
This group of symbols means Warning! Watch Out! ELECTRIC
SHOCK, MOVING PARTS, and HOT PARTS hazards. Consult sym-
bols and related instructions below for necessary actions to avoid the
hazards.
1-2. Arc Welding Hazards
The symbols shown below are used throughout this manual
to call attention to and identify possible hazards. When you
see the symbol, watch out, and follow the related instructions
to avoid the hazard. The safety information given below is
only a summary of the more complete safety information
found in the Safety Standards listed in Section 1-5. Read and
follow all Safety Standards.
Only qualified persons should install, operate, maintain, and
repair this equipment. A qualified person is defined as one
who, by possession of a recognized degree, certificate, or
professional standing, or who by extensive knowledge, train-
ing and experience, has successfully demonstrated ability to
solve or resolve problems relating to the subject matter, the
work, or the project and has received safety training to recog-
nize and avoid the hazards involved.
During operation, keep everybody, especially children, away.
Touching live electrical parts can cause fatal shocks
or severe burns. The electrode and work circuit is
electrically live whenever the output is on. The input
power circuit and machine internal circuits are also
live when power is on. In semiautomatic or automatic
wire welding, the wire, wire reel, drive roll housing,
and all metal parts touching the welding wire are
electrically live. Incorrectly installed or improperly
grounded equipment is a hazard.
D
Do not touch live electrical parts.
ELECTRIC SHOCK can kill.
D
Wear dry, hole-free insulating gloves and body protection.
D
Insulate yourself from work and ground using dry insulating mats
or covers big enough to prevent any physical contact with the work
or ground.
D
Do not use AC weld output in damp, wet, or confined spaces, or if
there is a danger of falling.
D
Use AC output ONLY if required for the welding process.
D
If AC output is required, use remote output control if present on
unit.
D
Additional safety precautions are required when any of the follow-
ing electrically hazardous conditions are present: in damp
locations or while wearing wet clothing; on metal structures such
as floors, gratings, or scaffolds; when in cramped positions such
as sitting, kneeling, or lying; or when there is a high risk of unavoid-
able or accidental contact with the workpiece or ground. For these
conditions, use the following equipment in order presented: 1) a
semiautomatic DC constant voltage (wire) welder, 2) a DC manual
(stick) welder, or 3) an AC welder with reduced open-circuit volt-
age. In most situations, use of a DC, constant voltage wire welder
is recommended. And, do not work alone!
D
Disconnect input power or stop engine before installing or
servicing this equipment. Lockout/tagout input power according to
OSHA 29 CFR 1910.147 (see Safety Standards).
D
Properly install, ground, and operate this equipment according to
its Owner’s Manual and national, state, and local codes.
D
Always verify the supply ground
−
check and be sure that input
power cord ground wire is properly connected to ground terminal in
disconnect box or that cord plug is connected to a properly
grounded receptacle outlet.
D
When making input connections, attach proper grounding conduc-
tor first
−
double-check connections.
D
Keep cords dry, free of oil and grease, and protected from hot metal
and sparks.
D
Frequently inspect input power cord and ground conductor for
damage or bare wiring – replace immediately if damaged – bare
wiring can kill.
D
Turn off all equipment when not in use.
D
Do not use worn, damaged, undersized, or repaired cables.
D
Do not drape cables over your body.
D
If earth grounding of the workpiece is required, ground it directly
with a separate cable.
D
Do not touch electrode if you are in contact with the work, ground,
or another electrode from a different machine.
D
Do not touch electrode holders connected to two welding ma-
chines at the same time since double open-circuit voltage will be
present.
D
Use only well-maintained equipment. Repair or replace damaged
parts at once. Maintain unit according to manual.
D
Wear a safety harness if working above floor level.
D
Keep all panels and covers securely in place.
D
Clamp work cable with good metal-to-metal contact to workpiece
or worktable as near the weld as practical.
D
Insulate work clamp when not connected to workpiece to prevent
contact with any metal object.
D
Do not connect more than one electrode or work cable to any
single weld output terminal. Disconnect cable for process not in
use.
D
Use GFCI protection when operating auxiliary equipment in damp
or wet locations.
SIGNIFICANT DC VOLTAGE exists in inverter weld-
ing power sources AFTER removal of input power.
D
Turn off unit, disconnect input power, and discharge input capaci-
tors according to instructions in Manual before touching any parts.
HOT PARTS can burn.
D
Do not touch hot parts bare handed.
D
Allow cooling period before working on
equipment.
D
To handle hot parts, use proper tools and/or wear heavy, insu-
lated welding gloves and clothing to prevent burns.
Summary of Contents for XMT 304
Page 4: ......
Page 21: ...OM 2208 Page 17 Notes...
Page 33: ...OM 2208 Page 29 Notes...
Page 38: ...Notes...