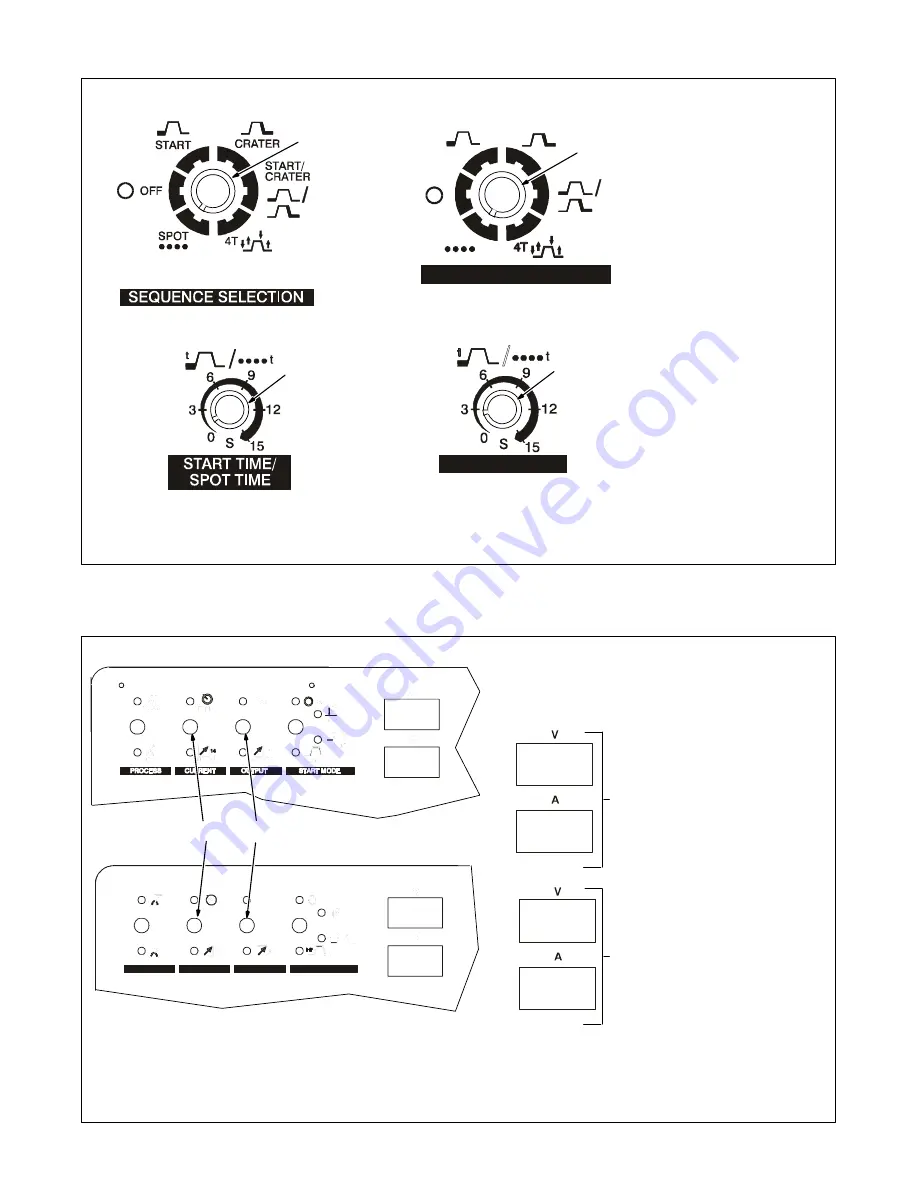
OM-356 Page 35
5-19. Spot Time Control
1
Sequence Selection Switch −
Spot Position
Used with the (GTAW) TIG Spot
process, generally with a direct cur-
rent electrode negative (DCEN) set-
up.
2
Start Time/Spot Time Control
Use control to select 0−15 seconds
of spot time.
Use Amperage Adjust control (see
Section 5-8) to set amperage.
Application:
TIG spot welding is used for joining
thinner materials that are in close
contact, with the fusion method. A
good example would be joining coil
ends.
1
2
2
1
(CE Nameplate Only)
5-20. Timer/Cycle Counter
1
Current Control
2
Output (Contactor) Control
To read timer/cycle counter, hold
Current and Output (contactor) but-
tons while turning on power.
3
Timer Display
The hours and minutes are dis-
played on the volt and amp meters
for the first five seconds, and are
read as 1, 234 hours and 56 min-
utes.
4
Cycle Display
The cycles are displayed on the volt
and amp meters for the next five
seconds, and are read as 123, 456
cycles.
1
2
(CE Nameplate Only)
1 2 3
4 5 6
1 2 3
4 5 6
3
4