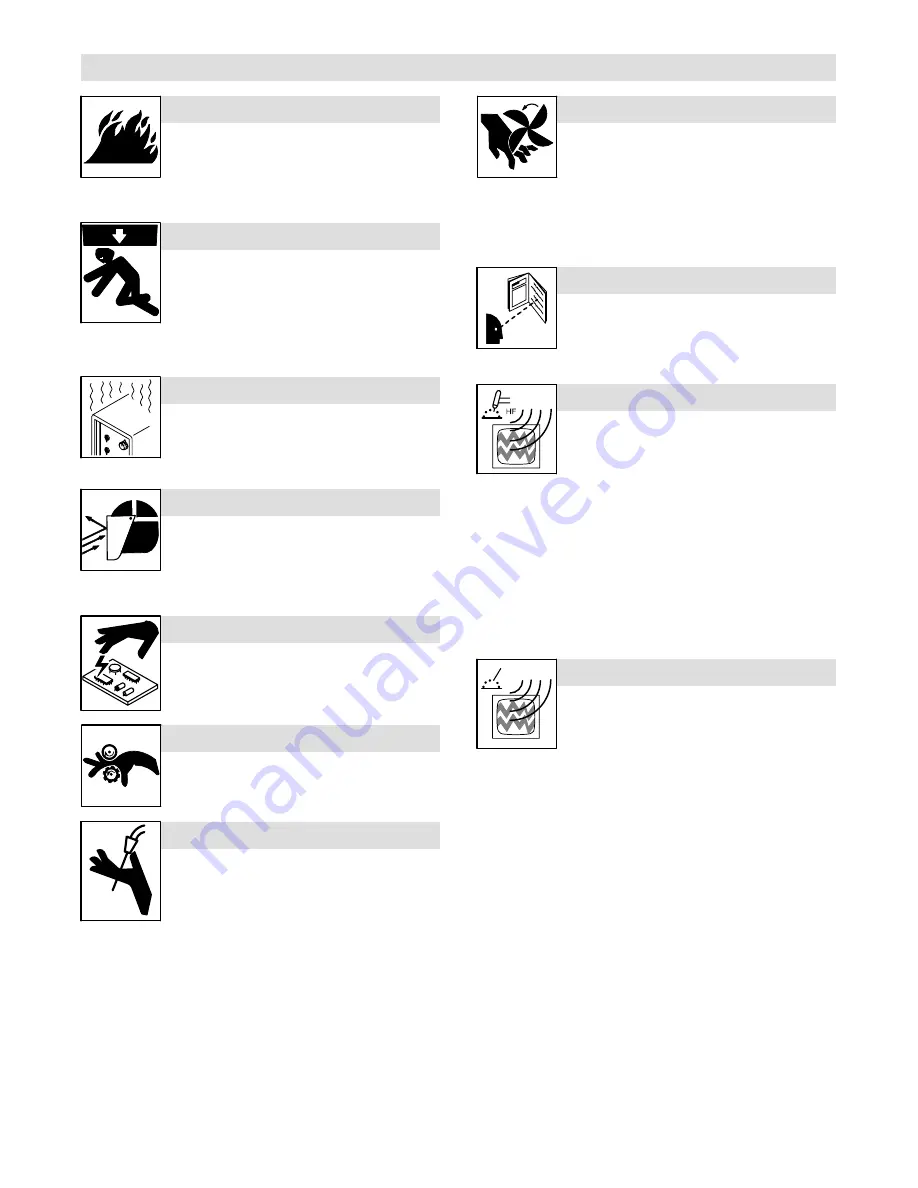
OM-238 172 Page 3
1-3. Additional Symbols For Installation, Operation, And Maintenance
FIRE OR EXPLOSION hazard.
D
Do not install or place unit on, over, or near
combustible surfaces.
D
Do not install unit near flammables.
D
Do not overload building wiring
−
be sure power supply system is
properly sized, rated, and protected to handle this unit.
FALLING UNIT can cause injury.
D
Use lifting eye to lift unit only, NOT running
gear, gas cylinders, or any other accessories.
D
Use equipment of adequate capacity to lift and
support unit.
D
If using lift forks to move unit, be sure forks are
long enough to extend beyond opposite side of
unit.
OVERUSE can cause OVERHEATING
D
Allow cooling period; follow rated duty cycle.
D
Reduce current or reduce duty cycle before
starting to weld again.
D
Do not block or filter airflow to unit.
FLYING SPARKS can cause injury.
D
Wear a face shield to protect eyes and face.
D
Shape tungsten electrode only on grinder with
proper guards in a safe location wearing proper
face, hand, and body protection.
D
Sparks can cause fires — keep flammables away.
STATIC (ESD) can damage PC boards.
D
Put on grounded wrist strap BEFORE handling
boards or parts.
D
Use proper static-proof bags and boxes to
store, move, or ship PC boards.
MOVING PARTS can cause injury.
D
Keep away from moving parts.
D
Keep away from pinch points such as drive
rolls.
WELDING WIRE can cause injury.
D
Do not press gun trigger until instructed to do
so.
D
Do not point gun toward any part of the body,
other people, or any metal when threading
welding wire.
MOVING PARTS can cause injury.
D
Keep away from moving parts such as fans.
D
Keep all doors, panels, covers, and guards
closed and securely in place.
D
Have only qualified persons remove doors, panels, covers, or
guards for maintenance as necessary.
D
Reinstall doors, panels, covers, or guards when maintenance is
finished and before reconnecting input power.
READ INSTRUCTIONS.
D
Read Owner’s Manual before using or servic-
ing unit.
D
Use only genuine replacement parts from the
manufacturer.
H.F. RADIATION can cause interference.
D
High-frequency (H.F.) can interfere with radio
navigation, safety services, computers, and
communications equipment.
D
Have only qualified persons familiar with
electronic equipment perform this installation.
D
The user is responsible for having a qualified electrician prompt-
ly correct any interference problem resulting from the installa-
tion.
D
If notified by the FCC about interference, stop using the
equipment at once.
D
Have the installation regularly checked and maintained.
D
Keep high-frequency source doors and panels tightly shut, keep
spark gaps at correct setting, and use grounding and shielding to
minimize the possibility of interference.
ARC WELDING can cause interference.
D
Electromagnetic energy can interfere with
sensitive electronic equipment such as
computers and computer-driven equipment
such as robots.
D
Be sure all equipment in the welding area is
electromagnetically compatible.
D
To reduce possible interference, keep weld cables as short as
possible, close together, and down low, such as on the floor.
D
Locate welding operation 100 meters from any sensitive elec-
tronic equipment.
D
Be sure this welding machine is installed and grounded
according to this manual.
D
If interference still occurs, the user must take extra measures
such as moving the welding machine, using shielded cables,
using line filters, or shielding the work area.
Summary of Contents for ST-24 ce
Page 14: ...OM 238 172 Page 10...
Page 33: ...Notes...