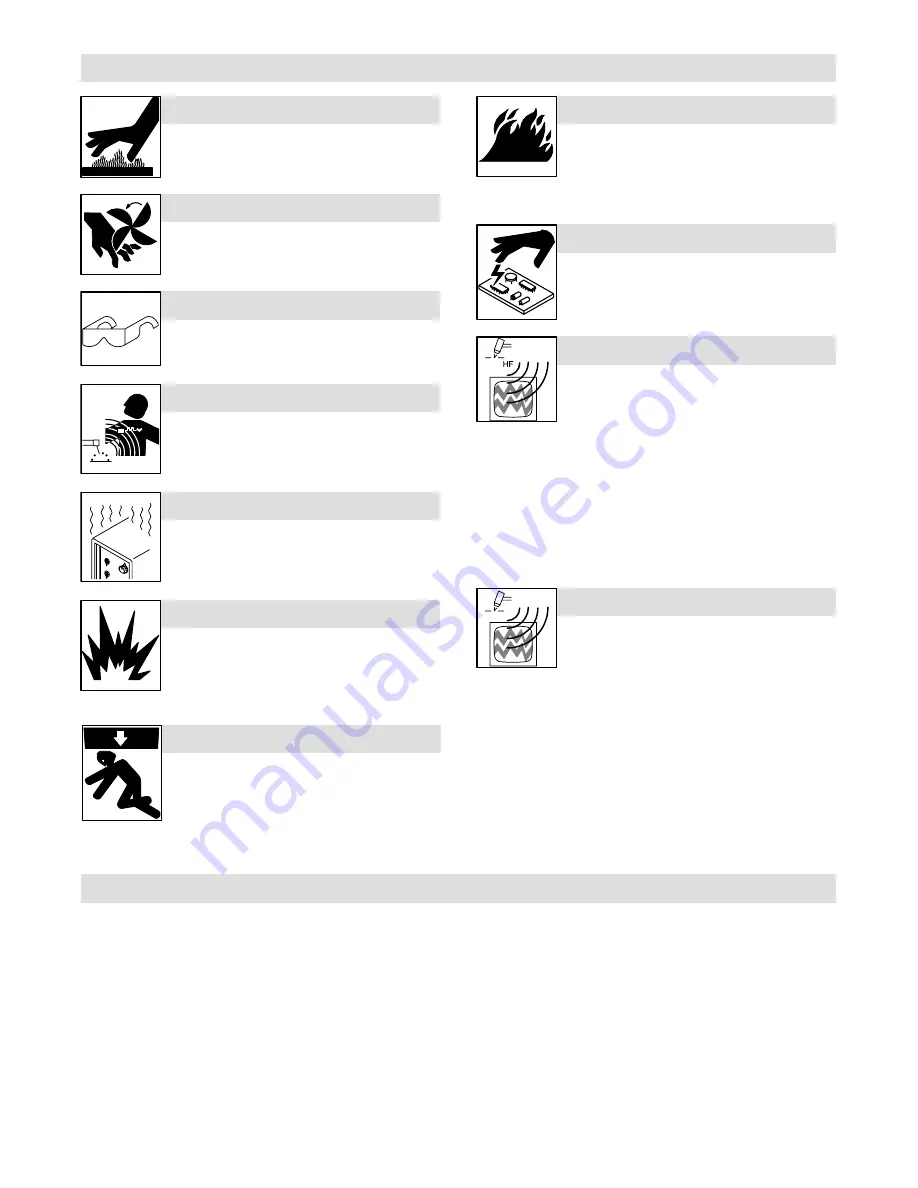
OM-2219 Page 3
1-3.
Additional Symbols For Installation, Operation, And Maintenance
HOT PARTS can cause severe burns.
D
Do not touch hot parts bare handed.
D
Allow cooling period before working on torch.
MOVING PARTS can cause injury.
D
Keep away from moving parts such as fans.
D
Keep all doors, panels, covers, and guards
closed and securely in place.
FLYING METAL can injure eyes.
D
Wear safety glasses with side shields or face
shield.
MAGNETIC FIELDS can affect pacemakers
.
D
Pacemaker wearers keep away.
D
Wearers should consult their doctor before go-
ing near plasma arc cutting operations.
OVERUSE can cause OVERHEATING.
D
Allow cooling period; follow rated duty cycle.
D
Reduce amperage (thickness) or reduce duty
cycle before starting to cut again.
EXPLODING HYDROGEN hazard.
D
When cutting aluminum underwater or with the
water touching the underside of the aluminum,
free hydrogen gas may collect under the work-
piece.
D
See your cutting engineer and water table instructions for help.
FALLING UNIT can cause injury.
D
Use lifting eye to lift unit only, NOT running
gear, gas cylinders, or any other accessories.
D
Use equipment of adequate capacity to lift unit.
D
If using lift forks to move unit, be sure forks are long enough to ex-
tend beyond opposite side of unit.
FIRE OR EXPLOSION hazard.
D
Do not locate unit on, over, or near combustible
surfaces.
D
Do not install unit near flammables.
D
Do not overload building wiring − be sure power supply system is
properly sized, rated, and protected to handle this unit.
STATIC (ESD) can damage PC boards.
D
Put on grounded wrist strap BEFORE handling
boards or parts.
D
Use proper static-proof bags and boxes to
store, move, or ship PC boards.
H.F. RADIATION can cause interference.
D
High frequency (H.F.) can interfere with radio
navigation, safety services, computers, and
communications equipment.
D
Have only qualified persons familiar with elec-
tronic equipment perform this installation.
D
The user is responsible for having a qualified electrician promptly
correct any interference problem resulting from the installation.
D
If notified by the FCC about interference, stop using the equipment
at once.
D
Have the installation regularly checked and maintained.
D
Keep high-frequency source doors and panels tightly shut, keep
spark gaps at correct setting, and use grounding and shielding to
minimize the possibility of interference.
ARC CUTTING can cause interference.
D
Electromagnetic energy can interfere with
sensitive electronic equipment such as
computers and computer-driven equipment
such as robots.
D
To reduce possible interference, keep cables as short as possible,
close together, and down low, such as on the floor.
D
Locate cutting operation 100 meters from any sensitive electronic
equipment.
D
Be sure this cutting power source is installed and grounded
according to this manual.
D
If interference still occurs, the user must take extra measures such
as moving the machine, using shielded cables, using line filters, or
shielding the work area.
1-4.
Principal Safety Standards
Safety in Welding and Cutting, ANSI Standard Z49.1, from American
Welding Society, 550 N.W. LeJeune Rd, Miami FL 33126
Safety and Health Standards, OSHA 29 CFR 1910, from Superinten-
dent of Documents, U.S. Government Printing Office, Washington, D.C.
20402.
Recommended Practices for Plasma Arc Cutting, American Welding
Society Standard AWS C5.2, from American Welding Society, 550 N.W.
LeJeune Rd, Miami, FL 33126
Recommended Safe Practices for the Preparation for Welding and Cut-
ting of Containers That Have Held Hazardous Substances, American
Welding Society Standard AWS F4.1, from American Welding Society,
550 N.W. LeJeune Rd, Miami, FL 33126
National Electrical Code, NFPA Standard 70, from National Fire Protec-
tion Association, Batterymarch Park, Quincy, MA 02269.
Safe Handling of Compressed Gases in Cylinders, CGA Pamphlet P-1,
from Compressed Gas Association, 1235 Jefferson Davis Highway,
Suite 501, Arlington, VA 22202.
Code for Safety in Welding and Cutting, CSA Standard W117.2, from
Canadian Standards Association, Standards Sales, 178 Rexdale Bou-
levard, Rexdale, Ontario, Canada M9W 1R3.
Safe Practices For Occupation And Educational Eye And Face Protec-
tion, ANSI Standard Z87.1, from American National Standards Institute,
1430 Broadway, New York, NY 10018.
Cutting And Welding Processes, NFPA Standard 51B, from National
Fire Protection Association, Batterymarch Park, Quincy, MA 02269.
Summary of Contents for Spectrum Lynx
Page 4: ......