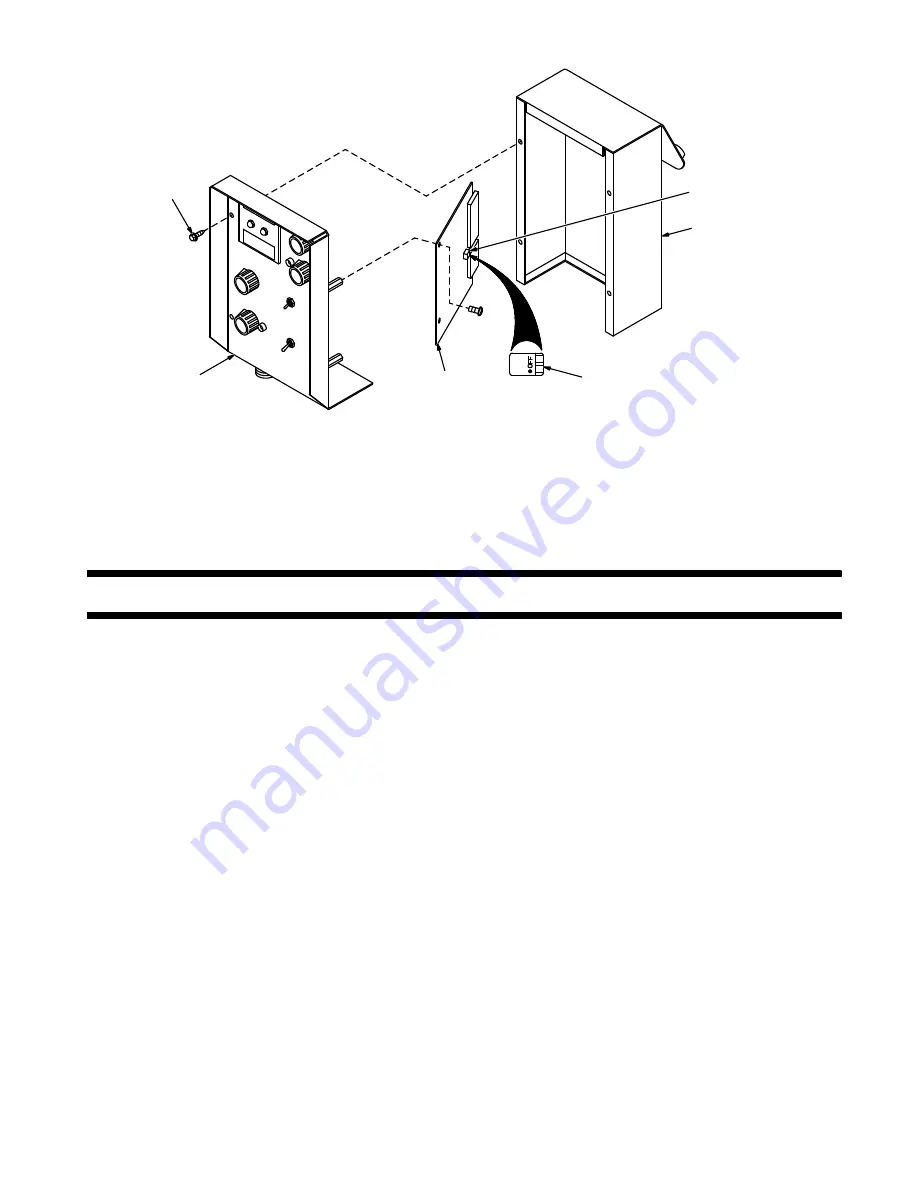
OM-533 Page 3
ST-113 509-A
Mounting
Screws (5)
Front
Panel
Cover
Dip
Switch
Circuit
Board
PC5
Both dip switches down for
1000 ampere model operation
Both dip switches up for
650 ampere model operation
Figure 2-2. Dip Switch Positions And Locations
SECTION 3 – OPERATOR CONTROLS
3-1. MODE SELECTOR SWITCH (Figure 3-1)
The Mode Selector switch allows selection of CC
(constant current), CV (constant voltage), or pulsed out-
put from the welding power source.
The CC position provides a constant current output spe-
cifically designed for Shielded Metal Arc (SMAW) and
Gas Tungsten Arc (GTAW) Welding processes. The CC
position is also normally used for Air Carbon Arc Cutting
(CAC-A) and gouging processes.
The CV position provides a constant voltage output de-
signed for wire feeding applications such as Gas Metal
Arc (GMAW), Flux Cored Arc (FCAW), or Submerged
Arc (SAW) Welding.
When pulsed output is desired for Gas Metal Arc Weld-
ing - Pulsed Arc (GMAW-P), place switch at the desired
number of pulses per second: 60, 90, 120 or 180.
3-2. ARC CONTROL AND PILOT LIGHT (Figure 3-1)
IMPORTANT:
The ARC CONTROL potentiometer and
pilot light are disabled in the CV (Constant Voltage) and
pulsed modes.
The ARC CONTROL potentiometer provides variable
selection of short-circuit current to suit individual weld-
ing conditions. Rotating this control clockwise causes
the current to increase as the short-circuit condition is
approached. When this control is set at some value
above 0, the current begins to increase when arc volt-
age drops below 20 volts.
When the control is set at 10 (MAX.), the short-circuit
current is considerably higher than normal welding cur-
rent (see welding power source volt-ampere curve for
CC mode). This provides extra current for arc starting in
out-of-position welds as well as for certain types of elec-
trodes.
When the control is set at 0 (SOFT), short-circuit current
is the same as normal welding current. The 0 position
provides current characteristics associated with the Gas
Tungsten Arc Welding (GTAW) process.
When the control is set at 5, short-circuit current is
approximately half that of the 10 (MAX.) position but still
higher than normal welding current. The 5 position pro-
vides a moderate current increase for arc starting nec-
essary for certain types of electrodes and applications.
Select a setting best suited for the application.
The Arc Control pilot light turns on when the Mode Se-
lector switch is in the CC position indicating that the ARC
CONTROL is active.
IMPORTANT:
The ARC CONTROL can be adjusted
while welding.