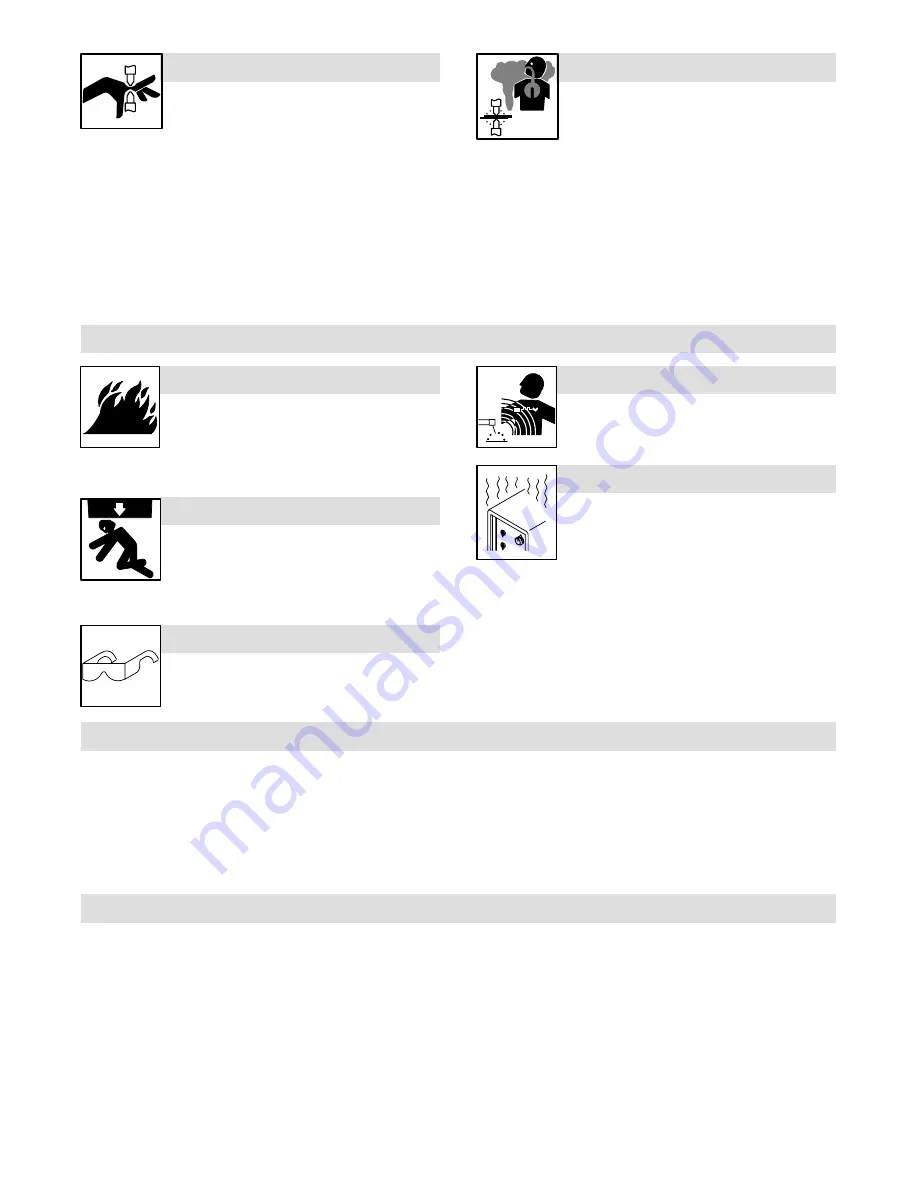
OM-708 Page 2
The tong tips, tongs, and linkages move during
operation.
MOVING PARTS can cause injury.
D
Keep away from moving parts.
D
Keep away from pinch points.
D
Do not put hands between tips.
D
Keep all guards and panels securely in place.
FUMES can be hazardous.
Coatings, cleaners, paints, and platings can pro-
duce fumes when welded. Breathing these fumes
can be hazardous to your health.
D
Do not breathe the fumes.
D
If inside, ventilate the area and/or use exhaust at the weld to remove
fumes.
D
In confined spaces, use an approved air-supplied respirator.
D
Do not weld on coated metals, such as galvanized, lead, or cad-
mium plated steel, unless the coating is removed from the weld
area, the area is well ventilated, or if necessary, while wearing an
air-supplied respirator. The coatings and any metals containing
these elements can give off toxic fumes if welded.
D
Read the Material Safety Data Sheets (MSDSs) and the manufac-
turer’s instructions for metals, coatings, and cleaners.
1-3.
Additional Symbols for Installation, Operation, and Maintenance
FIRE OR EXPLOSION hazard.
D
Do not install or place unit on, over, or near
combustible surfaces.
D
Do not install or operate unit near flammables.
D
Do not overload building wiring – be sure power supply system is
properly sized, rated, and protected to handle this unit.
FALLING EQUIPMENT can cause injury.
D
Use equipment of adequate capacity to lift the
unit.
D
Have two people of adequate physical strength
lift portable units.
D
Secure unit during transport so it cannot tip or fall.
FLYING METAL or DIRT can injure eyes.
D
Wear approved safety glasses with side
shields or wear face shield.
MAGNETIC FIELDS can affect pacemakers
.
D
Pacemaker wearers keep away.
D
Wearers should consult their doctor before go-
ing near resistance spot welding operations.
OVERUSE can cause OVERHEATING.
D
Allow cooling period; follow rated duty cycle.
D
Reduce duty cycle before starting to weld
again.
1-4.
Principal Safety Standards
Safety in Welding and Cutting, ANSI Standard Z49.1, from American
Welding Society, 550 N.W. LeJeune Rd, Miami FL 33126
Safety and Health Standards, OSHA 29 CFR 1910, from Superinten-
dent of Documents, U.S. Government Printing Office, Washington, D.C.
20402.
National Electrical Code, NFPA Standard 70, from National Fire Protec-
tion Association, Batterymarch Park, Quincy, MA 02269.
Code for Safety in Welding and Cutting, CSA Standard W117.2, from
Canadian Standards Association, Standards Sales, 178 Rexdale Bou-
levard, Rexdale, Ontario, Canada M9W 1R3.
Safe Practices For Occupation And Educational Eye And Face Protec-
tion, ANSI Standard Z87.1, from American National Standards Institute,
1430 Broadway, New York, NY 10018.
Cutting And Welding Processes, NFPA Standard 51B, from National
Fire Protection Association, Batterymarch Park, Quincy, MA 02269.
1-5.
EMF Information
Considerations About Welding And The Effects Of Low Frequency
Electric And Magnetic Fields
Welding current will cause electromagnetic fields. There has been and
still is some concern about such fields. However, after examining more
than 500 studies spanning 17 years of research, a special blue ribbon
committee of the National Research Council concluded that: “The body
of evidence, in the committee’s judgment, has not demonstrated that
exposure to power-frequency electric and magnetic fields is a human-
health hazard.” However, studies are still going forth and evidence
continues to be examined.