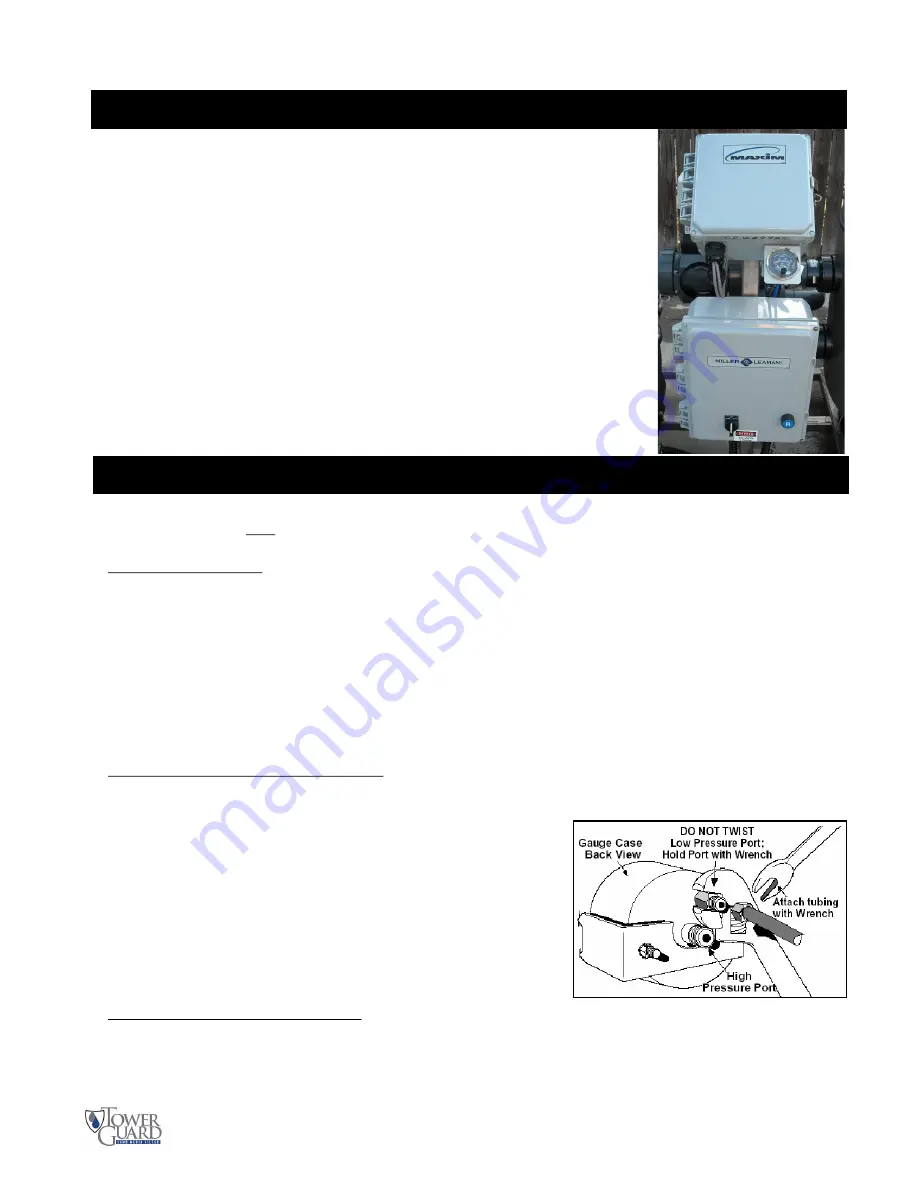
13
MAXIM - State-of-the-art Filter Backflush Controller
The TowerGuard Filter System is controlled by the
MAX IM,
a state-of-the-art
backflush controller designed for automatic filtration systems. The heart of the
MAXIM
is a programmable micro PLC, custom designed to maximize the per-
formance of your filtration system. These components are protected by a robust,
corrosion-proof watertight enclosure.
The
MAX IM
is operated and adjusted through the user-friendly menu screens
that give the user control of all critical automatic filter functions. The backlit
LCD display provides real-time system status. The controller includes a
memory module (EEPROM) port that allows for installation of system upgrades
and provides the ability to download custom, application specific programs
without the need for a computer.
Introduction
Installation
The
MAX IM
controller is pre-installed as a component of the complete TowerGuard filtration system. Follow
the directions below only if it is necessary to connect electrical or gauge connections.
Electrical Connections:
The Maxim controller is pre-wired as part of the Automatic TowerGuard Filter System.
Note:
When using an exter nal power sour ce, the input power to the PC Board must be the same as indi-
cated on the upper left side of the Maxim Controller. Typically, the controller is either 24 volts AC, or 24
volts DC, however some controllers use 120 volts AC or 12 volts DC.
Additional connections to the Outputs should be made to the corresponding
Output (+)
and a
Common (-)
ter-
minal on the circuit board. The Pressure Differential Gauge and Timer ON Enable inputs are connected to a
corresponding Input and Auxiliary Power Out (+) terminal on the Maxim circuit board.
Review the
Electrical Detail
section prior to making any connections to the controller. If requested custom in-
put/output capabilities are not described in this manual, please refer to an attached addendum.
Differential Pressure Gauge Connections:
Connect the pressure differential (PD) gauge to the system’s inlet (high/BLK) and outlet (low/BLU) pressure
ports.
WARNING:
Failur e to use a second wr ench on the low pr essur e
port when tightening fittings may result in damage to the internal
pressure tubing.
Be sure all connection tubing is clean prior to installation on the
gauge. The gauge contains orifices that may become clogged by
larger particles.
CAUTION:
Make sure not to foul the pr essur e or ifices with
pipe dope or dirt, as the gauge will not operate.
Differential Pressure Gauge Set-point:
Adjust the front face needle contact to the desired PD set-point that will trigger a backflush cycle. The recom-
mended PD setpoint is 8-10 PSID above the “clean” gauge reading at the systems MAXIMUM flow rate. Set-
ting this gauge at low flow may result in continuous backflushing at higher flow rates, since the Pressure Dif-
ferential increases with flow rate. Typical PD gauge setpoints are between 12-15 PSID, depending on the flow
rate. Initial factory PD Gauge setting is 12 PSID.