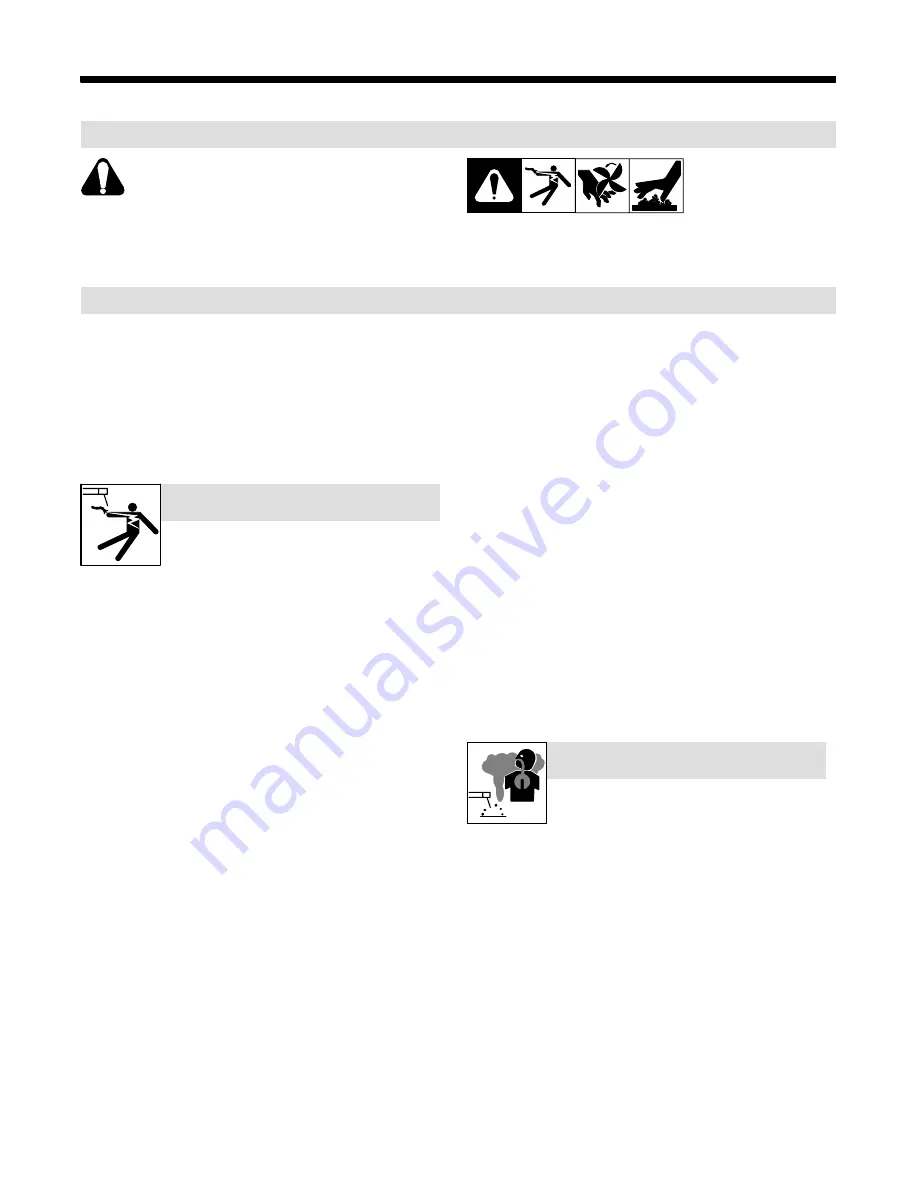
OM-2233 Page 5
SECTION 2
−
CONSIGNES DE SÉCURITÉ
−
LIRE AVANT UTILISATION
fre_som _3/05
Avertissement : se protéger et protéger les autres contre le risque de blessure — lire et respecter ces consignes.
2-1.
Symboles utilisés
Symbole graphique d’avertissement ! Attention ! Cette pro-
cédure comporte des risques possibles ! Les dangers éven-
tuels sont représentés par les symboles graphiques joints.
Indique un message de sécurité particulier
Signifie NOTE ; n’est pas relatif à la sécurité.
Ce groupe de symboles signifie Avertissement ! Attention ! Risques
d’ÉLECTROCUTION, ORGANES MOBILES et PARTIES
CHAUDES. Consulter les symboles et les instructions afférentes
ci-dessous concernant les mesures à prendre pour supprimer
les dangers.
2-2.
Dangers relatifs au soudage à l’arc
Les symboles représentés ci-dessous sont utilisés dans ce manuel
pour attirer l’attention et identifier les dangers possibles. En
présence de l’un de ces symboles, prendre garde et suivre les
instructions afférentes pour éviter tout risque. Les instructions en
matière de sécurité indiquées ci-dessous ne constituent qu’un
sommaire des instructions de sécurité plus complètes fournies
dans les normes de sécurité énumérées dans la Section 2-5. Lire et
observer toutes les normes de sécurité.
Seul un personnel qualifié est autorisé à installer, faire fonction-
ner, entretenir et réparer cet appareil.
Pendant le fonctionnement, maintenir à distance toutes les per-
sonnes, notamment les enfants de l’appareil.
UNE DÉCHARGE ÉLECTRIQUE peut
entraîner la mort.
Le contact d’organes électriques sous tension peut
provoquer des accidents mortels ou des brûlures
graves. Le circuit de l’électrode et de la pièce est
sous tension lorsque le courant est délivré à la
sortie. Le circuit d’alimentation et les circuits internes de la machine
sont également sous tension lorsque l’alimentation est sur Marche.
Dans le mode de soudage avec du fil, le fil, le dérouleur, le bloc de
commande du rouleau et toutes les parties métalliques en contact
avec le fil sont sous tension électrique. Un équipement installé ou mis
à la terre de manière incorrecte ou impropre constitue un danger.
Ne pas toucher aux pièces électriques sous tension.
Porter des gants isolants et des vêtements de protection secs et sans
trous.
S’isoler de la pièce à couper et du sol en utilisant des housses ou des
tapis assez grands afin d’éviter tout contact physique avec la pièce à
couper ou le sol.
Ne pas se servir de source électrique à courant électrique dans les zo-
nes humides, dans les endroits confinés ou là où on risque de tomber.
Se servir d’une source électrique à courant électrique UNIQUEMENT si
le procédé de soudage le demande.
Si l’utilisation d’une source électrique à courant électrique s’avère né-
cessaire, se servir de la fonction de télécommande si l’appareil en est
équipé.
D’autres consignes de sécurité sont nécessaires dans les conditions
suivantes : risques électriques dans un environnement humide ou si l’on
porte des vêtements mouillés ; sur des structures métalliques telles que
sols, grilles ou échafaudages ; en position coincée comme assise, à ge-
noux ou couchée ; ou s’il y a un risque élevé de contact inévitable ou
accidentel avec la pièce à souder ou le sol. Dans ces conditions, utiliser
les équipements suivants, dans l’ordre indiqué : 1) un poste à souder DC
à tension constante (à fil), 2) un poste à souder DC manuel (électrode)
ou 3) un poste à souder AC à tension à vide réduite. Dans la plupart des
situations, l’utilisation d’un poste à souder DC à fil à tension constante
est recommandée. En outre, ne pas travailler seul !
Couper l’alimentation ou arrêter le moteur avant de procéder
à l’installation, à la réparation ou à l’entretien de l’appareil. Déverrouiller
l’alimentation selon la norme OSHA 29 CFR 1910.147 (voir normes de
sécurité).
Installer le poste correctement et le mettre à la terre convenablement
selon les consignes du manuel de l’opérateur et les normes nationales,
provinciales et locales.
Toujours vérifier la terre du cordon d’alimentation. Vérifier et s’assurer
que le fil de terre du cordon d’alimentation est bien raccordé à la borne
de terre du sectionneur ou que la fiche du cordon est raccordée à une
prise correctement mise à la terre.
En effectuant les raccordements d’entrée, fixer d’abord le conducteur
de mise à la terre approprié et contre-vérifier les connexions.
Vérifier fréquemment le cordon d’alimentation afin de s’assurer qu’il
n’est pas altéré ou à nu, le remplacer immédiatement s’il l’est. Un fil à nu
peut entraîner la mort.
L’équipement doit être hors tension lorsqu’il n’est pas utilisé.
Ne pas utiliser des câbles usés, endommagés, de grosseur insuffisante
ou mal épissés.
Ne pas enrouler les câbles autour du corps.
Si la pièce soudée doit être mise à la terre, le faire directement avec un
câble distinct.
Ne pas toucher l’électrode quand on est en contact avec la pièce, la terre
ou une électrode provenant d’une autre machine.
Ne pas toucher des porte électrodes connectés à deux machines en
même temps à cause de la présence d’une tension à vide doublée.
N’utiliser qu’un matériel en bon état. Réparer ou remplacer sur-le-
champ les pièces endommagées. Entretenir l’appareil conformément à
ce manuel.
Porter un harnais de sécurité si l’on doit travailler au-dessus du sol.
S’assurer que tous les panneaux et couvercles sont correctement en
place.
Fixer le câble de retour de façon à obtenir un bon contact métal-métal
avec la pièce à souder ou la table de travail, le plus près possible de la
soudure.
Isoler la pince de masse quand pas mis à la pièce pour éviter le contact
avec tout objet métallique.
Ne pas raccorder plus d’une électrode ou plus d’un câble de masse à
une même borne de sortie de soudage.
Il reste une TENSION DC NON NÉGLIGEABLE dans
les sources de soudage onduleur quand on a coupé
l’alimentation.
Arrêter les convertisseurs, débrancher le courant électrique et
décharger les condensateurs d’alimentation selon les instructions indi-
quées dans la partie Entretien avant de toucher les pièces.
Le soudage génère des fumées et des gaz. Leur
inhalation peut être dangereuse pour la santé.
LES FUMÉES ET LES GAZ peuvent
être dangereux.
Ne pas mettre sa tête au-dessus des vapeurs. Ne pas respirer ces va-
peurs.
À l’intérieur, ventiler la zone et/ou utiliser une ventilation forcée au niveau de
l’arc pour l’évacuation des fumées et des gaz de soudage.
Si la ventilation est médiocre, porter un respirateur anti-vapeurs approu-
vé.
Lire et comprendre les spécifications de sécurité des matériaux (MSDS) et
les instructions du fabricant concernant les métaux, les consommables, les
revêtements, les nettoyants et les dégraisseurs.
Travailler dans un espace fermé seulement s’il est bien ventilé ou en
portant un respirateur à alimentation d’air. Demander toujours à un sur-
veillant dûment formé de se tenir à proximité. Des fumées et des gaz de
soudage peuvent déplacer l’air et abaisser le niveau d’oxygène provo-
quant des blessures ou des accidents mortels. S’assurer que l’air de
respiration ne présente aucun danger.
Ne pas souder dans des endroits situés à proximité d’opérations de dé-
graissage, de nettoyage ou de pulvérisation. La chaleur et les rayons de
l’arc peuvent réagir en présence de vapeurs et former des gaz haute-
ment toxiques et irritants.
Ne pas souder des métaux munis d’un revêtement, tels que l’acier gal-
vanisé, plaqué en plomb ou au cadmium à moins que le revêtement n’ait
été enlevé dans la zone de soudure, que l’endroit soit bien ventilé et en
portant un respirateur à alimentation d’air. Les revêtements et tous les
métaux renfermant ces éléments peuvent dégager des fumées toxi-
ques en cas de soudage.