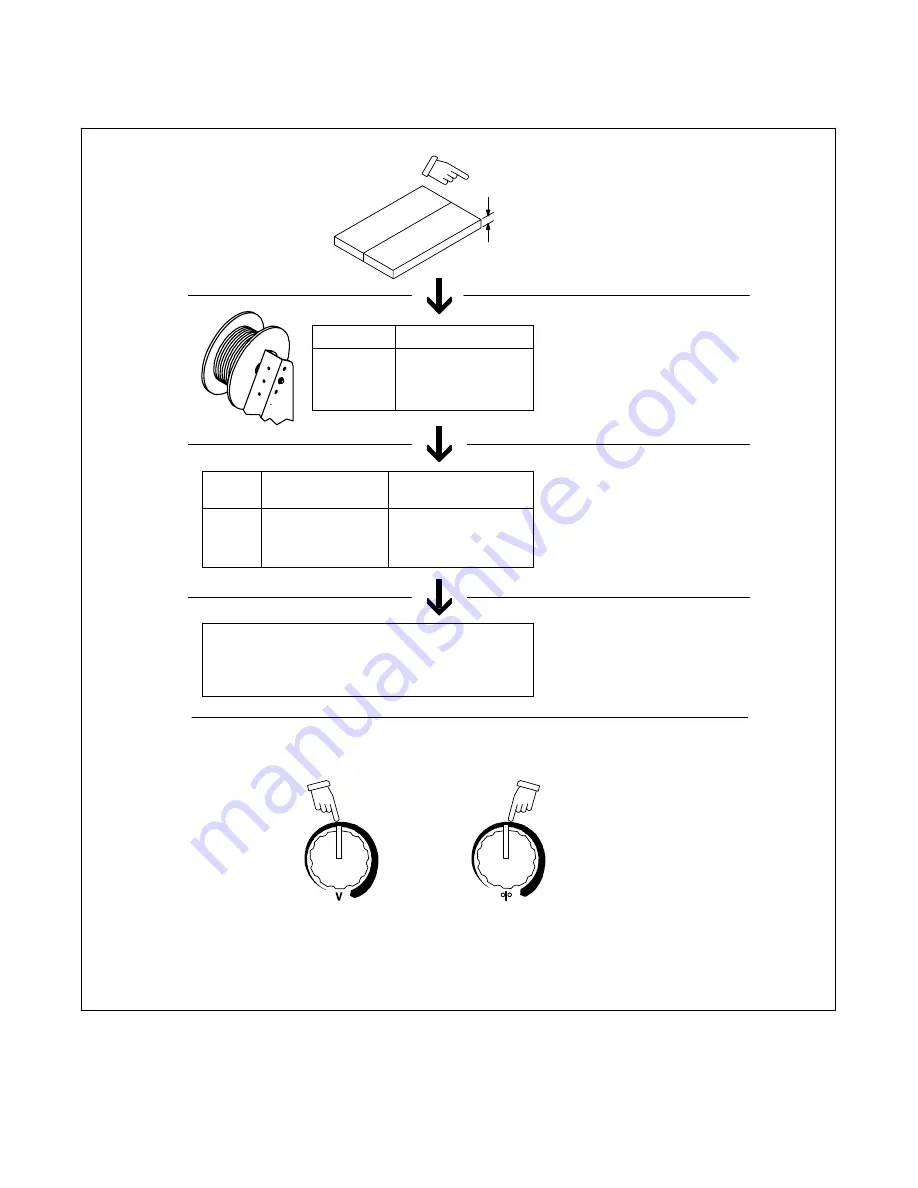
OM-232 386 Page 33
8-2.
Typical MIG Process Control Settings
.
These settings are guidelines only. Material and wire type, joint design, fitup, position, shielding gas, etc. affect settings. Test welds to be sure
they comply to specifications.
3.5 x 125 A = 437 ipm
2 x 125 A = 250 ipm
1.6 x 125 A = 200 ipm
30 − 90 A
40 − 145 A
50 − 180 A
Convert Material
Thickness to
Amperage (A)
Material thickness determines weld
parameters.
.035 in
Recommendation
Wire Speed
(Approx.)
1/8 or 0.125 in
(0.001 in = 1 ampere)
0.125 in = 125 A
Wire Size
Amperage Range
0.023 in
0.030 in
0.035 in
Select Wire Size
Wire
Size
0.023 in
0.030 in
0.035 in
3.5 in per ampere
2 in per ampere
1.6 in per ampere
Select Wire Speed
(Amperage)
125 A based on 1/8 in
material thickness
ipm = inches per minute
Low voltage: wire stubs into work
High voltage: arc is unstable (spatter)
Set voltage midway between high/low voltage
Select Voltage
Voltage controls height and
width of weld bead.
Wire speed (amperage) controls weld
penetration (wire speed = burn-off rate)