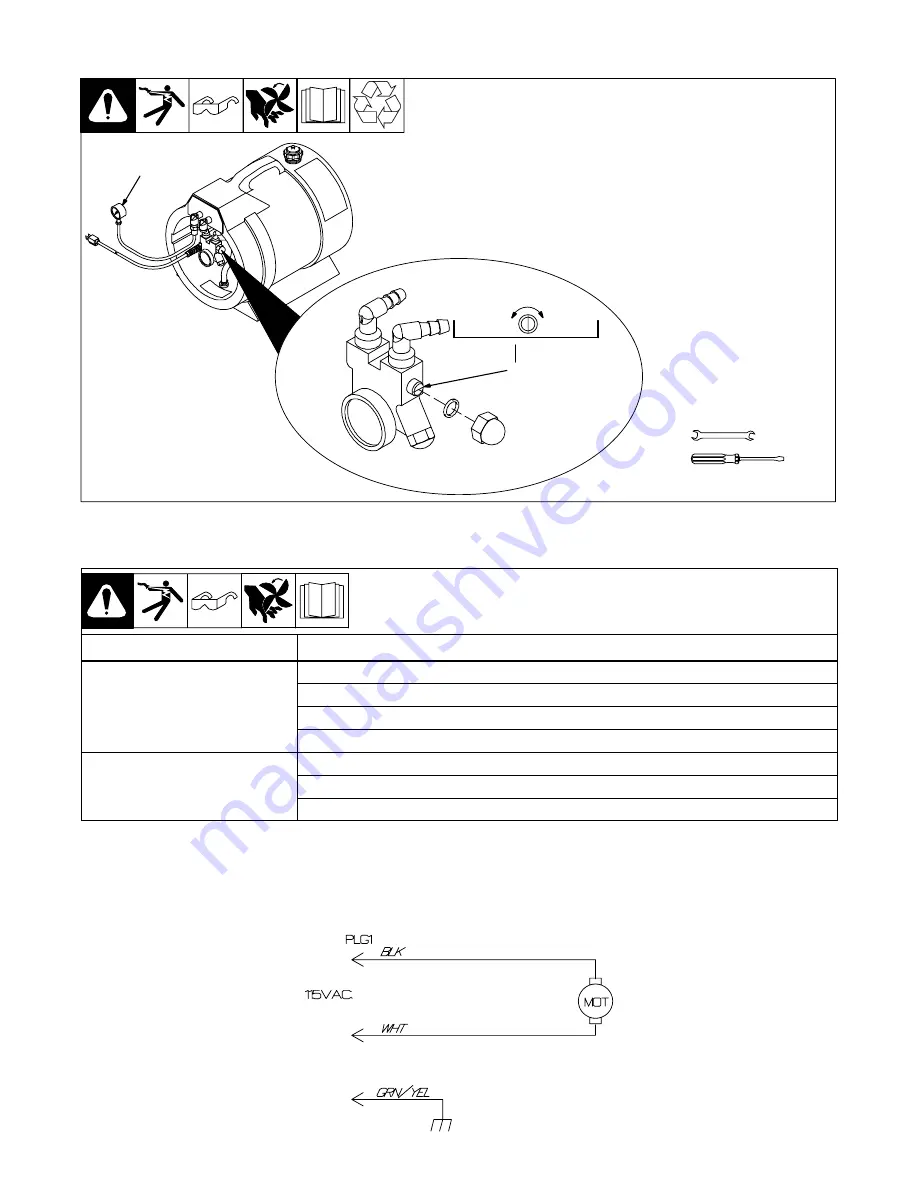
OM-624 Page 7
Tools Needed:
13. Adjusting Relief Valve
160 558-B
.
Relief valve is factory set at 60
psi (414 kPa), and normally
needs no adjustment: Only ad-
just if replacing motor.
1
Pressure gauge
2
Relief Valve Adjustment
Screw
Connect gauge to Coolant Out fit-
ting as shown. Block or plug any
output fitting on gauge.
Turn On power, and adjust pres-
sure adjustment screw as needed.
Turn Off power. Disconnect gauge
and reinstall nut.
3/4 in.
2
1
Increase
Decrease
14. Troubleshooting
Trouble
Remedy
Coolant system does not work.
Be sure input power cord is plugged in to energized receptacle.
Check line fuses or circuit breaker, and replace or reset if necessary.
Motor overheated. Unit starts running when motor has cooled.
Have Factory Authorized Service Agent check motor.
Decreased or no coolant flow.
Add coolant.
Check for clogged hoses or coolant filter.
Disconnect pump, and check for sheared coupling. Replace coupling if necessary.
15. Circuit Diagram
187 313
Summary of Contents for Coolmate Coolmate 4
Page 11: ...Notes ...