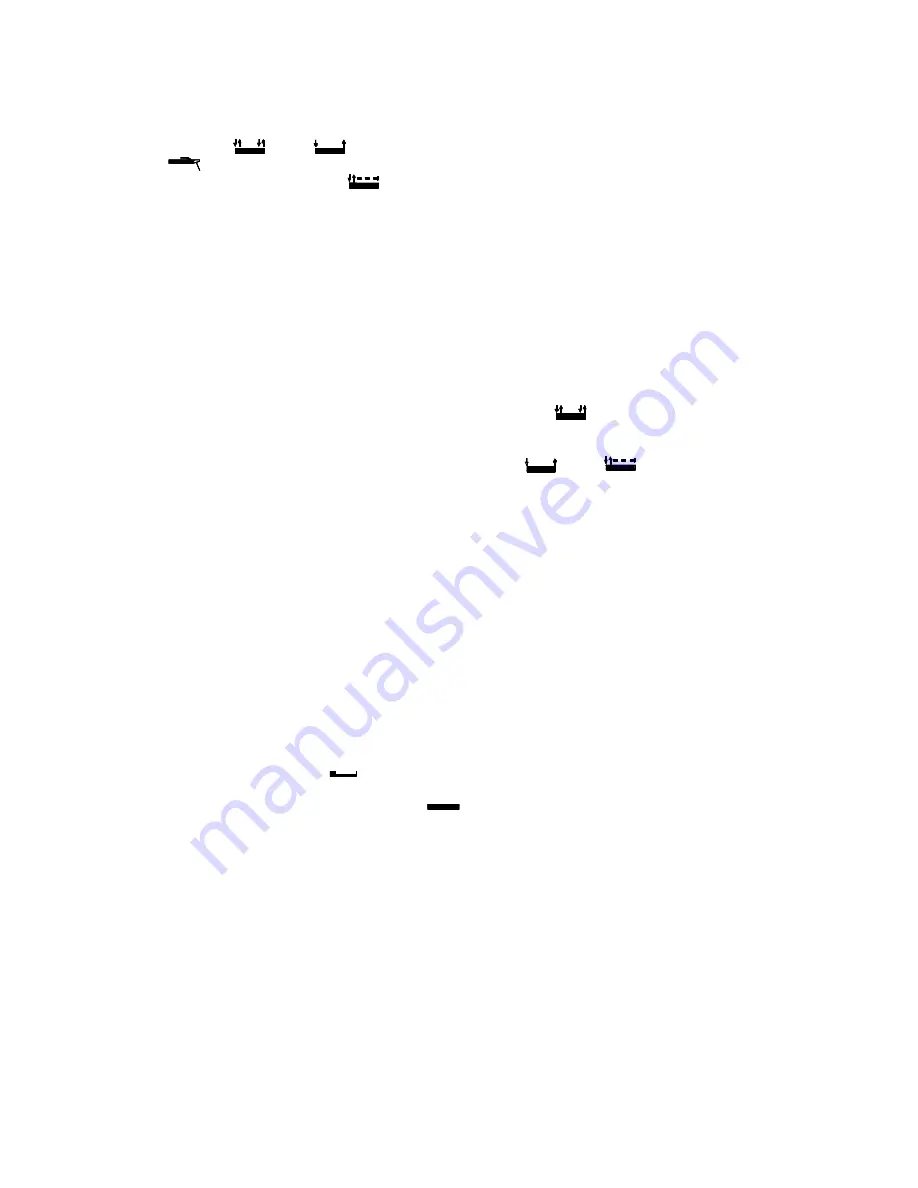
11
ADJUSTMENT FUNCTIONS BOXES
1.
Switch for functions:
Self hold
,
seam
,
electrode welding
. Control boxes of type I are also equipped
with the spot welding function
.
If the switch is set at electrode welding the
"hot-start" and "anti-sticking" automatics are
activated. In the other positions these functions
are automatically cut out.
If the machine is activated by a pressure on the
torch button when it is not welding, the machine
is automatically cut out after approximately 10
sec. (self hold and spot welding).
2.
Overload indicator
The red lamp lights if the automatic thermal
overload protection device has cut out the
machine. The thermostatically controlled fan
continues working until the machine has cooled
to normal temperature, after which the red light
will turn off automatically and the machine is
ready for use.
3.
Ammeter
Shows the set welding current. The machine is
equipped with a very exact electronic circuit
measuring the welding current. On the basis of
the measured and the set current, comparisons
and adjustments are currently made to ensure a
constant welding current irrespectively of
varying mains voltage, cable lengths or machine
heating.
4.
Green control lamp indicating that the solenoid
valve has opened for the shielding gas
5.
HF switch
Only on box type III. Boxes of type I and II have
automatic switch.
If the selector switch is at
, the HF will work
only at the time of ignition and will cut out
automatically when the arc is stable. At
,
the HF striking works during the whole welding
activity. This position is used for AC welding.
During electrode welding the HF striking is
automatically cut out.
6.
AC balance
Button for adjustment of the relation between
cleaning effect and penetration at aluminium
welding. This is done through a regulation of the
positive and negative halfwaves.
A setting at "70" gives the highest penetration
and "45" the highest cleaning effect. At DC wel-
ding the AC balance is set at "50" as this gives
the lowest consumption of mains current. At
type I and II boxes, this happens automatically.
7.
Post-weld gas flow
The post-weld gas flow time should be set in
accordance with the plate thickness and the
diameter of the tungsten electrode to prevent
oxidation of electrode and welding seam when
the welding is ended. The time is correctly set
when there is no temper colour at the end of the
tungsten electrode after the burn-back delay is
over, and a correct setting will extend the life of
the tungsten electrode. The max. post-weld gas
flow time is 30 sec.
8
Slope down control
Crater formation at the end of a weld seam can
be prevented by using this control to set the time
for the welding current to decay after completing
the welding seam. If the switch (pos. 1) is at self
hold
, the slope down works as long as the
torch button is held down and the welding ends
when it is released. If the switch is at seam
or spot
. the welding only stops when
the slope down time has expired.
9.
Set current
The welding current is adjusted by this
potentiometer equipped with a multidrive
reduction.
Control boxes I and II are furthermore equipped
with the following:
10. Multiplug for connection of remote control or
welding robot. Signals for set current, measured
current and "arc established".
11. Remote control switch
Switch between external or internal current
adjustment and for box I furthermore internal
adjustment of pulsatory arc. Machines equipped
with box I or II can also weld with pulsatory arc
by addition of remote control FPB (part no.
76116383). Max. pulse frequency is 16 Hz.
12. Hot start
This control can only be used when electrode
welding.
If this control is set at 100% the machine will
start with a welding current twice as high as the
set main current (pos. 9). This hot-start surge
continues for 1 second after which the machine
automatically drops to the set welding current.
Summary of Contents for MTE DIALOG
Page 2: ......
Page 8: ...8 DEFINITIONS ...
Page 10: ...10 ADJUSTMENT FUNCTIONS BOXES TYPE I TYPE II TYPE III ...
Page 13: ...13 ILLUSTRATION OF CONTROL PROGRAMMES FOR BOX TYPE I ...
Page 14: ...14 ...
Page 28: ...28 CTU 3000 ...